Water treatment methods all require a variety of technologies to meet their targets for the treatment of effluents. The remediation of a LNAPL (light non-aqueous phase liquid) plume may require a treatment train consisting of air strippers, oil-water separators and carbon adsorption systems in order to adhere to discharge conditions.
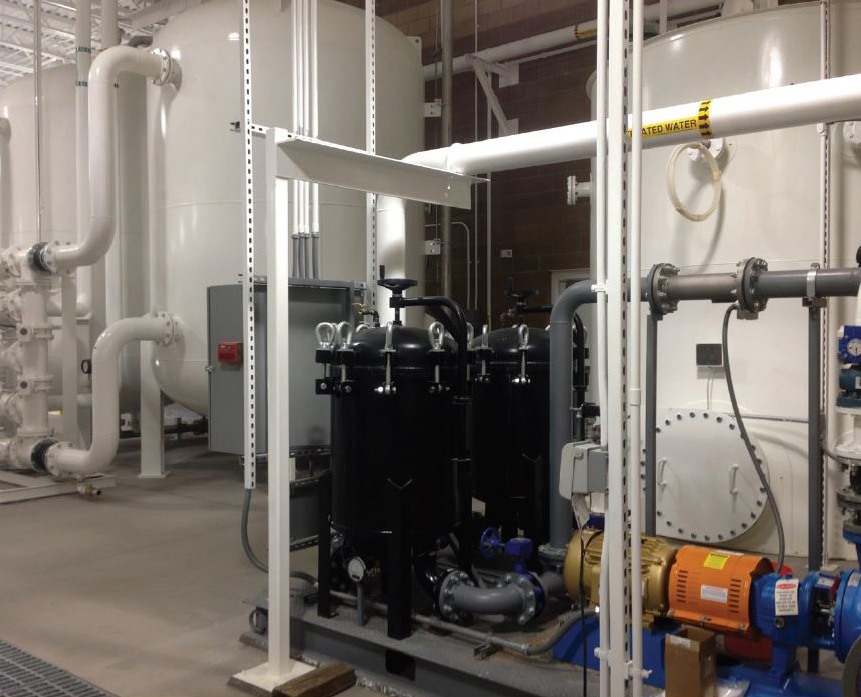
Wastewater Treatment System. Image Credit: Anguil Environmental Systems
It is advisable to factor in other components to protect the primary treatment equipment and ensure efficient and effective operation. These precautions are not targeting at the main contaminants of concern but rather reducing downtime and operating expenses.
For example, the upstream filtration of solids of granular activated carbon (GAC) units will prevent premature GAC fouling. The installation of a cone bottom inlet equalization/feed tank, rather than using the alternative of a flat bottom tank, means that settleable solids can be caught in the cone prior to further treatment.
The cone bottom can be easily accessed to pump out the resultant material without the need to drain the whole tank.
Other examples of protective equipment include:
- Upstream iron removal to reduce oxidation dose requirements
- Use of knock-out pots upstream of oxidizers and vacuum blowers to remove wetness from the process air
- The clarification of semi-volatile organics preceding the air strippers to reduce fouling
- Removal of inorganic material to protect membrane systems from scaling and fouling
- Reducing the risk of scaling in wet scrubbers by using water softening technologies
- Removal of solvents to protect membrane systems
- Removal of grit to reduce pump impeller wearing
It is also important to take the types of construction materials used into consideration, factoring in those which are compatible with water contaminants, as well as evaluating their use in areas where maintenance activities are likely to be carried out.
Painting or coating the mating surfaces of bag filter housings is not advisable. These housings need to be accessed to change bags and baskets, meaning any painted surfaces will chip and crack as a result.
While the use of stainless steel in the initial construction process may lead to an increase in upfront capital cost, the equipment will require less lifetime service, leading to ongoing operational savings.
The layout of equipment should also factor in the need for routine maintenance. For example, pipe runs should not be located across access hatches, while enough clearance space must be allowed to access the trays in low profile air strippers without impediment.
Another factor to take into consideration is the need for large basket strainers to be placed high enough from ground level so that the baskets can be easily removed. Where instruments need to be calibrated on a regular basis, such as pH sensors, for example, it is best to avoid locating these in or pipe runs or elevated ducts.
In the case of pumps, blowers, actuators and belts, appropriate space around routinely maintained areas needs to be factored in as much as possible. This helps ensure that operators will not be working in tight, less safe conditions or above ground level.
Organic and inorganic deposits can lead to high maintenance costs to restore operationality, even resulting in the need to prematurely replace equipment. Inorganic deposits often develop in the form of iron deposition and hardness scale. Struvite precipitation in landfill leachate systems is a common but industry-specific type of deposit.
Bacterial growth can lead to biofouling, which can affect the equipment’s operational capabilities, yet this is frequently overlooked in the initial equipment design process because the influent waters are not characterized appropriately in advance. Waste streams from many food processing plants contain contain fat, grease, or oil in considerable quantities so the process itself can be the source of fouling.
There are a variety of ways in which the deposit of inorganic material can be managed. For example, metals can be deliberately removed, sequestered, so they stay in suspended form or otherwise substituted during the softening process.
Variables such as residence time in the system, flow rate, and discharge requirements will help users to determine the most appropriate process for managing inorganic material. Where the discharge permit has expressed limits for calcium or iron, for example, removal may be necessary.
Where this is not the case, sequestration may be a more suitable option, as it will allow metals to pass through the equipment. This will not only protect the equipment but can also lead to reduced maintenance expenditure.
Bacterial growth has the potential to lead to foul carbon and clog bag filters, yet organic deposit control is often overlooked during the design phase, particularly where pumping and treatment systems are involved.
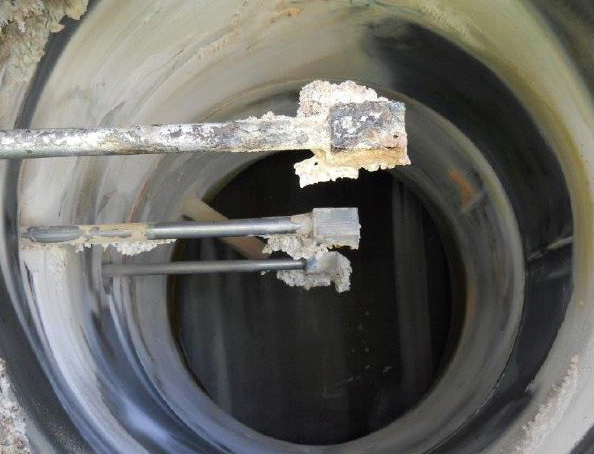
Scrubber Fouled from Calcium and Salt Deposits. Image Credit: Anguil Environmental Systems
There are two main methods of managing bio growth: by disinfection and by removing environmental conditions which promote bacterial growth. Examples of the latter include adjusting redox potential and removing nutrient sources.
Options for disinfection include the addition of sodium hypochlorite, chlorine, biocides, chlorine dioxide and the use of UV radiation. Each of these options brings its own operational issues, often related to concerns around health and safety, chemical handling and management of disinfection by-products.
To ensure maximum levels of protection, ideally, the disinfection process should occur as soon as possible in the system in question. Disinfection can also be used in cases where bio growth is felt to be out of control, as it introduces a sudden shock to the system.
When it comes to long-term management, as well as instances where biofouling needs to be removed, the use of bio dispersants by an injection process should be considered. Dispersants can lead to the removal of food sources, weakened cell walls and inhibition of the reproduction of bacteria.
Bio dispersants are generally safer to utilize than corrosive chemicals and biocides and will not react with the treatment system.
From day one, operators should have a preventative maintenance plan to hand. They should also be cognizant of all the manufacturer’s warranty exclusions and maintenance suggestions, including a comprehensive plan for mechanical controls and electrical checks.
Where the mechanics of the system are concerned, pump alignments need to be validated, integrity checks of gaskets and seals need to be carried out, leaking tanks need to be identified, every moving part needs to be checked for wear and tear, and all process equipment should be checked for organic and inorganic deposits on a routine basis.
In terms of electrical requirements, each control signal needs to be verified, and control panel components, including all system control and switch buttons, should be verified to ensure they are operating correctly.
The control system should be tested to ensure all alarms are operating appropriately; for example, making sure that high and low level switches are tripping correctly, all instruments are properly calibrated, and the sequence of operation remains sound.
Carrying out routine maintenance on a regular basis prevents minor issues from growing into maintenance challenges, leading to operational and maintenance budgets that extend beyond appropriate levels.
Maintenance and operational expenditure in large-scale remediation systems can often surpass the initial capital expenditure on the system, while a lack of focus on design details at the planning stage can turn what should be a routine maintenance timetable into a major operation.
Preventative maintenance engineers from Anguil noted during a site visit that in one instance, a large pipe header had been plumbed across the front face of a low profile air stripper. The air stripper was used to access the removable trays.
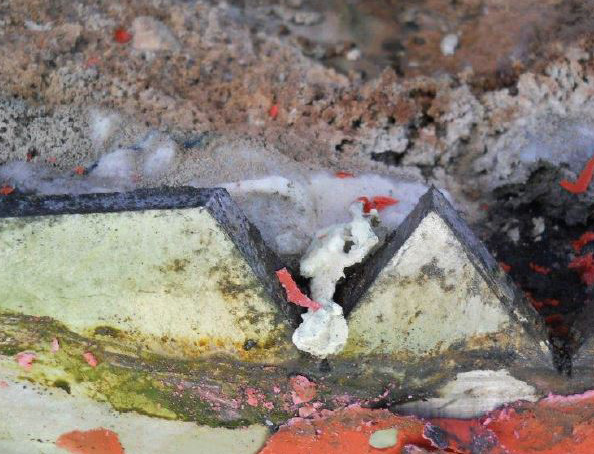
Hardness Deposits on Weir Plate. Image Credit: Anguil Environmental Systems
The location of the large pipe header meant that removing dirty trays for cleaning and replacing them with clean trays, which would usually be an activity that would take a single operator 30 minutes, now needed input from two operators over two days to safely remove and re-plumb the header.
Greater attention to detail and planning during the design or installation phases would have meant this problem could have easily been avoided. The piping could have been rerouted, or the air stripper could have been rotated.
Elsewhere, it was noted that a pH sensor had been placed in an elevated pipe run which was 3 meters from the ground.
This meant that what should have been a straightforward three-point recalibration of the pH sensor now involved hiring a man-lift and the involvement of a second operator to read the calibration values on the control panel, as a local LCD display had not been supplied on the pH analyzer.
These issues and many more maintenance problems could have been averted if a knowledgeable installation and operational specialist had been consulted when the system was still in the planning stage.
Acknowledgments
Produced from materials originally authored by Tim Jaglinski from Anguil Environmental Systems, Inc.
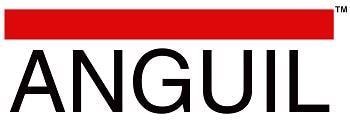
This information has been sourced, reviewed and adapted from materials provided by Anguil Environmental Systems.
For more information on this source, please visit Anguil Environmental Systems.