The treatment and disposal of surplus sludge are currently one of the most contentious environmental issues in the wastewater treatment industry. Excessive sludge from sewage treatment results from bacterial growth, the formation of inert materials in wastewater, and the buildup of endogenous residue. This article looks at the development of an innovative sewage sludge drying method using a modified solar greenhouse. The paper was published in Clean Technologies.
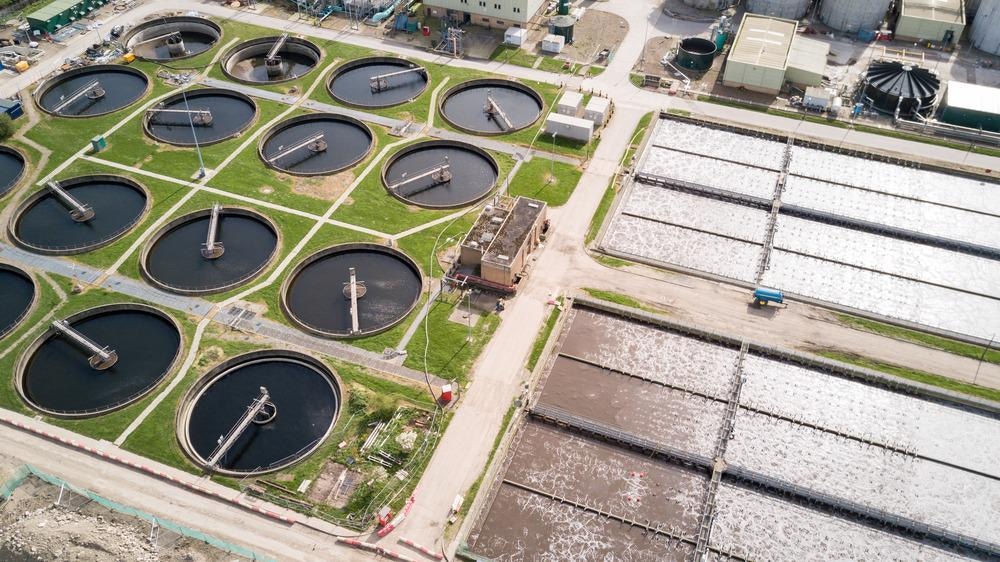
Image Credit: pxl.store/Shutterstock.com
Sludge handling in a wastewater treatment plant (WWTP) is associated with significant operational costs, which vary based on the plant’s site and the treatment method used in both the wastewater and sludge handling units.
Recent studies have pushed for the development of creative and cost-effective methods aimed at lowering surplus sludge distribution costs.
Sun greenhouse drying systems are a beneficial alternative for medium-small-scale WWTPs located in climate zones defined by strong solar radiation, with the goal of adopting environmentally friendly operations and utilizing renewable energy sources. Traditional solar greenhouses use both solar-generated hot water and energy provided by the greenhouse effect.
A dynamic greenhouse for sludge drying is made out of an impermeable floor warmed by hot water pipes where the wet sludge is placed, and a transparent ceiling (polycarbonate or glass) that creates the greenhouse effect.
Static solar greenhouses for sludge drying founded on the assumption of heat convection have not yet been presented to the best of the researchers’ knowledge. In light of this, the current research presents the first findings obtained with a unique closed-static solar greenhouse setup for sludge drying.
The use of a forced ventilation system rather than hot water below the wet sludge for sludge drying was the solar greenhouse’s key innovation, as was the use of 100% green energy for the whole system’s functioning.
Methodology
A 0.97-m long and 0.64-m wide polyvinylchloride (PVC) tank was used to design and build a pilot-scale greenhouse.
To prevent heat dispersion and conductive heat transmission to the outside, the tank’s sidewalls were sealed with polyurethane foam and an isothermal blanket. The solar greenhouse is depicted schematically in Figure 1.
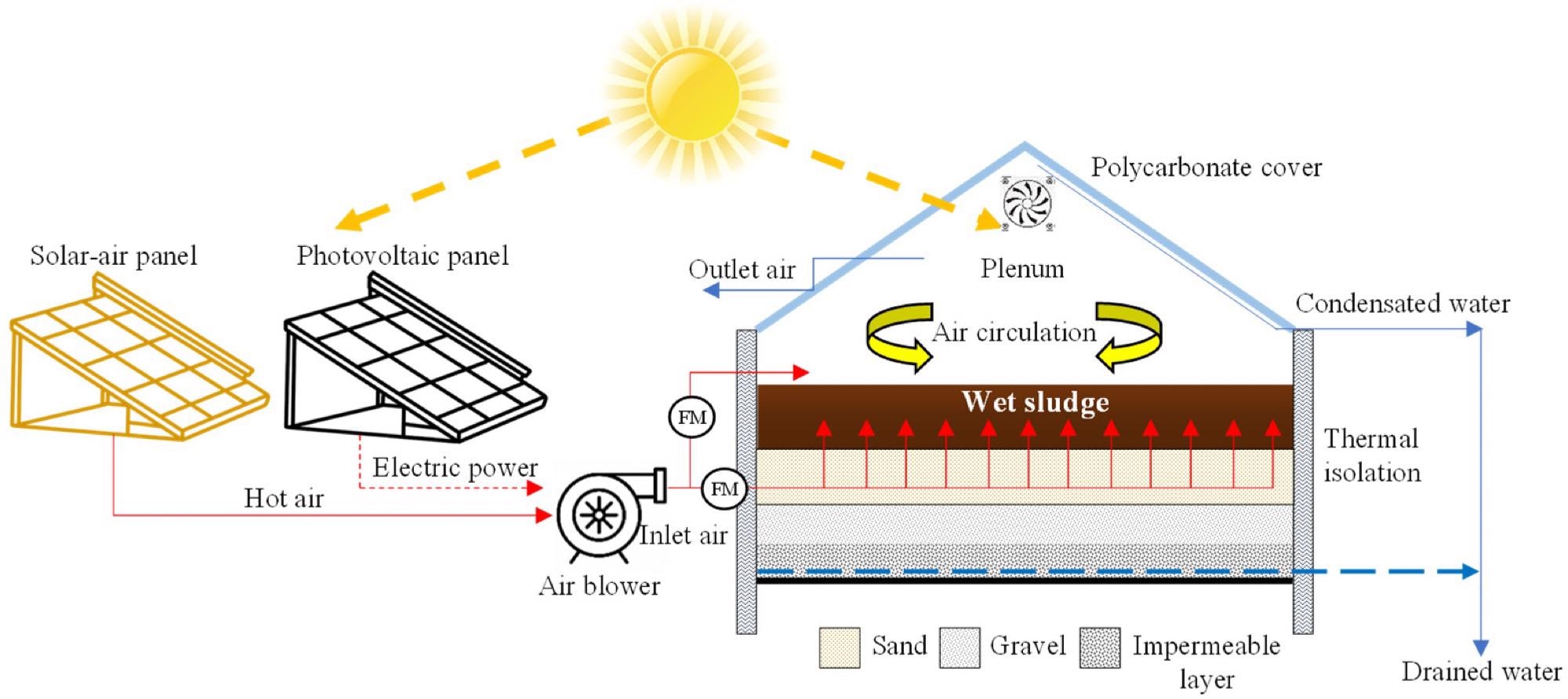
Figure 1. Schematic view of the static solar greenhouse. Image Credit: Sorrenti, et al., 2022
All studies, including the determination of sludge humidity and dry content, as well as overall and volatile suspended solids contents, were carried out using conventional procedures.
The drying curve was calculated to determine the sludge’s drying kinetics. This graph depicts the drying rate of the sample as a function of the sludge’s residual humidity. The drying rate was measured by subtracting the cumulative volume of water drained from the original water content, whereas the residual humidity of the sludge was measured by subtracting the constant quantity of water drained from the starting water content.
Results and Discussion
Figure 2 depicts the trends in mean temperature and highest solar radiation measured at various sites in the solar greenhouse as a consequence of weather conditions during the study.
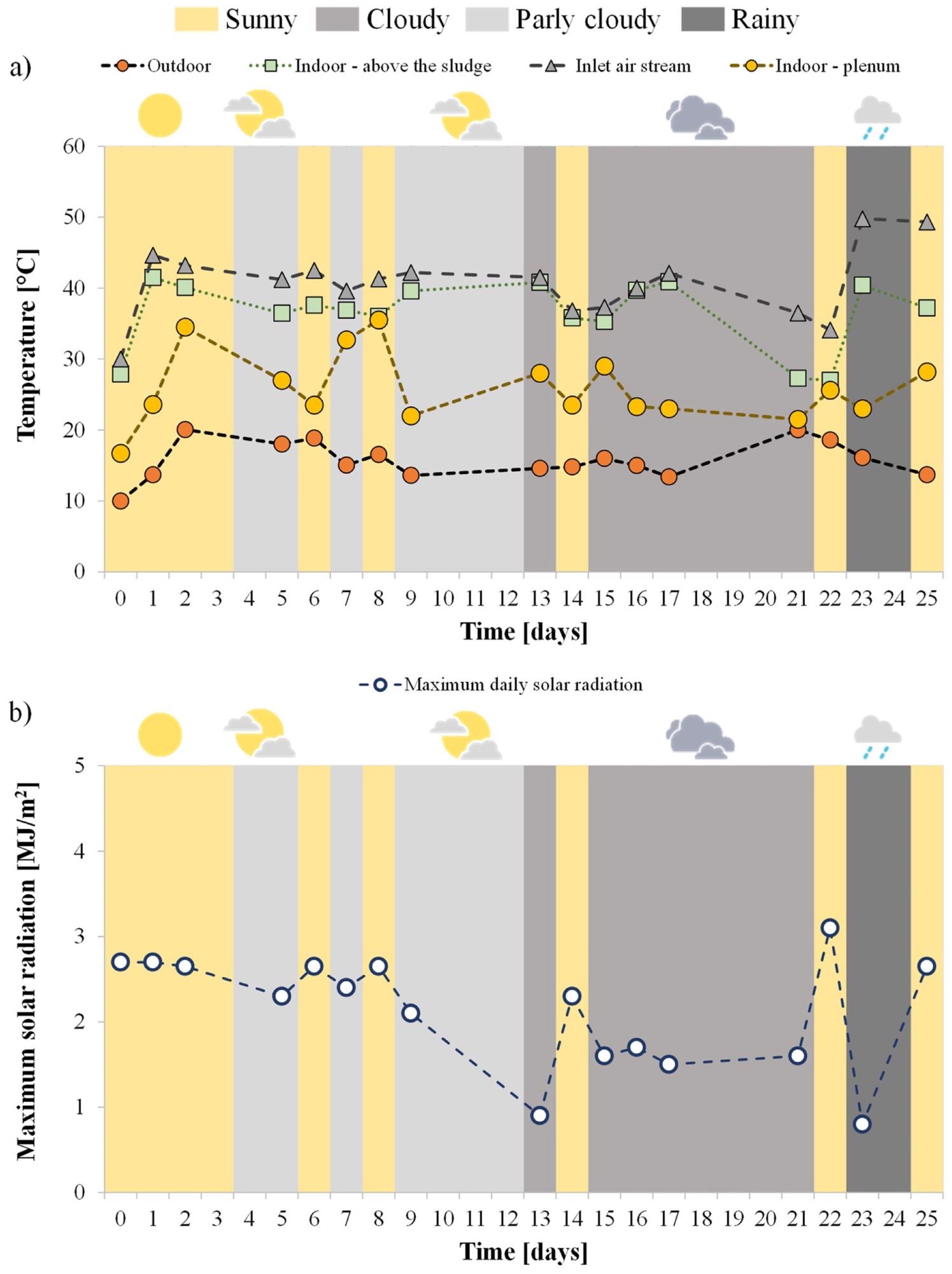
Figure 2. Wheatear conditions, trends of the average temperature measured in different points (a) and trend of the maximum daily solar irradiation (b). Image Credit: Sorrenti, et al., 2022
The weather was bright or somewhat cloudy for the first 14 days, then it became largely cloudy for the remainder of the study, with rainfall occurrences on days 23 and 24. Weather variables influenced the maximum daily incident sun radiation (Figure 2b).
This study looked at the impact of varied airflow rates underneath the sludge layer on the sludge drying process. Figure 3 depicts the relationship between residual humidity and the airflow rate blown further out on the sludge level.
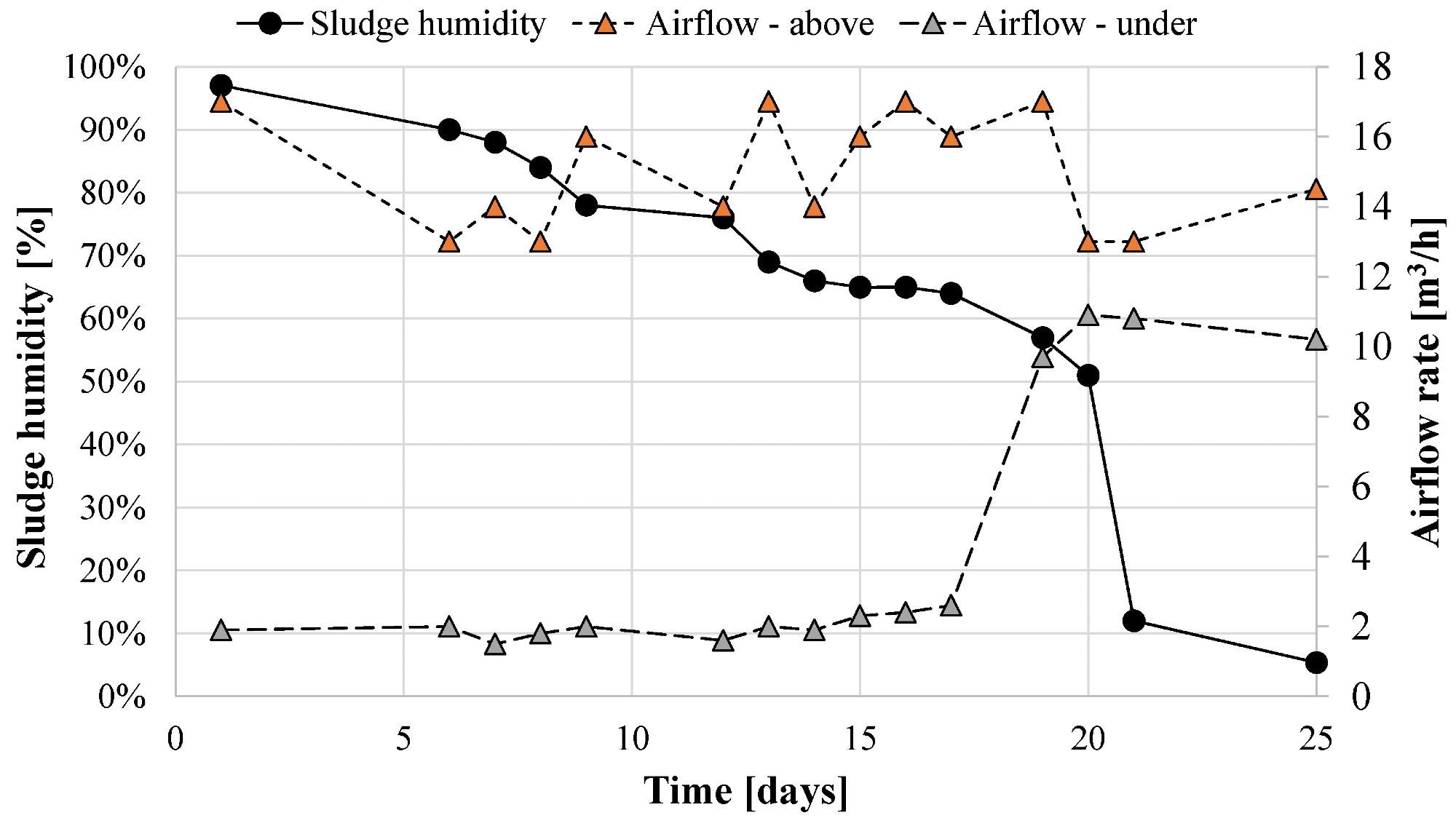
Figure 3. Trends of the residual humidity and the airflow rates during the experiment. Image Credit: Sorrenti, et al., 2022
During the first 18 days, the drying rate remained consistent, resulting in a daily humidity loss of around 2.30%. Beginning on the 19th day, the drying rate increased dramatically, resulting in a substantially higher humidity loss of close to 4% each day. This suggested that the airflow rate from the bottom of the sludge layer had an impact on the sludge drying kinetics and performance.
The drainage curve and sludge humidity at various levels were measured to provide deeper information regarding the sludge drying process and kinetics. Figure 4 displays a thorough view of the various phases of the sludge drying process, as well as the drainage curve, produced throughout the research (Figure 4a) and (Figure 4b).
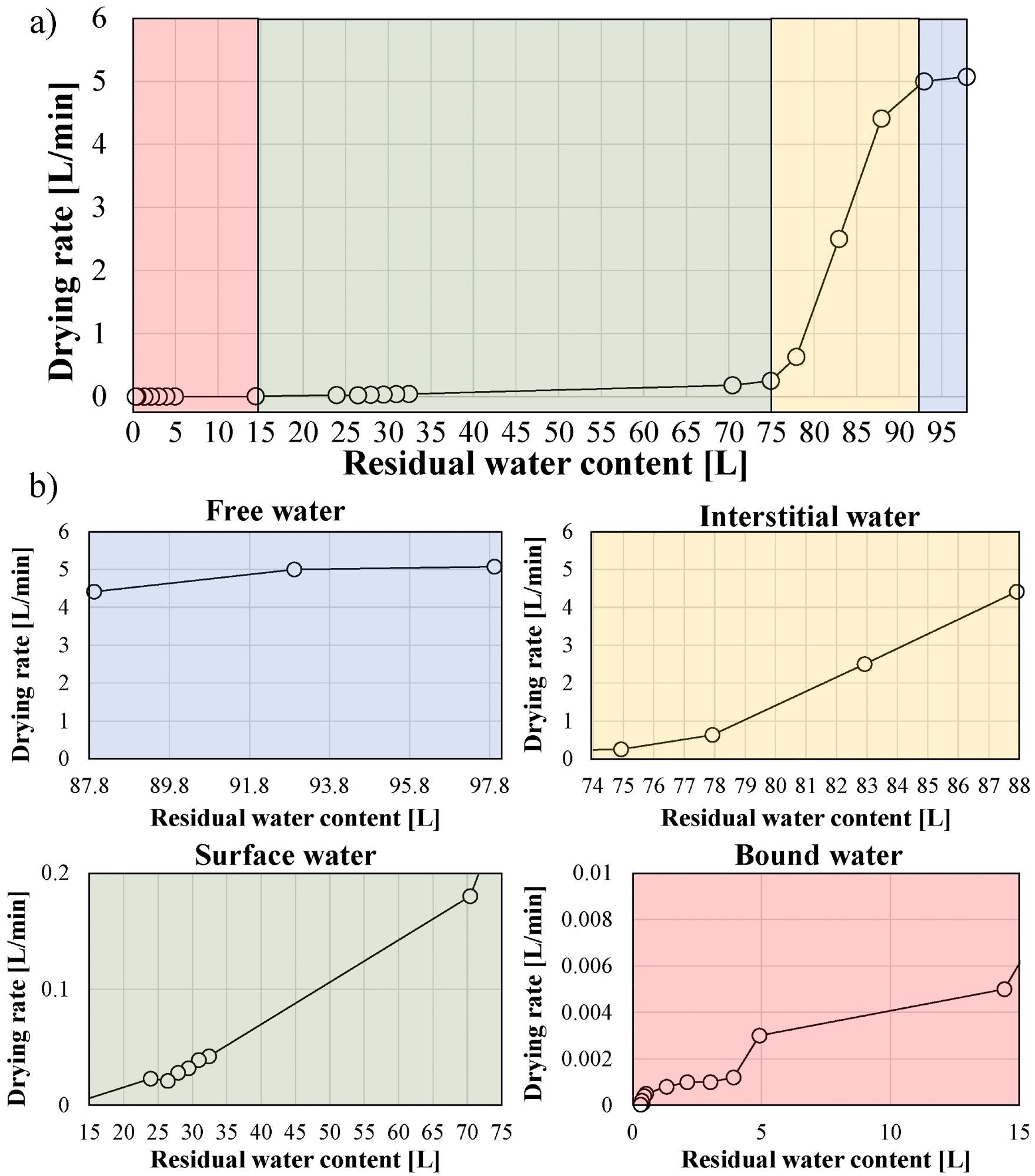
Figure 4. Sludge drying curve (a); detailed view of the several phases during sludge drying process (b). Image Credit: Sorrenti, et al., 2022
Figure 4a shows the usual profile of the wastewater sludge drying process reported in earlier research.
In particular, the curve’s initial phase was marked by a fairly steady water loss rate of around 5 L/minute, which correlated to the removal of residual water as stated in the literature. About 8% of the sludge’s basic moisture content was removed during this phase, which lasted roughly 3 minutes (Figure 4b).
Figure 5 shows the trends in sludge humidity measured by sensors at various levels below the surface during the course of nine operational days.
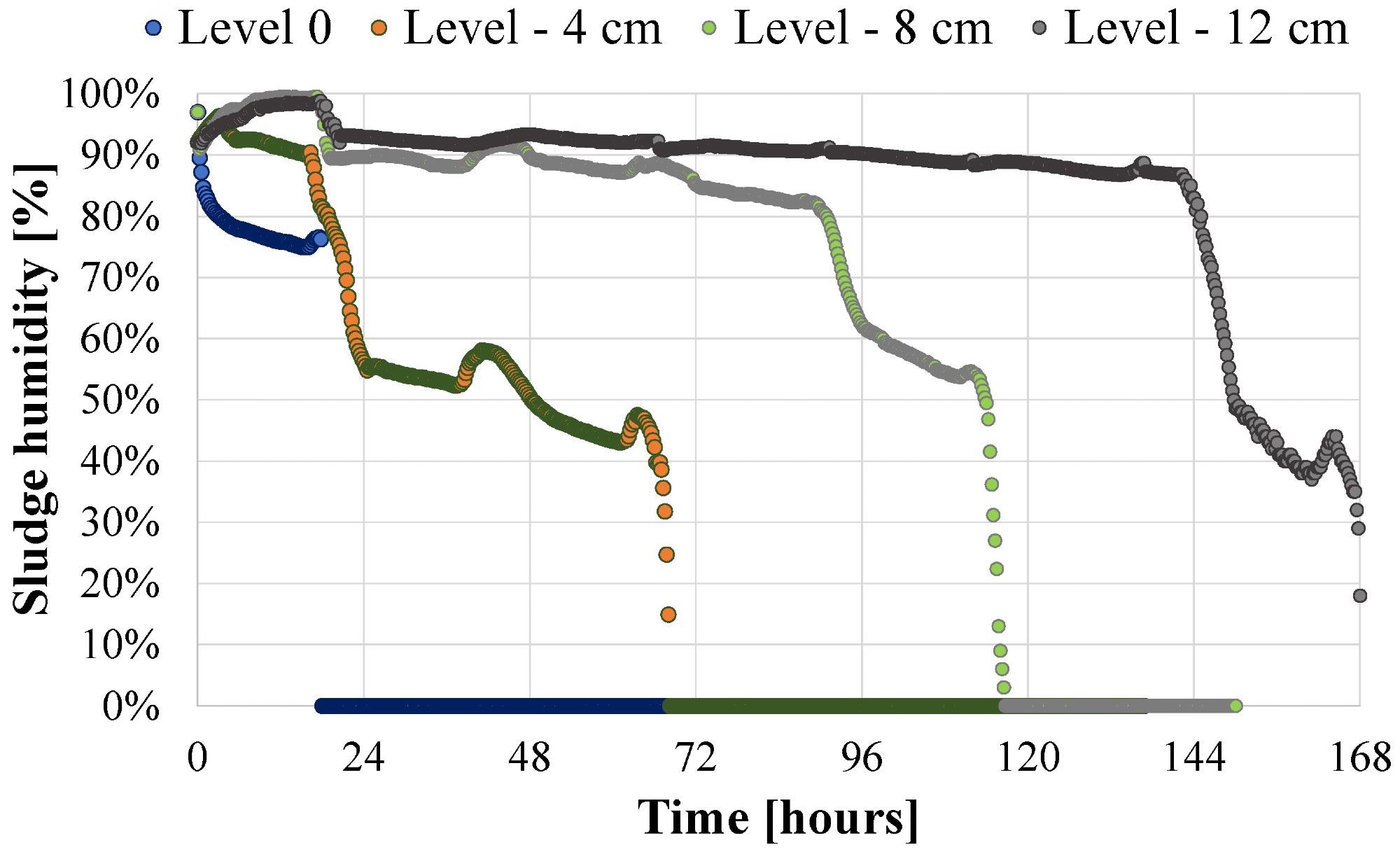
Figure 5. Trends of sludge humidity at different levels within the sludge. Image Credit: Sorrenti, et al., 2022
The starting and end values of the VSS/TSS ratio and sludge weight are shown in Figure 6. Wet sludge had an initial weight of around 125 kg, with a volatile suspended solids content of 73%.
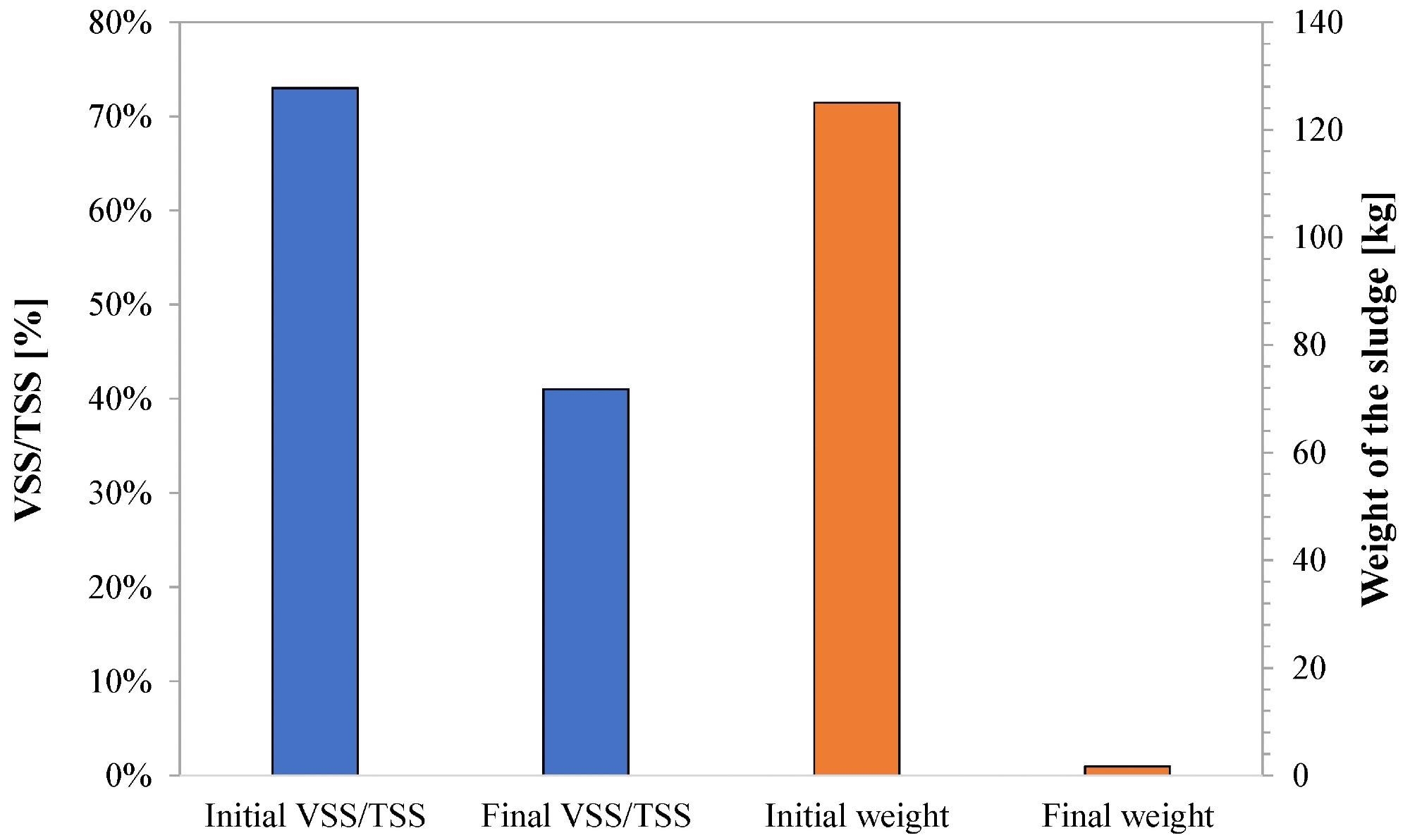
Figure 6. Initial and final values of VSS/TSS and weight of the sludge. Image Credit: Sorrenti, et al., 2022
Figure 7 shows two images of the sludge at the end of the test.
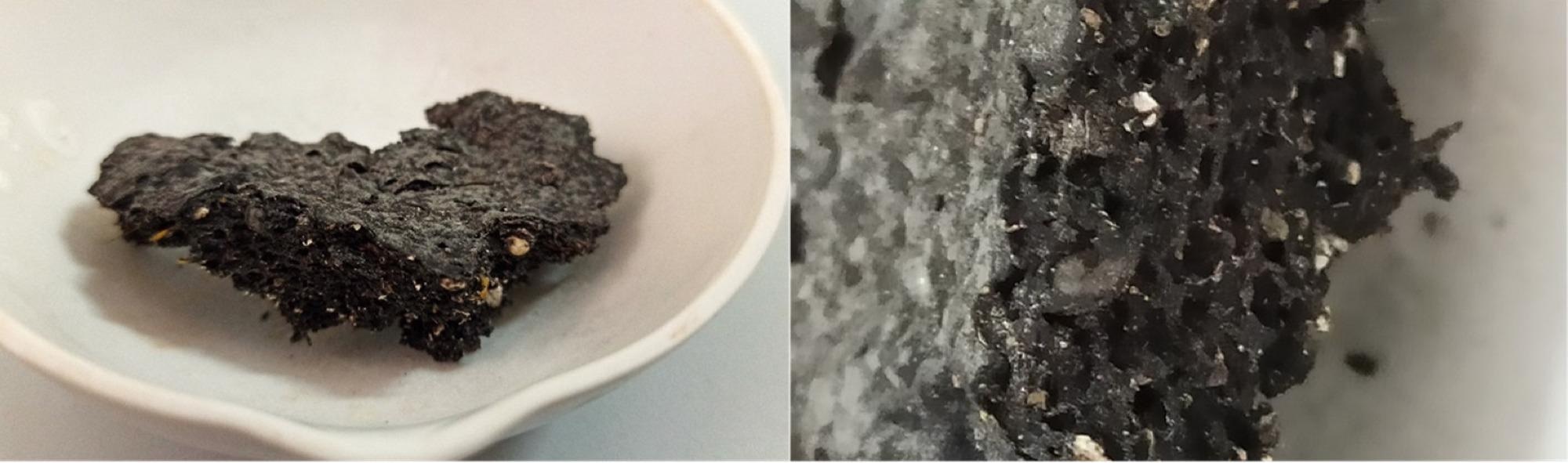
Figure 7. Images of the dried sludge at the end of the experiments. Image Credit: Sorrenti, et al., 2022
The sludge has a porous structure with a lot of cavities in it. This is attributable to the fact that throughout the drying process, channels of various diameters are formed inside the sludge, allowing water to drain.
The ultimate weight of the sludge at the end of the experiment was 1.67 kg, representing a decrease of almost 99% of the beginning sludge weight.
The net present value (NPV) was estimated for a 20-year period to determine the economic viability of sludge drying in the modified solar greenhouse.
The annual values of the NPV are shown in Table 1.
Table 1. Summary of the economic assessment though the NPV referred to a treatment potential of 1000 kg/d. Source: Sorrenti, et al., 2022
Year |
Initial Capital Cost |
Actual Cash Flow [EUR/Year] |
NPV [EUR] |
0 |
-EUR 365,200.60 |
EUR 0 |
-EUR 365,200.00 |
1 |
EUR 66,596.49 |
-EUR 298,603.51 |
2 |
EUR 63,425.23 |
-EUR 235,178.28 |
3 |
EUR 60,404.98 |
-EUR 174,773.30 |
4 |
EUR 57,528.55 |
-EUR 117,244.75 |
5 |
EUR 54,789.10 |
-EUR 62,455.65 |
6 |
EUR 52,180.09 |
-EUR 10,275.55 |
7 |
EUR 49,695.33 |
EUR 39,419.77 |
8 |
EUR 47,328.88 |
EUR 86,748.66 |
9 |
EUR 45,075.13 |
EUR 131,23.78 |
10 |
EUR 42,928.69 |
EUR 174,752.48 |
11 |
EUR 40,884.47 |
EUR 215,636.94 |
12 |
EUR 38,937.59 |
EUR 254,574.53 |
13 |
EUR 37,083.42 |
EUR 291,657.95 |
14 |
EUR 35,317.54 |
EUR 326,975.49 |
15 |
EUR 33,635.75 |
EUR 360,611.25 |
16 |
EUR 32,034.05 |
EUR 392,645.30 |
17 |
EUR 30,508.62 |
EUR 423,153.92 |
18 |
EUR 29,055.83 |
EUR 452,209.75 |
19 |
EUR 27,672.22 |
EUR 479,881.96 |
20 |
EUR 26,354.49 |
EUR 506,236.46 |
Conclusion
A redesigned solar greenhouse’s effectiveness for sewage sludge drying was evaluated. In 25 days, a residual humidity of around 5% was achieved, according to the findings. Furthermore, the introduction of hot air beneath the sludge bed resulted in a simultaneous impact of sludge stabilization.
Drying achieves a considerable weight reduction of up to 99%, which lowers sludge handling costs. Solar greenhouses are a very attractive technique for sludge drying in small WWTPs because of their low investment costs, low energy consumption (because of the use of solar energy), and easy maintenance.
Furthermore, because of the high dry solids content and low total volatile concentration, new disposal options, such as thermal treatment for energy recovery, may become available.
More research is needed to have a better understanding of the drying process and to assess the impact of various operational parameters on drying efficiency and process dynamics.
Journal Reference:
Sorrenti, A., Corsino, S. F., Traina, F., Viviani, G., Torregrossa, M. (2022) Enhanced Sewage Sludge Drying with a Modified Solar Greenhouse. Clean Technologies, 4(2), pp. 407-419. Available Online: https://www.mdpi.com/2571-8797/4/2/25/htm.
References and Further Reading
- Liu, W., et al. (2021) Environmental impacts assessment of wastewater treatment and sludge disposal systems under two sewage discharge standards: A case study in Kunshan, China. Journal of Cleaner Production, 287, p. 125046. doi.org/10.1016/j.jclepro.2020.125046.
- Foladori, P., et al. (2010) Sludge Reduction Technologies in Wastewater Treatment Plants. In: IWA Publishing: London, UK, 2010; ISBN 9781843392781. Available at: http://library.oapen.org/handle/20.500.12657/24365.
- Crutchik, D., et al. (2020) Polyhydroxyalkanoates (PHAs) production: A feasible economic option for the treatment of sewage sludge in municipalwastewater treatment plants? Water, 12(4), p. 1118. doi.org/10.3390/w12041118.
- Collivignarelli, M. C., et al. (2019) What advanced treatments can be used to minimize the production of sewage sludge in WWTPs? Applied Sciences, 9(13), p. 2650. doi.org/10.3390/app9132650.
- Oladejo, J., et al. (2019) A review of sludge-to-energy recovery methods. Energies, 12(1), p. 60. doi.org/10.3390/en12010060.
- Xue, S., et al. (2022) Emission, dispersion, and potential risk of volatile organic and odorous compounds in the exhaust gas from two sludge thermal drying processes. Waste Management, 138, pp. 116–124. doi.org/10.1016/j.wasman.2021.11.040.
- Khanlari, A., et al. (2020) Energetic, environmental and economic analysis of drying municipal sewage sludge with a modified sustainable solar drying system. \ Solar Energy, 208, pp. 787–799. https://doi.org/10.1016/j.solener.2020.08.039
- Di Fraia, S., et al. (2018) An integrated system for sewage sludge drying through solar energy and a combined heat and power unit fuelled by biogas. Energy Conversion and Management, 171, pp. 587–603. doi.org/10.1016/j.enconman.2018.06.018.
- Salihoglu, N., et al. (2007) Solar drying in sludge management in Turkey. Renewable Energy, 32(10), pp. pp. 1661–1675. doi.org/10.1016/j.renene.2006.08.001.
- Mathioudakis, V. L., et al. (2009) Extended Dewatering of Sewage Sludge in Solar Drying Plants. Desalination, 248(1–3), pp. 733–739. doi.org/10.1016/j.desal.2009.01.011.
- Belloulid, M. O., et al. (2017) Solar Greenhouse Drying of Wastewater Sludges Under Arid Climate. Waste and Biomass Valorization, 8, pp. 193–202. doi.org/10.1007/s12649-016-9614-1.
- Boguniewicz-Zablocka, J., et al. (2021) Sustainable management of biological solids in small treatment plants: Overview of strategies and reuse options for a solar drying facility in Poland. Environmental Science and Pollution Research, 28, pp. 24680–24693. doi.org/10.1007/s11356-020-10200-9.
- Singh, P., et al. (2018) Recent developments in greenhouse solar drying: A review. Renewable and Sustainable Energy Reviews, 82(P-3), pp. 3250–3262. doi.org/10.1016/j.rser.2017.10.020.
- Kurt, M., et al. (2015) Evaluation of solar sludge drying alternatives by costs and area requirements. Water Research, 82, pp. 47–57. doi.org/10.1016/j.watres.2015.04.043.
- APHA. (2012) Standard Methods for the Examination of Water and Wastewater. In: APHA: Washington, DC, USA, 2012; ISBN 978-0875532356.
- Berroug, F., et al. (2021) Simulation of sewage sludge drying under climate of solar greenhouse. AIP Conference Proceedings, 2345(1), p. 020044. doi.org/10.1063/5.0049423.
- Zheng, Q., et al. (2021) Effects of air parameters on sewage sludge drying characteristics and regression analyses of drying model coefficients. Applied Thermal Engineering, 198, p. 117501. doi.org/10.1016/j.applthermaleng.2021.117501.
- Lei, Z., et al. (2009) Sewage sludge solar drying practise and characteristics study. In: 2009 Asia-Pacific Power and Energy Engineering Conference, Wuhan, China, 27–31 March 2009. doi.org/10.1109/APPEEC.2009.4918741.
- Bennamoun, L (2012) Solar drying of wastewater sludge: A review. Renewable and Sustainable Energy Reviews, 16(1), pp. 1061–1073. doi.org/10.1016/j.rser.2011.10.005.
- He, X., et al. (2018) Ventilation optimization of solar greenhouse with removable back walls based on CFD. Computers and Electronics in Agriculture, 149, pp. 16–25. doi.org/10.1016/j.compag.2017.10.001.
- Bux, M., et al. (2002) Volume reduction and biological stabilization of sludge in small sewage plants by solar drying. Drying Technology, 20(4–5), pp. 829–837. doi.org/10.1081/DRT-120003765.
- Vaxelaire, J & Cézac, P (2004) Moisture distribution in activated sludges: A review. Water Research, 38(9), pp. 2215–2230. doi.org/10.1016/j.watres.2004.02.021.
- Deng, W. Y., et al. (2009) Measurement and simulation of the contact drying of sewage sludge in a Nara-type paddle dryer. Chemical Engineering Science, 64(24), pp. 5117–5124. doi.org/10.1016/j.ces.2009.08.015.
- Bennamoun, L., et al. (2016) Forced Convective Drying of Wastewater Sludge with the Presentation of Exergy Analysis of the Dryer. Chemical Engineering Communications, 203(7), pp. 855–860. doi.org/10.1080/00986445.2015.1114475.
- Deng, W., et al. (2011) Moisture distribution in sludges based on different testing methods. Journal of Environmental Sciences, 23(5), pp. 875–880. doi.org/10.1016/S1001-0742(10)60518-9.
- Wang, P., et al. (2019) Roof solar drying processes for sewage sludge within sandwich-like chamber bed. Renewable Energy, 136, pp. 1071–1081. doi.org/10.1016/j.renene.2018.09.081.
- Léonard, A., et al. (2004) Wastewater sludge convective drying: Influence of sludge origin. Environmental Technology, 25(9), pp. 1051–1057. doi.org/10.1080/09593330.2004.9619398.
- Bennamoun, L., et al. (2013) Review on fundamental aspect of application of drying process to wastewater sludge. Renewable and Sustainable Energy Reviews, 28, pp. 29–43. doi.org/10.1016/j.rser.2013.07.043.
- Krawczyk, P (2016) Control strategy for ventilation system of sewage sludge solar dryer. Journal of Power Technologies, 96(2), pp. 145–148. Available at: https://papers.itc.pw.edu.pl/index.php/JPT/article/view/746
- Slim, R., et al. (2008) Modeling of a solar and heat pump sludge drying system. International Journal of Refrigeration, 31(7), pp. 1156–1168. doi.org/10.1016/j.ijrefrig.2008.03.003.
- Bok, A (2017) Advantages and disadvantages of the solar drying of sewage sludge in Poland. Technical Journal, 12, pp. 171–179. doi.org/10.4467/2353737XCT.17.217.7760
- Zimmer, T., et al. (2022) Techno-Economic Analysis of Intermediate Pyrolysis with Solar Drying: A Chilean Case Study. Energies, 15(6), p. 2272. doi.org/10.3390/en15062272.
- European Comission. (2002) European Comission Part 4: Economic Report. In: European Comission: Brussels, Belgium; Luxembourg, 2002; ISBN 92-894-1801-X.