Aerzen has developed an innovative unit control system called AERtronic for the coordinated regulation of several types of units, namely, rotary lobe compressor, screw compressor and positive displacement blowers.
This is easy for the user, intelligent, and reliable, guaranteeing that the client plant or machine array will operate as desired, achieving the required operating point with respect to the system pressures and other parameters, even if the pressure is negative. It has been designed to offer maximum peace of mind to the customer about the way the plant is running.
.jpg)
AERtronic - Clever Functionality and Operation
Aerzen is known for its innovation, and with AERtronic it has raised the bar for blowers with its range of Delta Blower, Delta Hybrid and Delta Screw. This control system is extremely advanced, providing uniform and intelligent control for a set of packaged non-identical units. It is simple to connect a power cabinet from any manufacturer as an optional accessory, if required.
It offers several methods of control, security, and service of Aerzen units. Once activated, it takes over control of the machine to optimize machine operation to the highest efficiency depending on the pressure in the system, including negative pressure.
It also shows the operational information, while making sure the operating hour meter is running, and provides early event reports while the machine is running as well as recording them with date and time in its memory, so that they can be traced later. This is helpful in studying how the unit fits into the process and enables specific corrective action to be taken.
The AERtronic also looks after the service and maintenance of the machine, planning service employment with efficiency so that the machine can operate for a longer time.
.jpg)
Some of the functionalities offered by the basic model include:
- A front operating panel mounted on the acoustic hood which has a touch-screen as well as a color graphic TFT display of 4.3” dimensions
- Ability to regulate a power cabinet, either external or built-in
- Monitoring capability for measured values using limit values that can be adjusted
- Providing recording or output display of any machine incident
- Communication by MODBUS RTU as standard
- Non-stop metering of machine operating and service hours
- Operates in many languages, including all commonly used languages
- Displays specified measured values in graphic manner for a preset period
- User-friendly menu with password protection
- Modular technology allows targeted extension of control as needed
Optional modules include:
- Regulation by system pressure with the speed being specified to the frequency converter for the greatest energy efficiency
- Communication with a DCS via Profibus DP, or by Ethernet
- Failure notification by SMS through a GSM modem
- Regulation of acoustic hood heating in cold environments
- Monitoring of vibration with limit value criteria
- Software for visualization and interfacing with the PC connection
- Visualization software and interface for PC connection
.jpg)
Controls the perfect operating point: advanced AERtronic packaged unit control system, when using a frequency converter
Control in Compound Systems – Simply Solved with AERtronic
Each AERtronic already has a base load -/alternate switching capability which allows up to five Aerzen devices of equal priority to be linked up to each other via MODBUS RTU. As the pressure varies, an adjusted pressure band in the machine performs a connective-sensitive shutdown, with uniform distribution of its operating hours.
Energy can be saved to the tune of at least 30% because of optimized unit running periods that allow for better control of the maintenance intervals, if an AERtronic Master unit is added to the system. This allows up to 12 compressors and blowers to be controlled with fixed and variable speeds, from the same or different manufacturers, to form a powerful and very efficient coordinated setup.
At peak or increasing demand the Master control unit selects the most suitable machine to accomplish the task and switches this on. This minimizes the switching between idling and load cycles to save as much power as possible by reducing idling times to the bare minimum. The process data is also displayed for the operator, so they can assess the combination, making the operation clear and secure.
The addition of the AERtronic sets up the operation of the plant for many benefits:
- Proven and dependable control of Aerzen machines in a combined system
- Payment only for the required services due to the modular design which reduces unnecessary costs
- Every machine is controlled in the same way avoiding the need for re-accustoming each time
- Fast and easy machine control cuts down the time needed to operate the system while ensuring safety and efficiency
- Machine downtime is reduced along with increasing machine availability, which ensures a complete updating of the unit
Better Compression, More Success
Aerzen began as Aerzener Maschinenfabrik in 1864, and in 1868 the first European positive displacement blower rolled out from the plant. It was followed by the first turbo blowers in 1911. In 1943, the first screw compressors appeared, and 2010 saw Aerzen develop the first ever rotary lobe compressors in the world.
Aerzen has introduced many varied innovations which have advanced compressor technology considerably and progressively. This has brought it to the position of an industry leader, being the oldest manufacturer of positive displacement blowers, rotary lobe compressors, rotary piston gas meters, screw compressors and turbo blowers.
It is without doubt the primary supplier in many applications. With over 2,000 employees working at 40 affiliated companies the world over, the Aerzen experience is constantly harnessed to improve blower and compressor technology.
Aerzen manufactures the intelligent and successful products in its range because of its vast technical expertise, customer dialogue, and experience, which helps it to develop solutions that break new ground in energy efficiency, quality, and performance, as well as complying with ever-changing regulations. Finally, Aerzen offers a world-wide service to its customers post-sales.
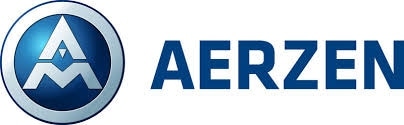
This information has been sourced, reviewed and adapted from materials provided by Aerzener Maschinenfabrik GmbH.
For more information on this source, please visit Aerzener Maschinenfabrik GmbH.