While the current global pandemic sees many manufacturers having to factor in the unknown, pollution control equipment still needs to be considered as part of a business’s decision making process.
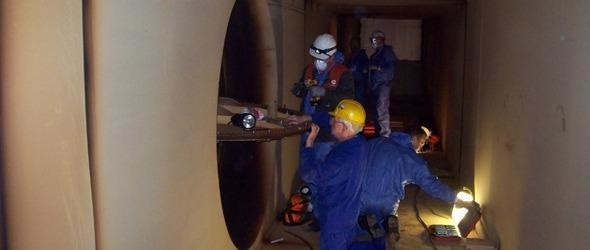
Image Credit: Anguil Environmental Systems
When facing uncertainty and rapid change, a calculated investment in existing pollution control systems can ensure compliance as well as offering opportunities for a quick return on investment (ROI).
These needs can include the addition of new process lines for new or expanded product offerings, changes in input process, increasing the speed of process lines, the consolidation of production plants, or the building of new facilities. Anguil is at hand to evaluate current equipment, capacities and production requirements to create a strategy that will fit the emerging needs of any business.
Rather than investing in new capital equipment, retrofitting existing equipment to fit tight timelines and lean budgets might be an option. There are three high payback equipment retrofits to consider.
Increase Capacity to Accommodate Production Changes
Adding more flow to the existing process is one commonly used option, and Anguil can expand the possibilities of existing pollution abatement equipment. Whether production lines need to expand or consolidate, retrofitting existing equipment is an option for treating additional flow.
How to Evaluate Capacity Changes
When evaluating capacity modifications, it is advisable to start by determining the current state and comparing its future goals.
For example, looking at whether the new flow exceeds the capacity of the existing unit by confirming and calculating existing and new levels of flow, VOC loading and temperature to oxidizer.
In general, it is possible to make modifications to existing units in order to increase capacity. This can be verified by reviewing the VOC loading and confirming it does not go beyond the capacity of the unit type. Engineering experts from Anguil can assist with exploring capacity modification options.
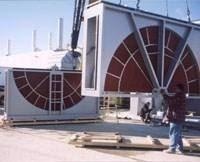
Image Credit: Anguil Environmental Systems
When capacity parameters have been determined, the next step is to evaluate several components’ ability to accommodate the new flow expansion. This generally involves the following steps:
- Evaluating upsizing the burner, which involves reviewing the burner system, fuel train and SFI.
- Changing the media design by reviewing media bed design, including size and depth, velocity, pressure drop, type of media, TER and residence time.
- Reviewing fan/VFD sizing for temperature flow and pressure rating.
- Adding an emission concentrator to reduce flow to the oxidizer by concentrating large flows of low concentration air upstream of the inlet.
Reduce Downtime with Controls Upgrades and Strategic Spares Management
Oxidizer operators can put in place preventive safeguards to ensure resiliency in instances of unexpected downtime. Judicious use of a spare parts inventory and investing in oxidizer control upgrades are just two high impact, low effort options for reducing equipment downtime.
Controls Upgrades
As oxidizer controls will normally operate without incident, even in conjunction with older software and hardware, they might not be regarded as a priority when it comes to replacement or upgrade plans. However, a lack of spares or a PLC crash can lead to significant downtime for older systems.
Anguil has considerable experience in consulting with operators on their oxidizer control needs. By developing customized solutions, unplanned downtime can be avoided, safety and compliance risks reduced and issues with obsolete parts minimized.
Obsolete parts may continue to operate, but these come with associated risks such as lack of customer service or protracted downtime.
As efficiency control components work in conjunction with each other, the failure of an obsolete or hard to replace component may require a full controls upgrade which can involve a 12 to 16week lead time.
Numerous controllers and I/O components commonly in use were discontinued in 2020. These included control components that were installed on equipment from Anguil that was manufactured prior to 2013.
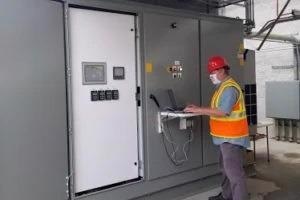
Image Credit: Anguil Environmental Systems
Anguil Aftermarket can help identify components scheduled for discontinuation by carrying out a Controls Review of current installed components and making recommendations for upgrading controls.
Incidents like display failures can impede the safe operation of an oxidizer system, so it is important to be ready to download the HMI program to a substitute display from a spare parts inventory.
Anguil Aftermarket can also perform PLC upgrades, even in instances where the original source code is unobtainable. Electrical and field service engineers from Anguil can specify, supply and install replacement hardware, as well as supplying and/or commissioning new software.
Upholding Safety Commitments
While a system might function adequately using components that are aging or even obsolete, the overal combustion system itself may not be meet current safety standards. Anguil Aftermarket can provide a review of the system’s program logic, suggest operational efficiency and safety improvements and develop a customized solution.
Utilizing hardware improvements such as an HMI (Human Machine Interface) upgrade can deliver improved system control and visibility on machine operations, plus troubleshooting options via the use of improved graphics and diagnostics.
Anguil Aftermarket offers a user-friendly 10” HMI option that combines straightforward operational capabilities with a graphical overview that incorporates loop bar graphs, trends, process values and I/O and purge interlock status.
Further upgrades, including Remote Ethernet Access and Digital Chart Recorders, can unleash the maximum capability of contemporary oxidizer control technology.
Maintaining a Spare Parts Inventory
Oxidizer spare parts programs deserve significant attention for a number of reasons. An effective spare parts program can help ensure:
- Increased uptime - downtime associated with a system issue can be dramatically reduced if the correct components are available on site.
- Regulatory compliance - keeping an appropriate stock of spare parts for an oxidizer system may be a requirement to comply with an environmental permit.
- Reduced loss of revenue - a well-stocked inventory of spare parts and components can get a system back online quickly, avoiding lengthy downtime, lost production and revenue, or wider plant issues.
- Long-term compliance - an appropriate stock of spare parts for an oxidizer system is an important element in ensuring long-term compliance with environmental regulations and commitments.
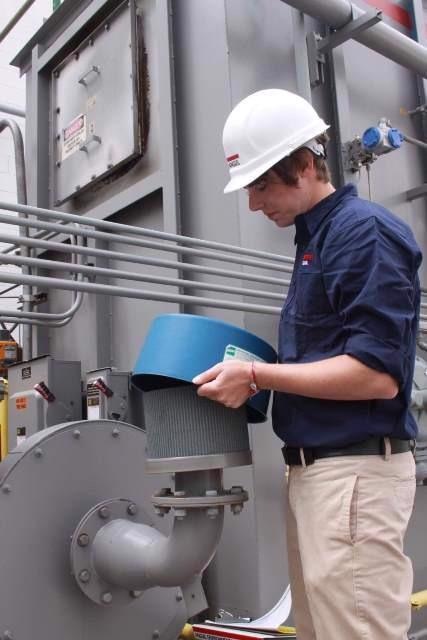
Image Credit: Anguil Environmental Systems
Anguil Aftermarket can create a customized Critical Spare Parts Package using the system process and instrumentation diagram (P&ID) and bill of materials (BOM) for any oxidizer system, regardless of the original manufacturing source.
Anguil Aftermarket can also provide components for ancillary equipment such as concentrator wheels, scrubbers and dust collectors. Each system component is logged into one of four categories in decreasing order of importance: critical, recommended, convenienceand when needed.
Source: Anguil Environmental Systems
Level |
Description |
Examples |
Convenience |
Consumables not critical to system operation |
Filter elements, door gasket |
Critical |
High use and high wear parts that are vital to system operation, parts that may have a long lead-time |
Actuators, poppet valve components, thermocouples, flow sensors and spark igniters |
Recommended |
These items are not typically known to fail; however, they cannot safely be bypassed if they do |
Air proving switches, PLC components and fuel train components |
When Needed |
Parts that are unlikely to fail or not generally critical to system operation |
Burners, gauges and flex joints |
The Critical Spare Parts Package
A critical spare parts package puts together the most important spare components for a system, sometimes at a discounted price. This removes conjecture from the process of ordering spare parts while ensuring this process is cost-efficient.
Not only does it assist in adhering to compliance requirements, a critical spare parts package bolsters the system downtime firewall and provides a discount when compared to the cost of ordering parts individually.
Anguil streamlines the procurement of parts because the company’s staff know the customer’s system, Anguil can deliver the necessary parts quickly, and engineering experts can quickly assess an unknown system to ascertain its parts needs.
Anguil also has an extensive system of vendor contacts, priority service and advantageous pricing, which is passed on to the customer.
Increase Thermal Energy Recovery (TER) for High Impact ROI
The media of an RTO is a vital objective area for high return on investment (ROI), something which may be offered through enhancements. Media replacements occur primarily out of necessity due to plugging, but there may be opportunities for improving ROI by focusing on the media’s TER performance.
Until recently, RTOs were designed with 95% Thermal Energy Recovery (TER) or less. If the average RTO outlet temperature is over 100 °F higher than the RTO inlet temperature, the TER% will most likely be less than 95%.
A slight increase in TER% can have a remarkable impact on RTO fuel usage, and in some instances, could completely eliminate RTO fuel use. Advances in ceramic media mean Anguil can enhance TER% in RTOs by swapping out a fraction of the current ceramic media beds, enhancing payback periods.
Anguil has carried out its retrofit process on many RTOs, regardless of the initial manufacturer. Anguil also offers a free Savings Cost Analysis making it easy to commence the retrofit process.
How to Evaluate a Media Design Change
It is advisable to start by ascertaining the current state before evaluating this against all available possibilities. The following should be noted during an evaluation of current media bed design.
- Media type
- Bed dimensions
- Space availability
The next step involves ascertaining current process conditions and calculating the current performance of the media. This involves consideration of:
- Airflow
- Inlet temperature
- VOC loading
- Combustion of air from the burner
- Current fan speed and sizing
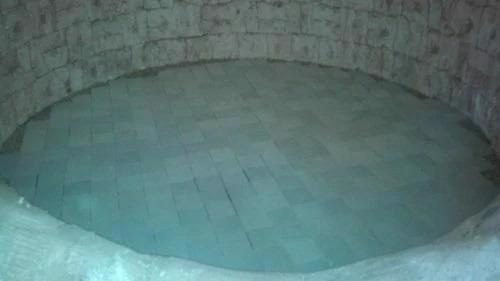
Image Credit: Anguil Environmental Systems
Finally, it is advisable to investigate a range of media suppliers before looking at the array of designs available. Important parameters should be kept in mind:
- Pressure drop across media beds and its potential to impact fan sizing and speed.
- Total flow requiring treatment, and whether this will impact pressure drop and velocity through the media.
ROI is determined by comparing the cost of the media retrofit versus any projected fuel savings will determine your ROI.
Anguil is a custom solutions provider, and the company’s team of experienced engineers is available to partner with customers.
This process involves gaining a comprehensive understanding of the customer’s system, taking on board its make, model, configuration and manufacturer before specifically designing the retrofit project to maximize system performance.
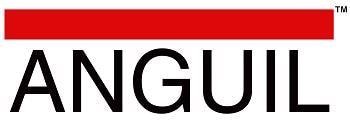
This information has been sourced, reviewed and adapted from materials provided by Anguil Environmental Systems.
For more information on this source, please visit Anguil Environmental Systems.