In this interview, AZoCleantech speaks to Anguil about the pollution control challenges from battery manufacturing, and how to make the industry greener from testing to recycling.
What are the pollution control applications of battery manufacturing?
Air pollution control and wastewater treatment are needed throughout the entire battery production chain, from material mining to powder production, anode coating, battery recycling, testing, and component manufacturing.
The industry is motivated to maintain its reputation as a good environmental steward and produce energy storage solutions that help our planet address climate challenges.
What are the pollutants of concern related to battery manufacturing?
Regulated by most state and federal agencies, volatile organic compounds (VOCs) are pollutants generated in many manufacturing processes. The battery industry is accustomed to these harmful by-products and the compliance hurdles that accompany them.
These organic vapors are dangerous to humans when inhaled in quantities over an extended period. They also interrupt and destroy natural plant processes and play a significant role in the formation of ozone and smog.
Hazardous air pollutants (HAPs) are a classification of VOCs with additional harmful properties, including potentially causing birth defects, nervous system damage, and even death in concentrated levels. HAPs are also regulated pollutants from battery manufacturing.
Some examples of pollutants produced by battery production are hydrocarbons, hydrogen fluoride (HF), hydrogen sulfide (H2S), sulfur dioxide (SO2), sulfur oxides (SOx), nitrogen oxides (NOx), carbon monoxide (CO), silane (SiH4), and other particulate.
‘Black mass’ is the industry name for the residual compound formed by ‘shredding’ Li-ion batteries that have reached the end of their usable life cycle. The challenge is to recover the lithium, nickel, manganese, and cobalt entwined within the battery and upcycle them into usable battery materials, which can be done by some battery recyclers.
Is there a standard pollution control system for battery manufacturing?
Battery manufacturing technologies and techniques are constantly evolving as producers look to remain competitive, increase storage capacity, and improve efficiency while decreasing battery size and weight.
Combined with an unprecedented increase in demand and subsequent production increases, this means that manufacturers are in a constant state of change and makes every pollution control project unique.
When battery advancements occur, many existing production inputs and manufacturing practices need to adapt quickly. This can include raw material adjustments, production equipment modifications, or a change in coating techniques, just to name a few.
The pollution control technologies employed at battery manufacturing facilities and material mining sites are affected by the upstream process changes and are getting greater attention by plant personnel.
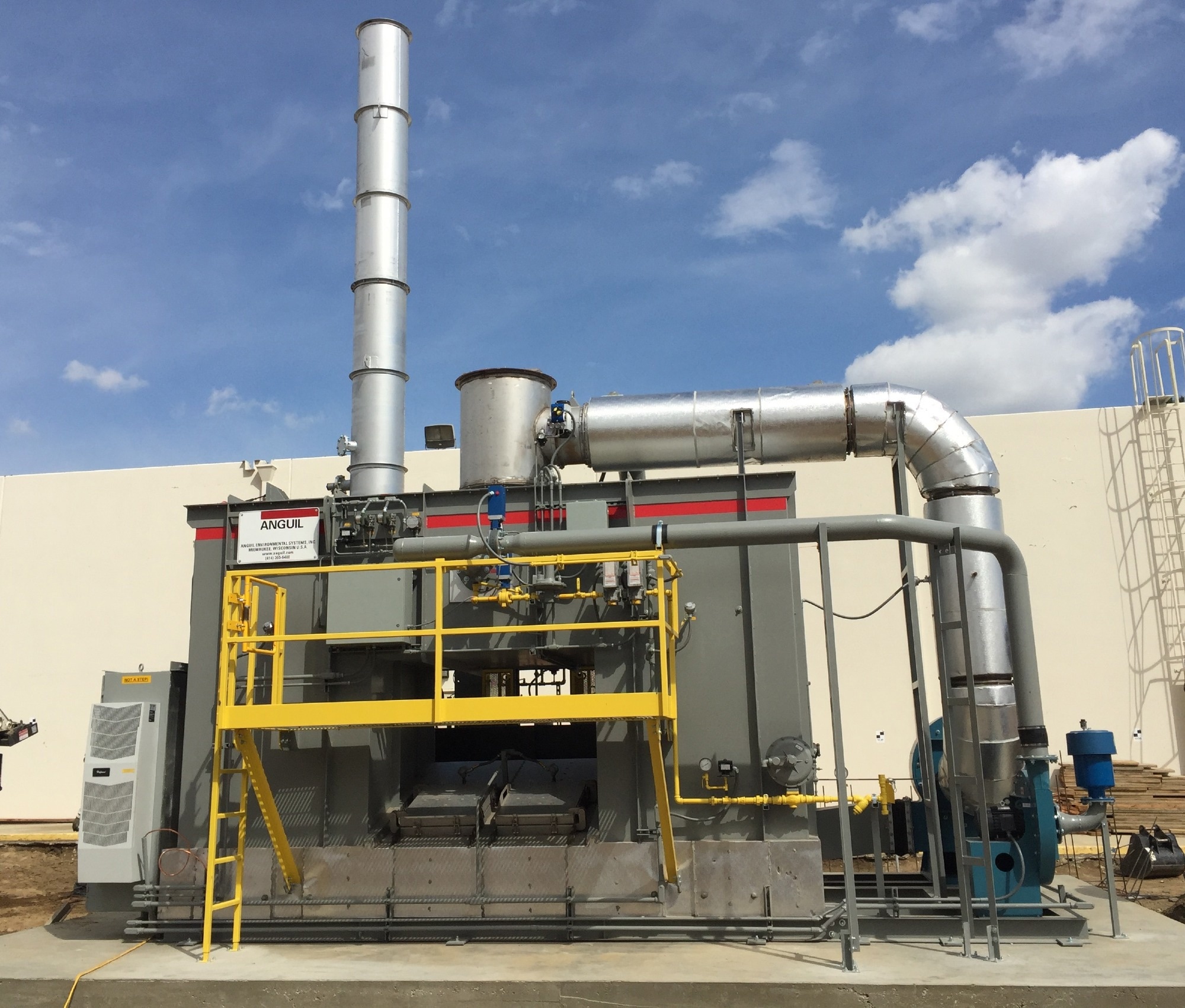
Image Credit: Anguil
What makes your product offerings unique in terms of air pollution control?
On air pollution control applications, many existing plants still tend to use scrubber technologies for emission abatement. With new, more stringent regulations, thermal oxidizer technologies can offer a lower carbon footprint, no wastewater by-product and higher destruction efficiency of VOCs and HAPs.
When talking wastewater treatment with Environmental, Health, and Safety (EHS) professionals they are often dealing with varrying constituents and concentrations so understanding the conaminents is critical. Many customers are utilizing our in-house water lab to help determind equipment options and estimated costs before commiting to a single treatment technology.
From a pollution control perspective, what trends are you seeing in battery applications?
On the wastewater treatment side of things, water reuse is a hot topic. POTWs (Publicly Owned Treatment Works) are increasing surcharges for water they receive from all industries.
In some cases, the POTWs are forcing industries to stop discharging certain compounds altogether. In other instances, they are increasing the surcharges to cover the cost of equipment required for treatment.
Whenever possible, the battery industry is looking to reuse water rather than pay higher surcharges or costs for an onsite treatment system.
In air pollution control applications, the thermal and catalytic oxidizers used for emission abatement are increasingly being designed with alternative fuel sources.
Traditional oxidation technologies use natural gas or propane to bring the systems up to operating temperature. Manufacturers like Anguil are now offering electric and hydrogen-fueled oxidizers to help customers reduce the carbon footprint from abatement systems.
What are the common pollution sources in the battery production chain?
From material mining to powder processing, anode coating, component manufacturing, battery recycling and testing, each stage of battery production generates unique by-products that require careful environmental management.
We are seeing consistent demand for emission control systems on process kilns and furnaces used for graphite and cathode material production. There are also many coating and finishing lines in battery manufacturing that utilize solvent-based chemicals like N-Methyl-2-Pyrrodlidone (NMP) which require recovery or destruction to meet regulatory requirements. At the upstream end, large-scale mining operations extract critical minerals from below the earth's surface and we are treating Ventilation Air Methane (VAM) from the shaft. Battery testing has become one of the most common, and complex, areas for air pollution control enquiries due to the unpredicable nature of emissions during different testing scenarios.
On the water side, the majority of treatment requests stem from battery parts washing operations. When local publicly owned treatment works (POTWS) either refuse wasterwater or impose prohibitive surcharges, we typically get involved. Our approach begins with evaluating the full process chain, identifying potential water reduction strategies, and then validating the best-fit treatment technologies.
What products does Anguil primarily supply to the battery supply chain?
Direct Fired Thermal Oxidizers
Direct Fired Thermal Oxidizers (DFTOs) have historically been used to destroy highly concentrated kiln exhausts from battery powder applications. The kiln exhausts from some graphite purification processes contain tar, which often causes plugging in a standard emission control device. Special design considerations can be implemented into the Anguil DFTO that reduce these maintenance concerns and improve reliability. The system introduces the exhaust into the DFTO with a unique inlet manifold that eliminates build-up and plugging concerns. The Anguil DFTO system can destroy over 99% of the air pollutants.
Anguil has also supplied Multi-Stage Direct Fired Thermal Oxidizers with Acid Gas Scrubbers to other graphite manufacturing operations, providing solutions for particulates, emissions, NOx, SO2, and hydrogen cyanide.
When oxidizing nitrogen bearing compounds such as ammonia and hydrogen cyanide, NOx will be a by-product and could lead to further environmental impacts. To eliminate these concerns, Anguil has designed the specialized multi-zone DFTO whereby the nitrogen compounds are destroyed in an oxygen-depleted chamber to prevent the formation of NOX. The remaining toxins then move to a secondary zone where total emission destruction efficiencies are over 99%. Optional acid gas scrubbers can be included to remove any inorganic acids.
Anguil also provides an induced draft system for increased safety on many of these applications. This ensures that all the pollutants would be drawn into the oxidizer for destruction, protecting employees and neighborhoods from potentially lethal situations.
Regenerative Thermal Oxidizers
Widely considered the most energy-efficient oxidation technology, the Regenerative Thermal Oxidizer (RTO) uses the thermal oxidation principles with a unique heat recovery component. Highly efficient ceramic media within the oxidizer captures heat from emission combustion and reuses it to preheat incoming pollutants thus minimizing supplemental fuel requirements.
Anguil has supplied a Regenerative Thermal Oxidizer (RTO) with upstream filtration on battery recycling operations. Recycled batteries are placed in a submerged shredder and then transported to a hammermill. Process exhausts from both the shredder and hammermill are directed to the RTO for destruction.
The RTO also uses uniquely designed poppet valves to divert process air into and out of the oxidizer, properly balance emission loading, maintain destruction efficiency, and optimize heat recovery. Most RTOs are a two-bed design, but they can be designed in a multi-chamber configuration to accommodate larger airflows and achieve destruction efficiencies above 99.7%.
Wastewater Treatment
In terms of wastewater treatment, Anguil also provides solutions. Volatile organic compounds (VOCs) and other harmful pollutants can be present in wastewater from battery operations, but they are more prevalent in the upstream suppliers to the battery industry.
Treatment trains from these operations can include a variety of techniques and several technologies to bring contaminated water to discharge requirements or reuse standards.
Contaminants of concern can be metals, total suspended solids, inorganic compounds, and a variety of acids. Whenever possible, manufacturers try to utilize water reuse methods to recover valuable raw materials and water that can be reutilized in the process.
There is no universal industrial wastewater treatment process in place for all applications and industries. Each application requires a unique treatment process, which is why many businesses need to install a customized solution based on their needs.
A well-designed system will help maintain compliance, reduce operational costs, minimize the risk of operator error, and increase throughput.
As battery manufacturing processes vary and are ever-changing, it is important to know what contaminants are present in the wastewater before designing a treatment train. Anguil routinely utilizes an in-house lab to test a battery manufacturer’s contaminants before making equipment recommendations.
Where can our readers find more information?
Readers can find out more from the following web pages:
About Sandra Beal
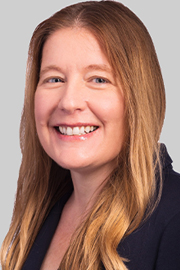
With decades of experience in the selection, optimization, and design of air pollution control systems, Sandy utilizes a strategic engineering approach to apply Anguil abatement technologies throughout the world, ensuring they meet various international regulatory requirements and efficiency standards. Sandy currently manages sales for the European market while supporting the company’s business development efforts in target regions and emerging industries. She holds a Bachelor of Science in Mechanical Engineering from Rensselaer Polytechnic Institute.
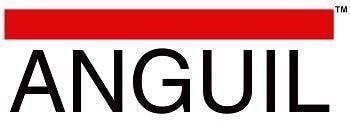
This information has been sourced, reviewed and adapted from materials provided by Anguil Environmental Systems.
For more information on this source, please visit Anguil Environmental Systems.
Disclaimer: The views expressed here are those of the interviewee and do not necessarily represent the views of AZoM.com Limited (T/A) AZoNetwork, the owner and operator of this website. This disclaimer forms part of the Terms and Conditions of use of this website.