Sponsored by TOFWERKReviewed by Aimee MolineuxOct 31 2023
Ensuring a contamination-free environment is of paramount importance in high-throughput semiconductor manufacturing. Vigilant oversight is required throughout the semiconductor fabrication plant (fab), covering cleanrooms, plenum areas, and sub-fab spaces.
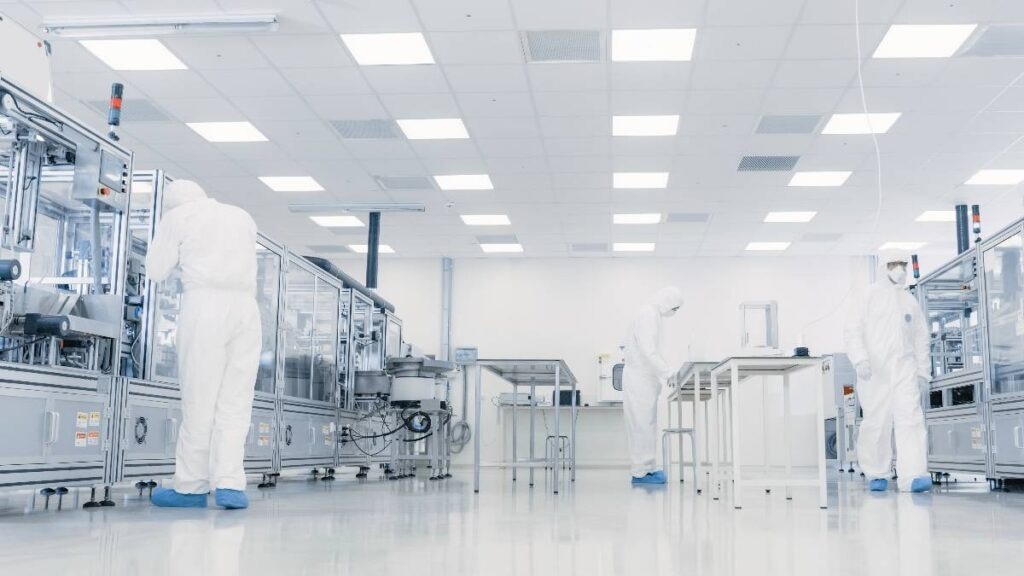
Felipe Lopez-Hilfiker, Abigail Koss, Adrian Mueller, Carla Frege TOFWERK, Switzerland and USA. Image Credit: TOFWERK
An integral component in semiconductor manufacturing, especially when dealing with Airborne Molecular Contamination (AMC) monitoring, is the manifold valve system, also known as the manifold sampling system.
This system plays a crucial role in monitoring gases originating from various sources, ensuring that processes are executed under optimal conditions and preventing material contamination.
AMC monitoring is a critical aspect of semiconductor manufacturing. Even minute quantities of airborne contaminants significantly impact product quality and performance.
Maintaining precise control over the flow of gases and chemicals used in the manufacturing process is essential, and this is where the manifold valve system becomes significant.
Manifold valve systems enhance sampling efficiency, allowing a single analyzer to oversee multiple sources. The speed of measuring each source or port is inversely related to the number of ports.
TOFWERK's multiport valve system, in conjunction with the AMC analyzer, offers rapid sampling, often within milliseconds. Each port is sampled within seconds, covering up to six different chemical ionization methods across a broad range of AMC classes.
Integrating TOFWERK's manifold system with AMC monitors is straightforward. The option to customize the number of sampling points is available by adding modules to the six accessible ports, as depicted in Figure 1.
The ultra-fast instrument response enables sampling of each port in as little as 10 seconds, ensuring that there are no memory effects between ports (see Figure 2).1
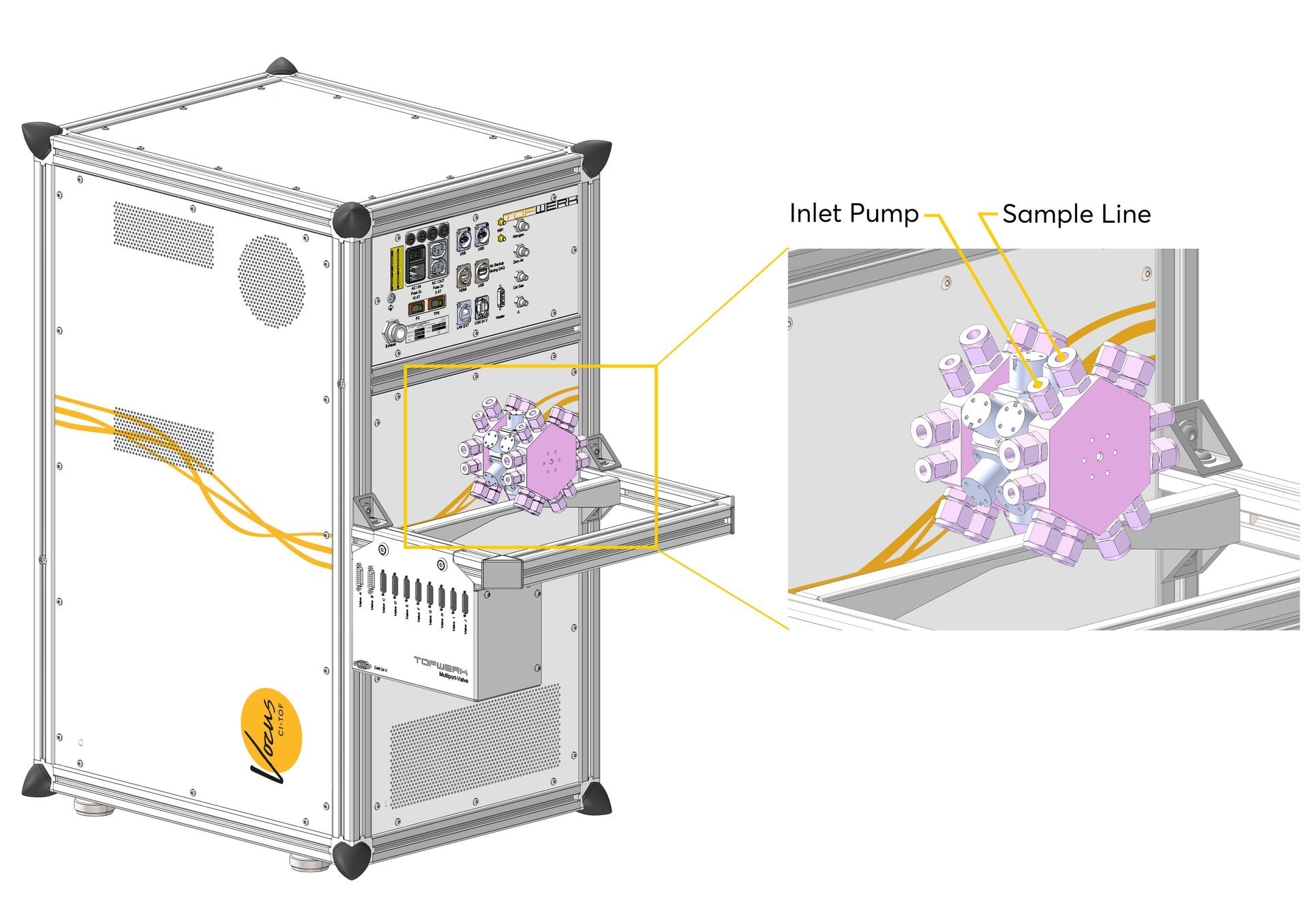
Figure 1. Schematic of TOFWERK’s multiport valve assembled with an AMC monitor. Image Credit: TOFWERK
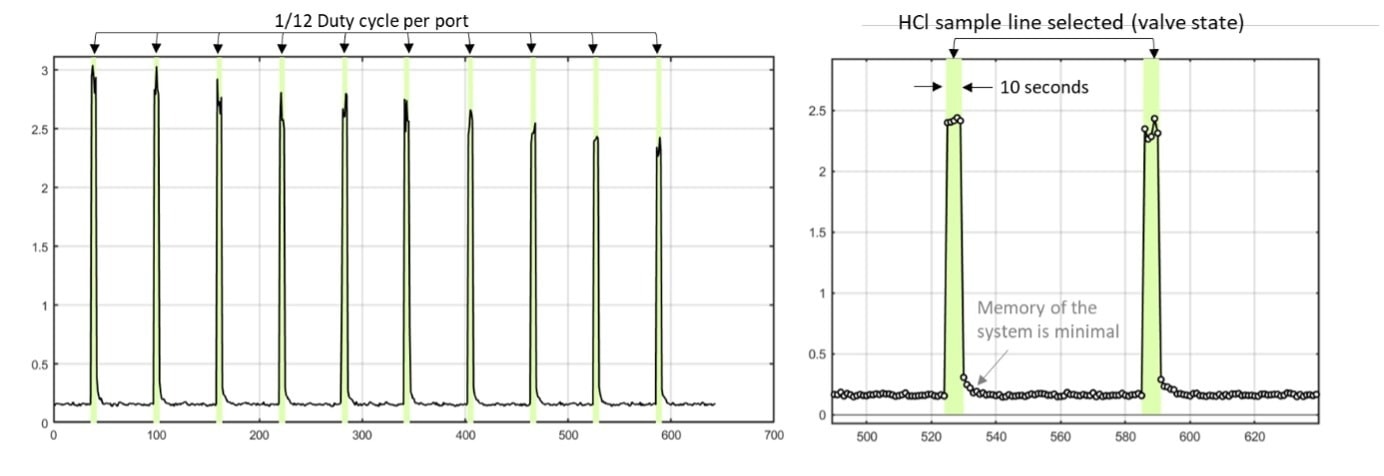
Figure 2. Duty cycle per port using twelve ports (left) and fast time response between ports (right). Image Credit: TOFWERK
TOFWERK's manifold system has undergone rigorous testing within fab facilities, which involved analyzing timed excursion events from various locations. The system accurately identified present AMCs, including acids, solvents, and bases. Instances of excursion events are displayed in Figures 3 and 4 for PGMEA and Cl2, respectively.
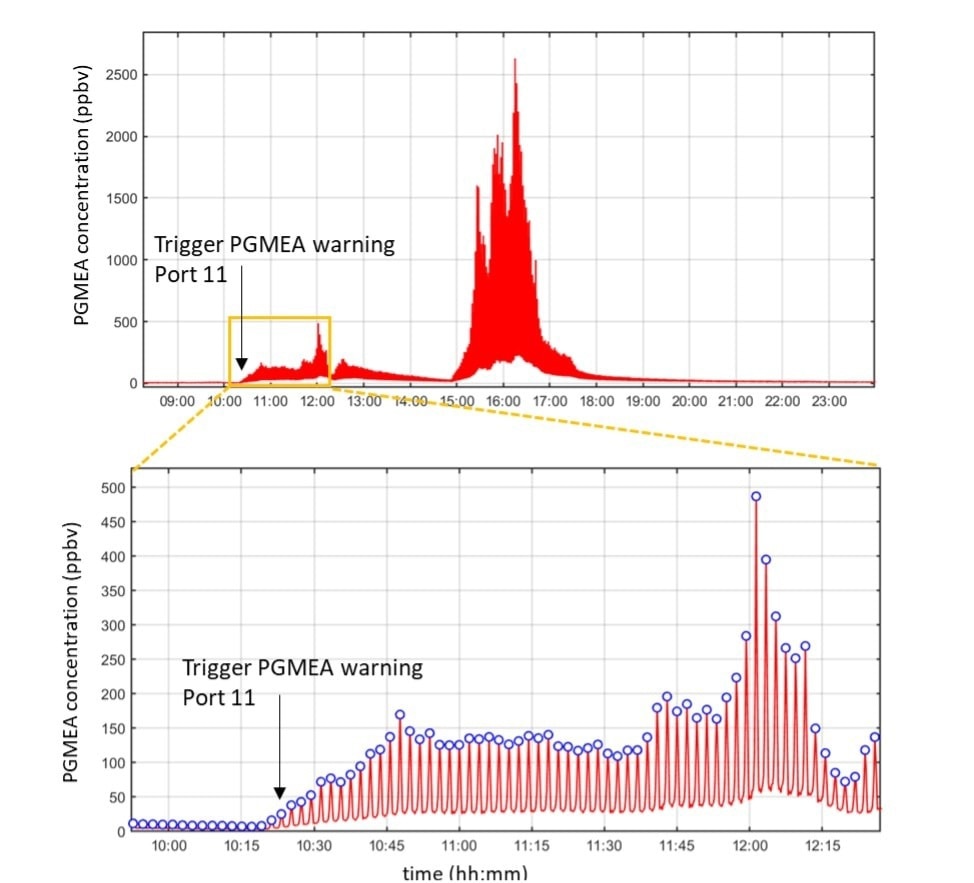
Figure 3. Top: Time series for PGMEA showing excursion events in one location (Port 11). Bottom: zoom-in in one of the excursion events where an alarm was triggered. Image Credit: TOFWERK
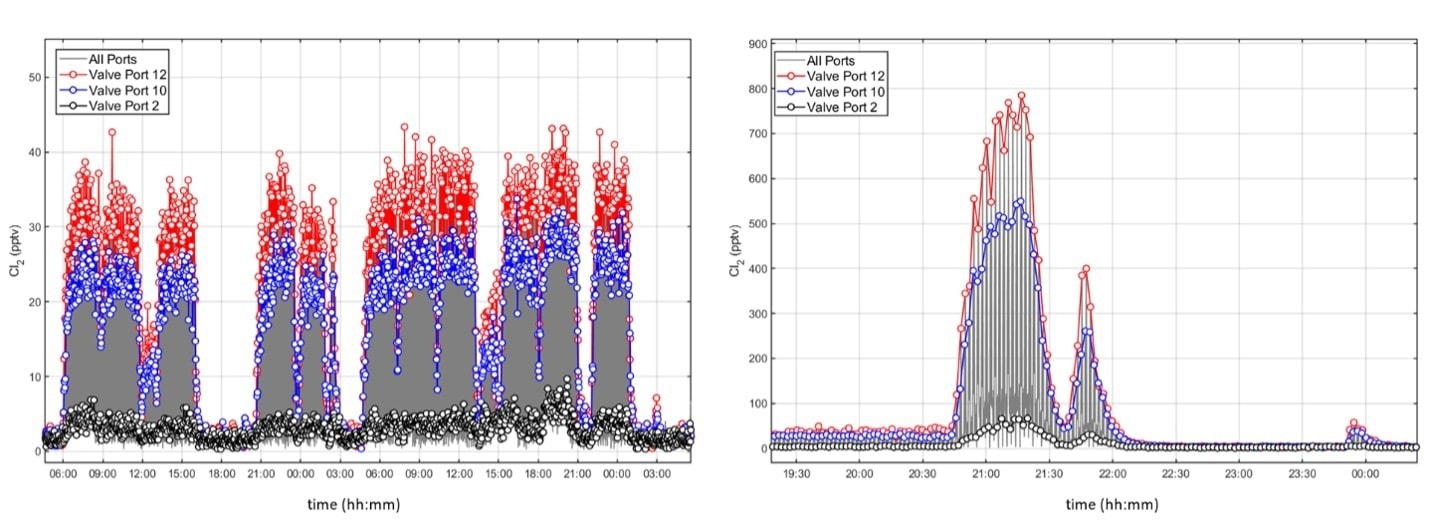
Figure 4. Chlorine ( Cl2) measurement in a fab. Left: recurring events with low concentrations ~50 pptv with measurement points at 3 different locations highlighted. Grey lines are the 12 port switching in a cycle of 2 minutes. Right: Excursion event reaching concentrations of almost 1 ppb in port 12 and 500 ppt in port 10, while other locations in the fab were minimally impacted. Image Credit: TOFWERK
This article outlines a demonstration of the utilization of a multiport valve system to enhance the efficiency of monitored locations and to assist in the detection of processes or events that impede production yield.
Depending on the contaminant's physicochemical characteristics, sampling delays may occur due to the interaction of the contaminant with the sampling lines.1 This effect remains unrelated to the analyzer and is instead influenced by the contaminant's volatility, absorption, and adsorption properties.

This information has been sourced, reviewed and adapted from materials provided by TOFWERK.
For more information on this source, please visit TOFWERK.