Handling cement comes with a range of flow challenges due to its unique material properties and the rigorous processes involved in its production.
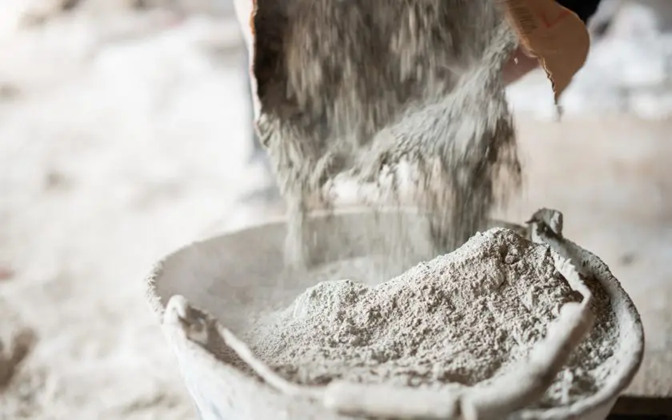
Close-up of a worker filling a bucket with cement from a bag at construction site. Image Credit: Jenike & Johanson
Whether handling raw materials like limestone or managing finished cement in storage, challenges such as arching, ratholing, erratic flow, and flooding can disrupt efficient operations. Understanding and addressing these flow issues is essential for maintaining smooth cement production.
Raw Material Flow Problems
Cement production depends on a steady and consistent feed of raw materials. The most commonly used raw materials include limestone, clay and sand (for silica).
If required, materials like mill scale (for iron), bauxite (for aluminum), gypsum, and fly ash are added to cement. However, these raw materials often exhibit poor flow behavior, particularly when being reclaimed from stockpiles or stored in silos or hoppers.
Arching and Ratholing
Two common flow issues in cement handling include arching (also known as bridging) and ratholing. Arching takes place when materials form an arch-like obstruction above the hopper outlet, practically blocking material flow. This can occur for multiple reasons, such as the interlocking of larger particles where the particles mechanically lock to make obstructions or when particles come together.
Ratholing, on the other hand, happens when material flows only through a central channel while the surrounding material remains stagnant, forming a vertical void. Both arching and ratholing significantly hinder material flow efficiency and often require manual intervention to resolve.
Erratic Flow
Cohesive materials like limestone, gypsum, and clay can cause erratic flow when stored in a poorly designed silo or hopper. This behavior occurs when material alternates between forming an arch and a rathole, obstructing flow. A rathole may collapse due to external forces, such as air cannons, causing a sudden material discharge.
As the material falls, it often accumulates over the outlet, forming an arch that may also collapse under external forces. When the arch breaks, flow resumes until the channel empties and another rathole forms. This cycle can create significant dynamic loads on the silo, increasing the risk of structural failure and causing inefficiencies, especially in processes requiring a continuous feed.
Flooding
If a rathole collapses and the material is fine—typically less than 150 micrometers, like Portland cement or fly ash—flooding can occur. In this state, the material behaves like a fluid due to aeration, potentially leading to uncontrolled discharge from the silo at high rates.
This can cause process spillage if downstream equipment isn’t designed to handle such flow conditions. Additionally, flooding can create challenges in bag filling, as the discharged material often has a low and inconsistent bulk density, making precise packaging difficult.
Dust Generation and Segregation
Cement handling produces a large quantity of dust, resulting in multiple operational difficulties:
- Fluidization segregation: Fine particles can trap air in their void spaces during handling, causing them to separate from larger particles.
- Dusting segregation: Fine particles stay suspended in an air stream longer than coarser particles and may be displaced from the fill point by a secondary air current, resulting in inconsistent material compositions.
- Health and safety concerns: Dust is a significant safety risk for workers and may lead to equipment wear and tea, elevating maintenance costs.
Controlling dust not only improves material flow but also creates a safer working environment and reduces equipment downtime. While specialized equipment like dust collection systems can help mitigate these risks, they must be properly integrated into the overall material handling process to be effective.
Temperature Effects
The high temperatures in cement production, especially during clinker handling, can significantly impact material flow properties. Hot clinker flows differently than cooled cement, and temperature fluctuations during production or storage can further alter material behavior, often leading to flow inconsistencies.
Segregation Issues
Segregation can be a significant challenge in cement handling, where materials separate according to particle size or density. Widespread kinds of segregation include:
- Sifting segregation: This happens when smaller particles sift down through larger ones in material transfer.
- Trajectory segregation: In discharge, larger particles travel further, while smaller particles usually fall near the outlet.
Both types of segregation can lead to inconsistent material quality, requiring operators to implement specific handling techniques to prevent these issues. Optimizing storage methods and controlling material flow can help minimize segregation and maintain uniformity.
Equipment Design Considerations
Addressing these flow challenges requires specialized equipment designed to accommodate cement’s unique properties. Mass flow bin designs are essential for preventing issues like ratholing and ensuring consistent material discharge. Properly sizing the outlet helps prevent arching, while certain materials, such as sticky limestone, may require specialized feeders like apron feeders with mass flow interfaces.
Additionally, bulk material testing serves as a proactive approach to identifying potential flow issues before they cause disruptions. By analyzing flow characteristics such as shear strength and wall friction, cement producers can refine equipment designs and implement corrective measures to improve handling efficiency.
Closing Thoughts
Cement handling presents numerous flow challenges due to the material's properties and the demands of the production process. Common issues like arching, ratholing, erratic flow, dust generation, temperature effects, and segregation must be addressed to maintain efficient operations.
Effective solutions include optimizing equipment design, managing moisture and dust levels, and conducting regular material testing to understand flow behavior. By focusing on these factors, cement producers can improve operational efficiency, reduce downtime, and enhance overall material handling performance.
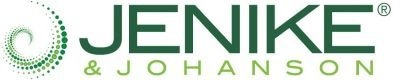
This information has been sourced, reviewed and adapted from materials provided by Jenike & Johanson.
For more information on this source, please visit Jenike & Johanson.