The Vapor Combustion Unit from Anguil integrates the ease of an enclosed flare with the thermal oxidizer’s destruction performance.
If planned for intermittent use or installed on a constant emission stream, the Anguil VCU technology has several benefits over other enclosed combustion systems. It is a robust device with the potential to tackle altering emission flow rates and concentration changes.
Thermal flaring technologies utilized to destroy hydrocarbons, volatile organic compounds (VOCs), or hazardous air pollutants (HAPs) have been developed in two fundamental configurations: open and enclosed flame burners.
New regulations on vapor radiation, visible emissions, greenhouse gases (GHGs), and noise pollution have driven the industry away from open flaring and toward the enclosed vapor combustion system.
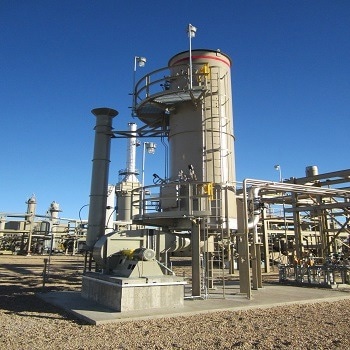
Image Credit: Anguil Environmental Systems
Product Overview
Benefits of Anguil’s VCUs
- Skid-mounted design eases installation and decreases charges
- Proprietary burner design removes visible emissions and the requirement for water or steam injection
- Air staging burner design further reduces carbon monoxide (CO) and nitrogen oxide (NOX) output
- Specialty burner design enables several separate process streams to be injected separably and concurrently
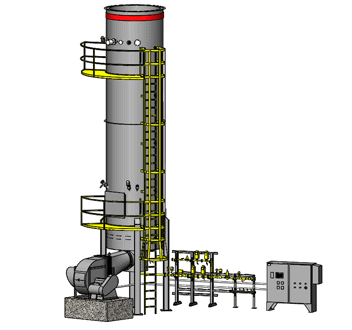
Image Credit: Anguil Environmental Systems
Product Overview
- Around 99%+ Destruction Rate Efficiency (DRE), Regulatory Compliance Guaranteed
- Optional Corrosion Resistant Coatings provided
- Free-standing construction available
- Forced draft or natural draft systems available
- Access ladder and platforms to sample ports and combustion chamber
- Gas trains have been developed to fulfill FM Global or any international certifications like EN, CSA, TSSA, or CGA
- Comes with a free-standing fuel train and control rack
- Programmable Logic Controllers (PLCs): automate operation startup to shutdown, reducing operator interface needs. Remote telemetry is capable of several enclosure options.
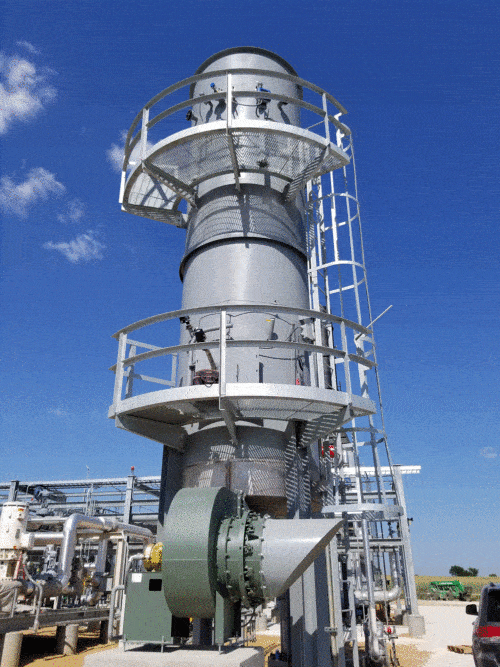
Image Credit: Anguil Environmental Systems
Features and Design Options
Features
- Process gas capacities range up to 100 MMBTU/H
- High turndown abilities / 10:1 or Greater
- Destruction Rate Efficiencies Up to 99+%
- Stainless steel construction on components vulnerable to weather damage
- Several burner options available for fuel input, such as propane, natural gas, and hydrogen, and ultra-low NOx or electric heating elements
- Completely integrated burner management system available
- Sample test and sight ports
- Flame Arresting Burners come for flashback mitigation and secure operation
- Trustworthy and automatic pilot ignition systems
- Gas trains have been developed to fulfill FM Global or international certifications such as CSA, TSSA, EN, CGA, and ATEX.
- Strong Programmable Logic Controller (PLC) based controls with digital data recording, remote telemetry, and several configuration options.
Options
- Knockout pots available for upstream liquid separation
- Comes with forced draft configuration
- Corrosion resistant metallurgies
- Heat transfer tubes available for process heating needs
- Refractory lined with ceramic fiber insulation
- Availability of low, medium, or high-temperature designs
- Natural draft or forced draft combustion
- Detonation or deflagration flame arrestors are available
Operating Cost Reduction Strategies
How do Vapor Combustors Work?
Based on the industry, the following terms might be utilized interchangeably to explain the vapor combustor technology: Medium Temperature Flare (MTF), Low Emission Flare (LEF), High-Temperature Flare (HTF), Industrial Burners, Biogas Flares, Enclosed Flares, Gas Burners, Open Flame Flare, Fired Heaters, Flare Stack, Candlestick Flare, Thermal Combustors, Fire Box, Enclosed Burners, Vapor Combustor Units (VCUs).
Before introducing process gases, a purge sequence inside the VCU eliminates any present combustibles from the device.
The pilot ignites just after the system controls verify a safe condition. The process gas is introduced into the system via an inlet duct or isolation valve. It is these process emissions which further start fueling the combustion device.
The vapor combustion of the Anguil unit could be developed in a natural draft configuration, nullifying the requirement for combustion air fans, or with a blower package under low process pressure conditions.
In most cases, combustion air has been drawn into the ruin chamber through one or more natural-draft air inlets. Regulating control dampers automatically offer temperature control guaranteeing proper combustion temperatures available for the oxidation of several compounds.
The emissions might be introduced to the combustion chamber via various burner heads or stages for highly variable process conditions, both regarding flow and hydrocarbon content.
Staged introduction of process gases leads to greater system turndown ratios and lower greenhouse gas (GHG) emissions like CO2 and NOX. Also, this firm and staged combustion burner enables emission destruction at low operating temperatures; normally between 1500 and 1800 °F (815 and 982 °C).
At the time of the operation, the destruction of process gases in the combustion chamber is typically achieved via an exothermic reaction. When inadequate VOCs are present to retain oxidation alone, supplemental fuel is needed for achieving destruction temperatures.
The natural gas burner is just utilized for supplemental firing to retain emission destruction and operating temperature during a low BTU content process gas condition. With the correct mix of time, temperature, and turbulence, the VCU normally notices destruction efficiencies upwards of 99+%.
Air Flow Range and Efficiency
Air Flow Range
- Varying flows and concentrations
Turndown Capabilities
Destruction & Removal Efficiency
Ideal Applications
Ideal Applications
- Altering process flow rates and vapor concentrations
- Maintenance demands are least
- High emission destruction needs
- Tank vents, mixing operations, loading stations, and more