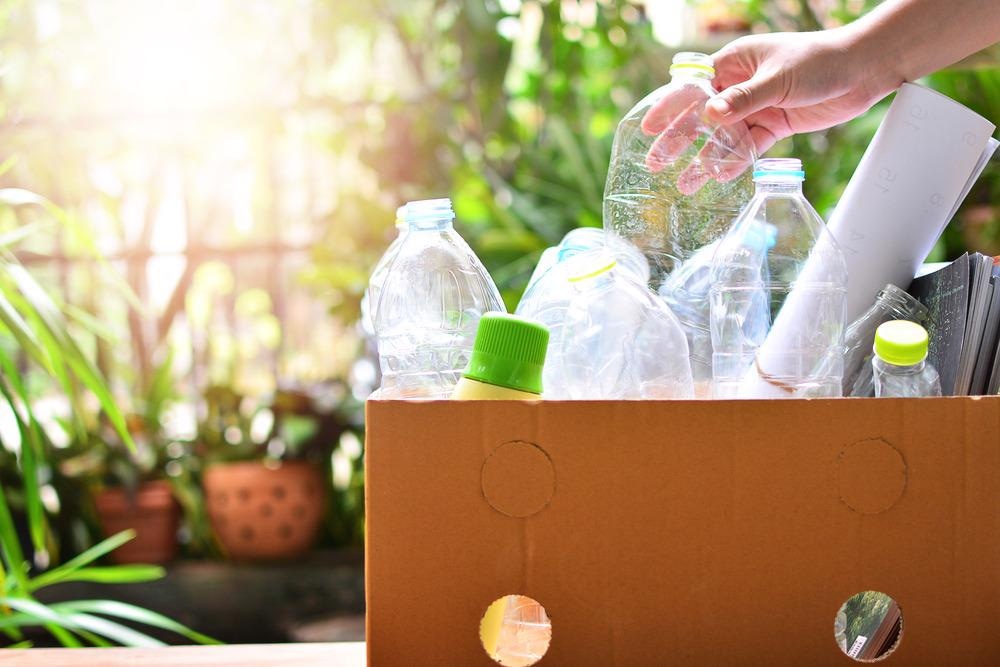
Image Credit: ITTIGallery/Shutterstock.com
Environmental solutions company Biofabrik is introducing its innovative plastic recycling technology WASTX Plastic to the global market. The first pilot plant is now fully operational at a QM Recycled Energy (QMRE) site in the UK, and the platform is entering serial production and international roll-out.
The WASTX Plastic technology from German company Biofabrik is the first of its kind to recycle plastic waste into tradable synthetic crude oil (so-called Syncrude) and energy in a decentralized and fully automated way.
The recycled oil is fed back into the raw material cycle to make recycled plastics, turning problematic waste into a valuable raw material and helping to close the plastic loop.
Over the last 20 years, the world has produced more plastic than during the whole of the 20th century. According to National Geographic, almost 50% of plastic products only get used once before being thrown away. Without the large-scale implementation of sustainable ways to manage plastic, the billions of tons that already exist will only continue to build until more plastic is in the ocean than fish by 2050.
Biofabrik’s fully automated waste-to-fuel WASTX plastic technology offers a convenient and easy solution to recycling plastic in a decentralized, scalable, and highly profitable way. The self-sufficient platform powers itself by generating electricity.
We want to contribute to building a world in which plastic waste is not a critical environmental problem, but instead – a valuable resource.”
Biofabrik
Biofabrik Dedicated to Tackling the World’s Environmental Challenges
Founded in Dresden Germany in 2011, the Biofabrik company brings together an interdisciplinary team dedicated to tackling the world’s environmental challenges by ensuring the sustainability of our planet’s resources in the most productive and nature-friendly way.
“The sustainable use of our planet’s resources is way more profitable than their constant and destructive exploitation,” says the team.
Chaired by CEO Oliver Riedel and CSO Jorg Metzner, the company has spent the last nine years researching and developing sustainable ways to manage waste, energy, and nutrition globally.
As well as WASTX Plastic, the company is also rolling out WASTX Oil Plants, which transforms thousands of liters of contaminated oil into fresh base oil that can be reintroduced into the raw material cycle.
This compact system can be set up in any village or city, irrespective of location, eliminating the need to rely on large disposal companies.
More about the WASTX Plastic Technology
Across the globe, 12,000 kg of plastic is produced every second, and 140 million tons is wasted every year.
The WASTX plastic recycling technology from Biofabrik is a container-based, decentralized, fully automated unit that can convert 1 kg of plastic waste into 1 liter of valuable recycled oil. The system processes the waste material at the source – where it is collected or produced – taking the solution to the problem rather than the problem to the solution.
“The new synthetic fuel will be pure enough to be used directly from production,” says Biofabrik. “Typical users of this fuel will be incinerator and furnace operators, marine vessels and heavy plant construction companies.”
The scalability of the technology is unlimited; each module of the platform, which can be connected in series, can process up to 1000 kg of plastic every day.
Previously shredded plastic is fed continuously and automatically into the system, where a temperature-controlled reactor enables the processing of multilayer and contaminated plastics. Using a process called pyrolysis, high temperatures crack long-chain hydrocarbons in the absence of oxygen. Solid hydrocarbon compounds move upwards in gaseous form, while contaminants such as metals and organic residues move downwards.
Conversion of the gaseous hydrocarbons to liquid using a multi-stage condensation process enables around 85% of registered plastics to be recaptured as recycling oil. In comparison, approximately 12% remains as a gas that forms a power source to fuel the unit.
The system leaves almost no residues, which are shifted via a collection system into a gas-tight container where metals are siphoned out, and any remaining carbon ash is used to produce, for example, bitumen and asphalt.
The final Syncrude oil product is stored in temperature-controlled tanks for use locally or remotely, depending on the application.
September 2020: WASTX Plastic: First pilot series plant is ready for delivery
Video Credit: Biofabrik Technologies GmbH/YouTube.com
Where Does QM Recycled Energy (QMRE) Come in?
Biofabrik’s UK distributor QM Recycled Energy (QMRE) has received its first pilot WASTX plastic plant, which is now in full operation at the company’s site in Longfield, Kent.
QMRE has extensively researched the market for pyrolysis-based plastic waste-to-fuel technologies, comparing multiple businesses worldwide that operate the systems, including in the US, Australia, China, and Europe.
Although QMRE had considered other technologies such as the bio-plastics route, they confirmed that pyrolysis was the preferred technology. Bioplastics were too expensive, with a poor carbon footprint that would lead to more landfill.
However, QMRE still needed to decide whether production should include batch processing or continuous processing. Competitor companies such as Recycling Technologies and Renew ELP pursued the batch-processing route, but QMRE considers continuous processing to be a far more efficient and profitable approach.
When QMRE co-founder and managing director Tim St Claire-Pearce heard about Biofabrik, he immediately placed an order for the WASTX Plastic pilot plant.
“It is a technology with continuous entry and yet it is a small and compact machine that can be installed anywhere, anytime. They are simply ahead of the rest of the world,” he says.
QMRE also signed a deal with Biofabrik to become the appointed sole distributor of the WASTX plastic recycling technology for the UK and Ireland. Towards the end of 2020, the first pilot plant was delivered to a QRME site in Longfield, Kent, where it is now in full operation. The plan is to create 50 sites across the UK with WASTX Plastic systems, with one in each county.
Worldwide Roll-Out of the WASTX Plastic Recycling Technology
Many other countries serving as official international Biofabrik distributors, including Saudi Arabia, and Turkey, will also be receiving their first pilot machines as the company works towards its ultimate goal of implementing hundreds of mini-recycling factories worldwide.
References and Further Reading
Biofabrik. Closing the Plastic Loop. [Online] Available at: https://biofabrik.com/en/white-refinery/wastx-plastic/
Biofabrik. Revolution engineering. [Online] Available at: https://biofabrik.com/en/
Pressebox (2020) German Startup makes decentral plastic waste recycling possible. [Online] Available at: https://www.pressebox.com/pressrelease/biofabrik-technologies-gmbh/German-Startup-makes-decentral-plastic-waste-recycling-possible/boxid/1028818
Pressebox (2021) WASTX Plastic: Pilot series in full operation in the UK. [Online] Available at: https://www.pressebox.de/pressemitteilung/biofabrik-technologies-gmbh/WASTX-Plastic-Pilot-series-in-full-operation-in-the-UK/boxid/1038665
QM Recycled Energy. Modular P-series WASTXPLASTIC. [Online] Available at: https://qmre.ltd/wp-content/uploads/2020/09/QMRE-P-Series-Brochure-Digital-High-Res-150dpi-1.pdf
Disclaimer: The views expressed here are those of the author expressed in their private capacity and do not necessarily represent the views of AZoM.com Limited T/A AZoNetwork the owner and operator of this website. This disclaimer forms part of the Terms and conditions of use of this website.