Increasing CO2 is a global problem and to capture it, various CO2 adsorbents are needed. This article looks at the design of a porous CO2 adsorbent reported in Cheng Duan et al's paper published in Materials.
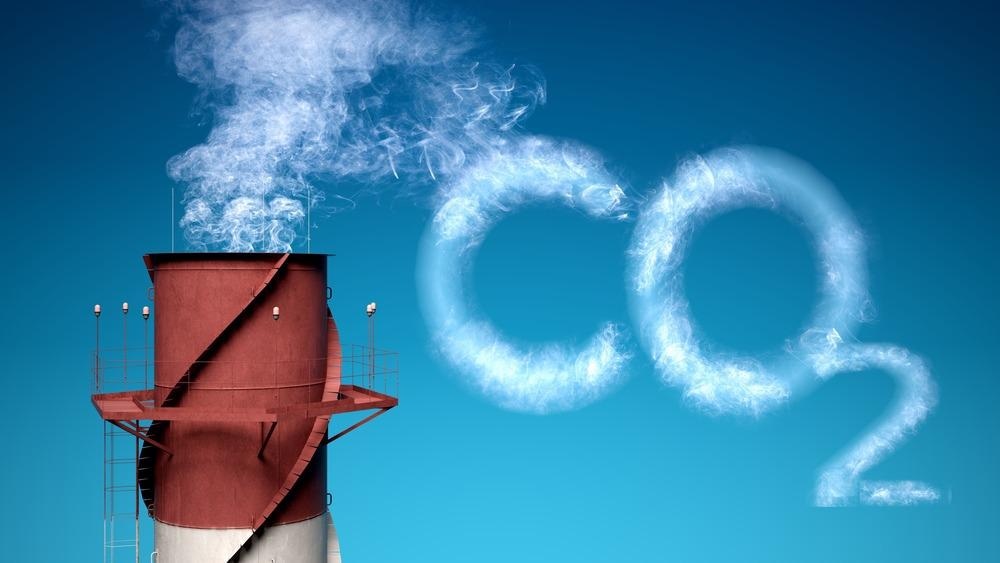
Image Credit: Billion Photos/Shutterstock.com
The increasing amount of carbon dioxide (CO2) in the atmosphere, a major reason for global climate change, has given rise to CO2 capture technology development. Numerous porous materials have been used as a CO2 adsorbent (zeolite, metal-organic frameworks (MOFs), porous organic polymers, and porous carbons). Porous carbons also harbor excellent CO2 capacities along with exceptional chemical and physical stability and hence have garnered much attention. The high CO2 capacities of porous carbon relate to the profuse micropore volumes and the heteroatom.
To decrease diffusion pressure in the adsorbent, mesopores or macropores were introduced into the adsorbent. The macroporous structures in polymers are created by removing the internal phase, and an open-cell interconnected porous polymer monolith was obtained.
This article illustrates the use of a concentrated emulsion for developing microporous–macroporou s carbon foams (“ACRFs”), depicted in Scheme 1.
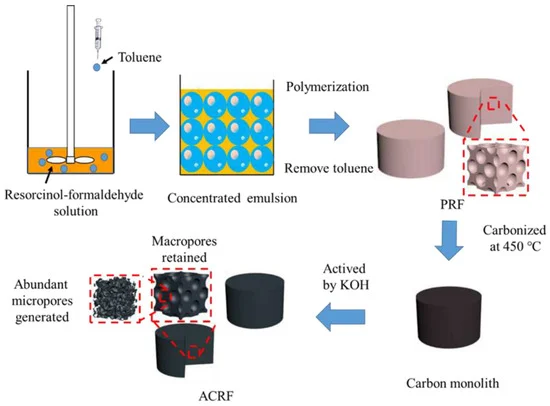
Scheme 1. Preparation route of microporous-macroporous carbon foams (ACRFs). Image Credit: Duan et al., 2021.
The researchers initially prepared macroporous resorcinol-formaldehyde resins (PRFs) with a concentrated emulsion, and later ACRFs were collected by carbonizing PRFs with potassium hydroxide (KOH) as an activator.
Methodology
Reagent
The fabrication requires Resorcinol and Tween 20, formaldehyde 37 wt% aqueous solution, anhydrous sodium carbonate and KOH, toluene, methanol, and ethanol.
Preparation of PRF
Into a 100 mL flask, Resorcinol, formaldehyde aqueous solution, anhydrous sodium carbonate, and deionized water were added and pre-polymerized. After cooling, the resultant solution was mixed with Tween 20, along with adding toluene. A light-pink emulsion forms, which was later transferred into a mold and solidified. PRFs are obtained during this process and the toluene droplets leave unique open-cell macropores simultaneously.
Preparation of ACRF
Carbonization of the PRF monolith was carried out by placing them in a tube furnace and heating, followed by soaking the pre-carbonized PRF in water/methanol solution dissolved with KOH for 3 hours. Upon carbonizing for an hour, ACRF was formed.
Characterization
The researchers analyzed Fourier transform infrared spectroscopy (FT-IR) spectra, X-ray photoelectron spectroscopy spectra (XPS). Macropores in PRFs and ACRFs were observed by scanning electron microscopy. The researchers also measured the N2 adsorption–desorption isotherms, specific surface areas of the samples, the pore size distributions, CO2 adsorption isotherms, Raman spectra, X-ray diffraction (XRD).
Results and Discussion
Carbonizing Process of ACRFs
KOH when used as an activator during the carbonization process generates more micropores in the resultant carbon. But due to hydrolysis it was difficult to load KOH solution in PRFs and so PRFs were initially carbonized at low temperature, then the resultant macroporous carbon can be impregnated with KOH aqueous solution and further activated at the demanded temperature.
Figure 1 shows the TGA/DTA curves used for determining the pre-carbonizing temperature and activation temperature.
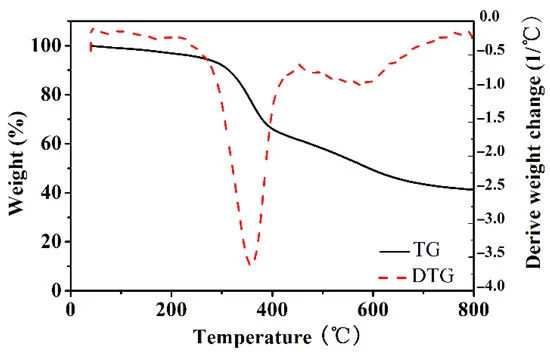
Figure 1. TGA and DTG curves of PRF-50C-85% under nitrogen flow. Image Credit: Duan et al., 2021.
Oxygen in Porous ACRFs
The XPS spectra of ACRF-50C-85%-600, ACRF-50C-85%-700, and ACRF-50C-85%-800 were used to analyze the surface chemistry state of these carbons (Figure 2) and revealed that the ACRFs were oxygen-enriched.
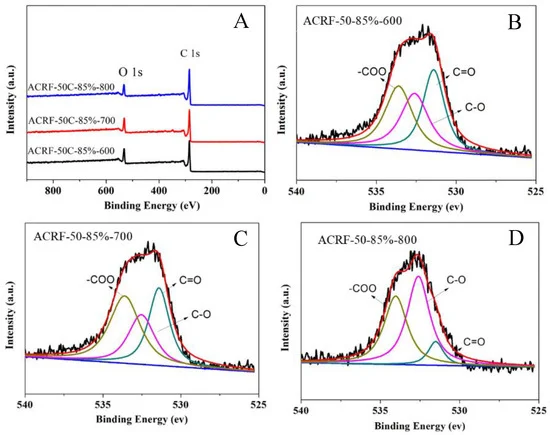
Figure 2. X-ray photoelectron spectroscopy (XPS) spectra of all ACRFs (A) and deconvolution of O 1s peaks of ACRF-50-85%-600 (B), ACRF-50-85%-700 (C) and ACRF-50-85%-800 (D). Image Credit: Duan et al., 2021.
Porosity of ACRFs
Figure 3 depicts the macroporous morphologies of PRFs and ACRFs. In the case of PRFs, SEM of the porous material showed numerous closely-packed cavities (“voids”) interconnected with the adjacent ones by small pores (“windows”). ACRF-50C-80%-800, ACRF-50C-85%-800, and ACRF-40C-85%-800 had macroporous structures of their corresponding PRFs.
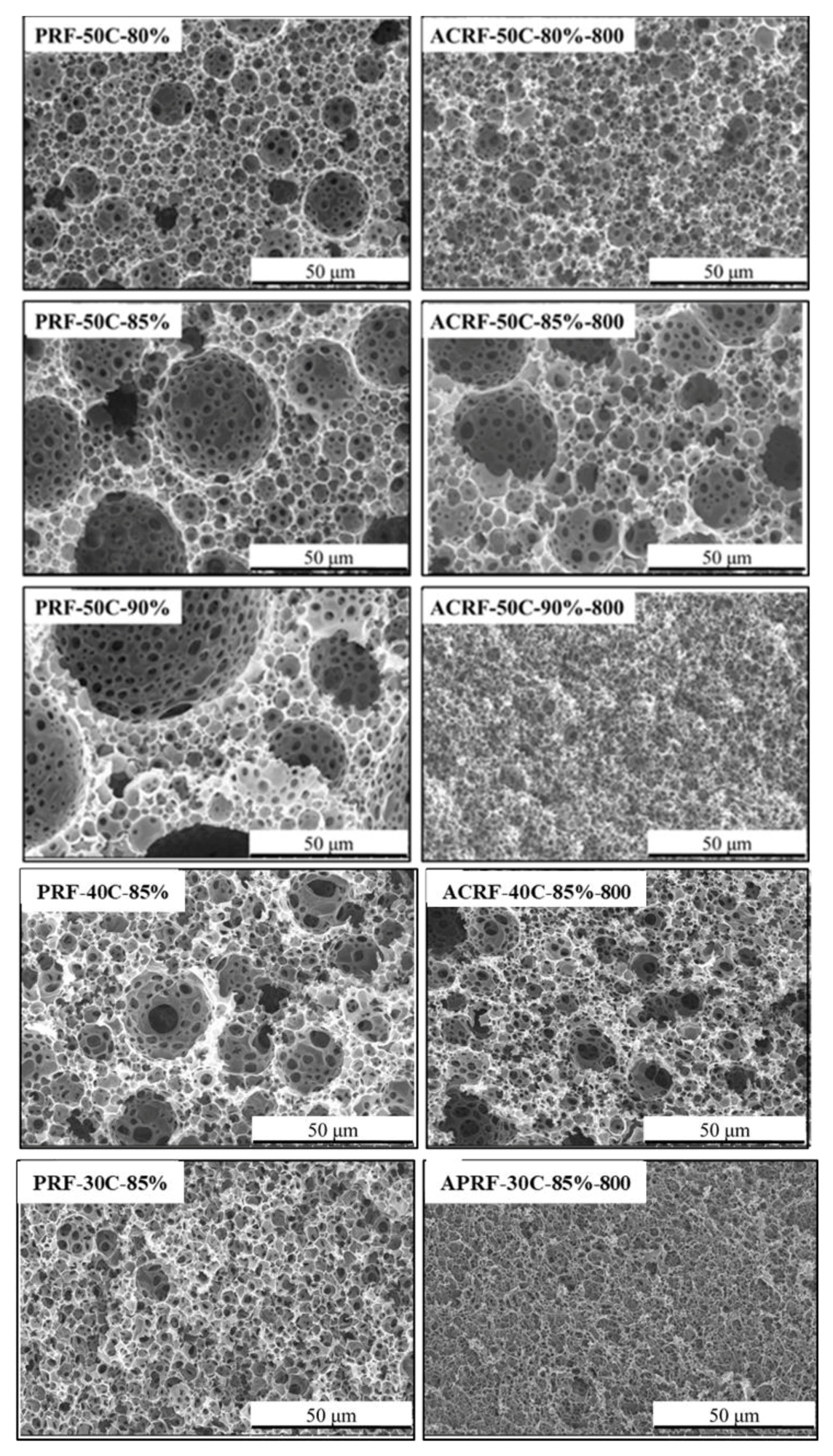
Figure 3. Scanning electron microscope (SEM) images of PRFs and corresponding ACRFs. Image Credit: Duan et al., 2021.
Figure 4 shows the N2 adsorption-desorption isothermals of all the ACRFs and the results showed that there were abundant micropores in ACRFs.
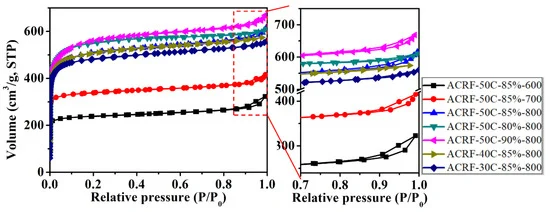
Figure 4. N2 adsorption-desorption isotherms of ACRFs at 77 K. Image Credit: Duan et al., 2021.
Micropores were dominant in all of the ACRFs and were mostly ultra-micropores (sizes below 0.7 nm) (Figure 5).
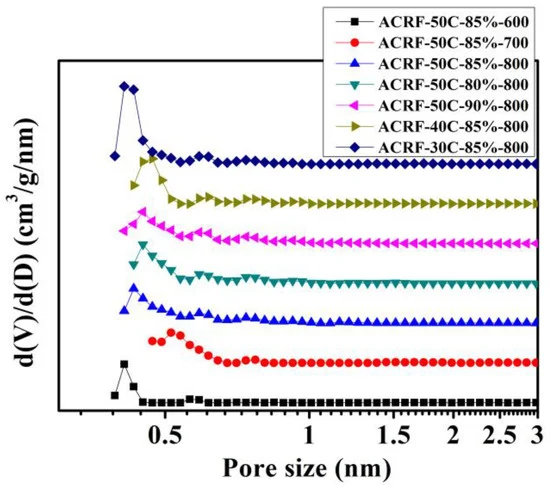
Figure 5. Pore size distributions of ACRFs. Image Credit: Duan et al., 2021.
CO2 Capacity of ACRFs at 1 Bar
Figure 6 shows the CO2 adsorption isothermals of all the ACRFs. The same is listed in Table 1.
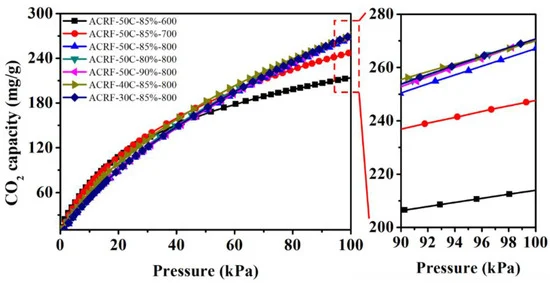
Figure 6. CO2 capacities of ACRFs at 273 K. Image Credit: Duan et al., 2021.
Table 1. Specific surface areas, pore volume, and CO2 capacities of ACRFs. Source: Duan et al., 2021.
Carbon
Foam |
Specific Surface Areas 1 m2/g |
Total Pore Volume 2 cm3/g |
Micropore Volume 3 cm3/g |
Ultra-Micropore Volume 3 cm3/g |
Micropore Volume/Total Pore Volume |
CO2 Capacity 4 mg/g |
ACRF-50C-85%-600 |
879 |
0.433 |
0.349 |
0.333 |
0.806 |
214 |
ACRF-50C-85%-700 |
1237 |
0.558 |
0.489 |
0.466 |
0.876 |
248 |
ACRF-50C-85%-800 |
1952 |
0.830 |
0.742 |
0.606 |
0.894 |
267 |
ACRF-50C-80%-800 |
2024 |
0.827 |
0.796 |
0.657 |
0.963 |
269 |
ACRF-50C-90%-800 |
2046 |
0.900 |
0.817 |
0.635 |
0.908 |
271 |
ACRF-40C-85%-800 |
1944 |
0.783 |
0.737 |
0.616 |
0.941 |
271 |
ACRF-30C-85%-800 |
1871 |
0.771 |
0.713 |
0.633 |
0.925 |
270 |
1 Calculated BET surface area over the pressure range of 0.01–0.2 P/P0 values.
2 Calculated by DFT method, cumulative pore volume under 2 nm.
3 Calculated by DFT method, cumulative pore volume under 0.7 nm.
4 Measured at 273 k, 1 bar.
Figure 7 shows the relationships of CO2 capacities with porosity. The high adsorption potential of ultra-micropores might be the factor that determines CO2 capacity at 1 bar.
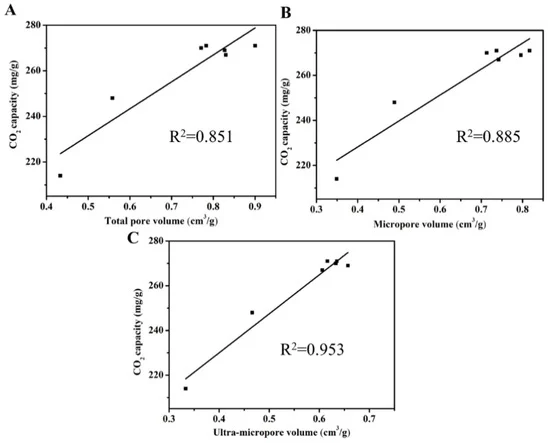
Figure 7. Relationships between CO2 capacities and total pore volume (A), micropore volume (B), and ultra-micropore volume (C). Image Credit: Duan et al., 2021.
Effect of Oxygen Content on the CO2 Capacities of ACRFs
The influence of oxygen content on the CO2 capacity of ACRFs was analyzed, and the results interpreted showed that an increase of oxygen in ACRFs improves the interaction between carbon surface and the CO2 molecule. This is important for ACRFs to capture CO2 at low pressure.
Effect of Macropores on CO2 Adsorption Kinetics of ACRFs
Figure 8 depicts the CO2 adsorption kinetics of ACRF-30C-85%-800 and ACRF-40C-85%-800. The analyses also confirmed the accelerating effect of macropores on CO2 adsorption kinetics.
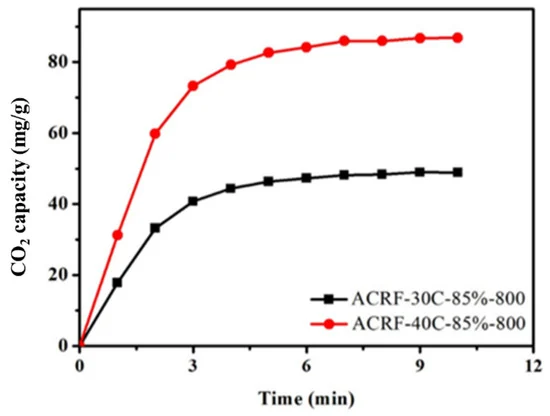
Figure 8. Comparison of the CO2 adsorption kinetics of ACRF-40C-85%-800 and ACRF-30C-85%-800. Image Credit: Duan et al., 2021.
CO2 Adsorbing Properties of ACRF-40C-85%-800
More analyses were carried out on the CO2 adsorbing behaviors of ACRF-40C-85%-800. The CO2 adsorption kinetics was carried out as shown in Figure 9.
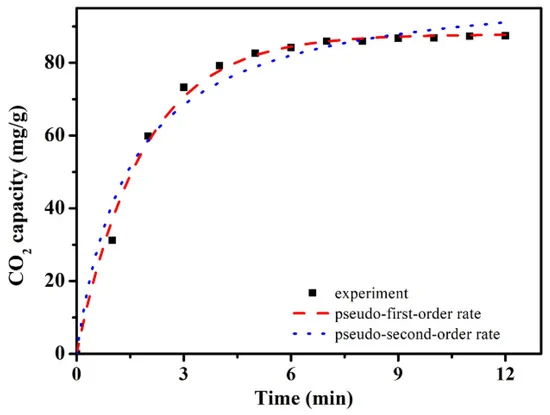
Figure 9. CO2 adsorption kinetics of ACRF-40C-85%-800. Image Credit: Duan et al., 2021.
Table 2 shows the kinetics model parameters for CO2 adsorption.
Table 2. Kinetics model parameters for CO2 adsorption. Source: Duan et al., 2021.
Sample |
Pseudo-First-Order Model |
Pseudo-Second-Order model |
ACRF-40C-85%-800 |
qe (mg/g) |
87.8 |
qe (mg/g) |
102 |
k1 (min-1) |
0.544 |
k2 (min-1) |
0.00655 |
R2 |
0.994 |
R2 |
0.975 |
The kinetics data was also analyzed with the micropore diffusion model. The CO2 selectivity adsorption over N2 was measured by the adsorption isotherms of CO2 and N2 at 273 K (Figure 10A). The results showed the competitive adsorption mechanism. It showed that they tended to adsorb CO2 over N2, and can selectively capture CO2 over N2 from a mixed gas feed stream.
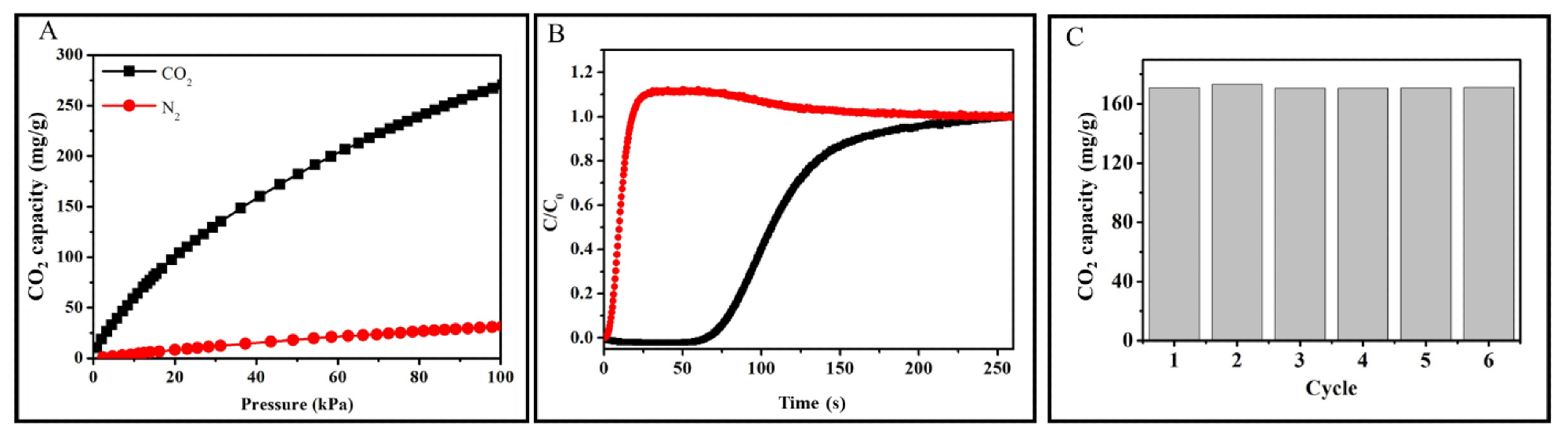
Figure 10. CO2 and N2 adsorption isothermals of ACRF-40C-85%-800 at 273 K (A); breakthrough curves of CO2/N2 of ACRF-40C-85-800 at 298 K (B); CO2 capacity at 298 K of ACRF-40C-85%-800 for six cycles (C). Image Credit: Duan et al., 2021.
The reproducibility of ACRF-40C-85%-800 revealed the same capacity as the first cycle even after the sixth cycle showing good reproducibility.
Figure 11 shows the CO2 adsorption heat calculated by Clausius−Clapeyron.
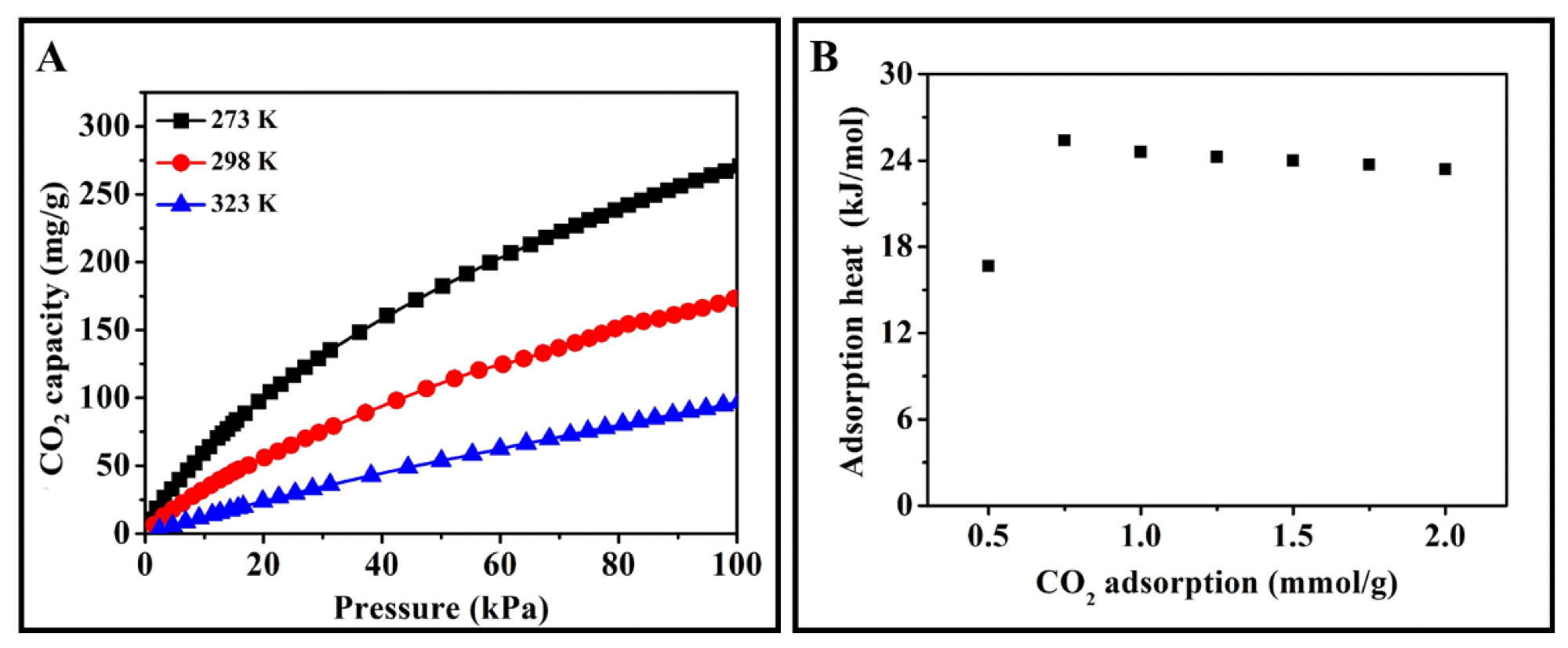
Figure 11. CO2 adsorption isothermals (A) and CO2 adsorption heats (B) of ACRF-40C-85%-800. Image Credit: Duan et al., 2021.
Conclusion
This article puts forth a strategy to fabricate monolith-like carbon (ACRFs) with macropores and micropores. The micropores were created by the activation effect of KOH, and the macropores by the macroporous precursor.
The macropores in ACRFs accelerated the CO2 adsorption rate. ACRFs also showed moderate CO2 adsorption heat and selective adsorption ability. It is assumed that ACRFs have the potential to be transformed into a CO2 adsorbent with outstanding comprehensive performance.
Journal Reference:
Duan, C., Zou, W., Zhongjie, Du., Mi, J., Han, J., Zhang, C. (2021) Construction of Oxygen-Rich Carbon Foams for Rapid Carbon Dioxide Capture. Materials, 4(1), p. 173. doi.org/10.3390/ma14010173.
References and Further Reading
- Zeng, Y., et al. (2016) Covalent organic frameworks for CO2 capture. Advance Materials, 28, pp. 2855–2873. doi.org/10.1002/adma.201505004.
- Jiang, Y., et al. (2018) Simultaneous biogas purification and CO2 capture by vacuum swing adsorption using zeolite NaUSY. Chemical Engineering Journal, 334, pp. 2593–2602. doi.org/10.1016/j.cej.2017.11.090.
- Howarth, A. J., et al. (2016) Best practices for the synthesis, activation, and characterization of metal–organic frameworks. Chemistry of Materials, 29, pp. 26–39. doi.org/10.1021/acs.chemmater.6b02626.
- Das, S., et al. (2016) Porous Organic Materials: Strategic Design and Structure–Function Correlation. Chemical Reviews, 117, pp. 1515–1563. doi.org/10.1021/acs.chemrev.6b00439.
- Xiong, S., et al. (2014) Liquid acid-catalysed fabrication of nanoporous 1,3,5-triazine frameworks with efficient and selective CO2 uptake. Polymer Chemistry, 5, pp. 3424–3431. doi.org/10.1039/C3PY01471A.
- Wang, Y., et al. (2019) Flexible Ketone-bridged organic porous nanospheres: Promoting porosity utilizing intramolecular hydrogen-bonding effects for effective gas separation. Chemical Engineering Journal, 358, pp. 1383–1389. doi.org/10.1016/j.cej.2018.10.046.
- David, S.-T., et al. (2018) Effect of nitrogen doping on the pore texture of carbon xerogels based on resorcinol-melamine-formaldehyde precursors. Microporous and Mesoporous Materials, 256, pp. 190–198. doi.org/10.1016/j.micromeso.2017.08.004.
- Lee, J.-S. M., et al. (2016) Hyperporous carbons from hypercrosslinked polymers. Advanced Materials, 28, pp. 9804–9810. doi.org/10.1002/adma.201603051.
- Shao, L., et al. (2018) Triazine-based hyper-cross-linked polymers with inorganic-organic hybrid framework derived porous carbons for CO2 capture. Chemical Engineering Journal, 353, pp. 1–14. doi.org/10.1016/j.cej.2018.07.108.
- Peng, A., et al. (2019) Fabrication of N-doped porous carbons for enhanced CO2 capture: Rational design of an ammoniated polymer precursor. Chemical Engineering Journal, 369, pp. 170–179. doi.org/10.1016/j.cej.2019.03.038.
- Peng, A., et al. (2019) N-doped porous carbons derived from a polymer precursor with a record-high N content: Efficient adsorbents for CO2 capture. Chemical Engineering Journal, 372, pp. 656–664. doi.org/10.1016/j.cej.2019.04.190.
- Chen, C., et al. (2018) Template-free synthesis of hierarchical porous carbon with controlled morphology for CO2 efficient capture. Chemical Engineering Journal, 353, pp. 584–594. doi.org/10.1016/j.cej.2018.07.161.
- Bing, X., et al. (2016) Template-free synthesis of nitrogen-doped hierarchical porous carbons for CO2 adsorption and supercapacitor electrodes. Journal of Colloid and Interface Science, 488, 207–217. doi.org/10.1016/j.jcis.2016.10.076.
- Tian, W., et al. (2018) One-step synthesis of flour-derived functional nanocarbons with hierarchical pores for versatile environmental application. Chemical Engineering Journal, 347, pp. 432–439. doi.org/10.1016/j.cej.2018.04.139.
- Singh, J., et al. (2019) Synthesis of sulphur enriched carbon monoliths for dynamic CO2 capture. Chemical Engineering Journal, 374, pp. 1–9. doi.org/10.1016/j.cej.2019.05.147.
- Kutorglo, E. M., et al. (2019) Nitrogen-rich hierarchically porous polyaniline-based adsorbents for carbon dioxide (CO2) capture. Chemical Engineering Journal, 360, pp. 1199–1212. doi.org/10.1016/j.cej.2018.10.133.
- Zhang, S., et al. (2018) Synthesis of emulsion-templated magnetic porous hydrogel beads and their application for catalyst of fenton reaction. Langmuir, 34, pp. 3669–3677. doi.org/10.1021/acs.langmuir.8b00009.
- Zhang, N., et al. (2018) Dual-templating synthesis of compressible and superhydrophobic spongy polystyrene for oil capture. Chemical Engineering Journal, 354, pp. 245–253. doi.org/10.1016/j.cej.2018.07.184.
- Azhar, U., et al. (2017) A cationic fluorosurfactant for fabrication of high-performance fluoropolymer foams with controllable morphology. Materials & Design, 124, pp. 194–202. doi.org/10.1016/j.matdes.2017.03.064.
- Sethia, G & Sayari, A (2016) Activated carbon with optimum pore size distribution for hydrogen storage. Carbon, 99, pp. 289–294. doi.org/10.1016/j.carbon.2015.12.032.
- Bedin, K. C., et al. (2019) KOH-activated carbon prepared from sucrose spherical carbon: Adsorption equilibrium, kinetic and thermodynamic studies for Methylene Blue removal. Chemical Engineering Journal, 286, pp. 476–484. doi.org/10.1016/j.cej.2015.10.099.
- Alabadi, A., et al. (2016) Highly porous activated carbon materials from carbonized biomass with high CO2 capturing capacity. Chemical Engineering Journal, 281, 606–612. doi.org/10.1016/j.cej.2015.06.032.
- Liu, J., et al. (2018) Three-dimensional hierarchical and interconnected honeycomb-like porous carbon derived from pomelo peel for high performance supercapacitors. Journal of Solid State Chemistry, 257, 64–71. doi.org/10.1016/j.jssc.2017.07.033.
- Lillo-Ródenas, M.A., et al. (2003) Understanding chemical reactions between carbons and NaOH and KOH: An insight into the chemical activation mechanism. Carbon, 41, 267–275. doi.org/10.1016/S0008-6223(02)00279-8.
- Liu, Z., et al. (2013) Moisture-resistant porous polymer from concentrated emulsion as low-cost and high-capacity sorbent for CO2 capture. RSC Advances, 3, pp. 18849–18856. doi.org/10.1039/C3RA43597K.
- Zhang, X., et al. (2015) Fabrication of porous polyurethane monoliths on strengthening interface of concentrated emulsion polymerization. Materials Chemistry and Physics, 164, pp. 78–84. doi.org/10.1016/j.matchemphys.2015.08.025.
- Woodward, R. T., et al. (2016) A. Hierarchically porous carbon foams from pickering high internal phase emulsions. Carbon, 101, pp. 253–260 doi.org/10.1016/j.carbon.2016.02.002.
- Sing, K. S (1985) Reporting physisorption data for gas/solid systems with special reference to the determination of surface area and porosity (Recommendations 1984). Pure and Applied Chemistry, 57, pp. 603–619. doi.org/10.1351/pac198557040603.
- Lin, Y., et al. (2019) Heteroatom-doped sheet-like and hierarchical porous carbon based on natural biomass small molecule peach gum for high-performance supercapacitors. ACS Sustainable Chemistry & Engineering, 7, pp. 3389–3403 doi.org/10.1021/acssuschemeng.8b05593.
- Ren, X., et al. (2017) N-doped porous carbons with exceptionally high CO2 selectivity for CO2 capture. Carbon, 114, pp. 473–48. doi.org/10.1016/j.carbon.2016.12.056.
- Gu, S., et al. (2016) Facile carbonization of microporous organic polymers into hierarchically porous carbons targeted for effective CO2 uptake at low pressures. Facile Carbonization of Microporous Organic Polymers into Hierarchically Porous Carbons Targeted for Effective CO2 Uptake at Low Pressures. ACS Applied Materials & Interfaces, 8, pp. 18383–18392. doi.org/10.1021/acsami.6b05170.
- He, J., et al. (2016) Tunable polyaniline-based porous carbon with ultrahigh surface area for CO2 capture at elevated pressure. Advanced Energy Materials, 6, p. 1502491. doi.org/10.1002/aenm.201502491.
- Zhu, X., et al. (2016) In situ doping strategy for the preparation of conjugated triazine frameworks displaying efficient CO2 capture performance. Journal of the American Chemical Society, 136, pp. 11497–11500. doi.org/10.1021/jacs.6b07644.
- Chen, W., et al. (2019) Template-free and fast one-step synthesis from enzymatic hydrolysis lignin to hierarchical porous carbon for CO2 capture. Microporous and Mesoporous Materials, 280, pp. 57–65. doi.org/10.1016/j.micromeso.2019.01.042.
- Yuan, M., et al. (2018) Premodified sepiolite functionalized with triethylenetetramine as an effective and inexpensive adsorbent for CO2 capture. Industrial & Engineering Chemistry Research, 57, pp. 6189–6200. doi.org/10.1021/acs.iecr.8b00348.
- Ruthven, D.M., et al. (1994) Pressure Swing Adsorption; VCH: New York, NY, USA
- Kuang, W., et al. (2017) Phenol-modified hyper-cross-linked resins with almost all micro/mesopores and their adsorption to aniline. Journal of Colloid and Interface Science, 487, pp. 31–37 doi.org/10.1016/j.jcis.2016.09.076.
- Myers, A. L & Prausnitz, J.M (1965) Thermodynamics of mixed-gas adsorption. AlChE Journal, 11, pp. 121–127. doi.org/10.1002/aic.690110125.
- Kaur, B., et al. (2019) Chemically activated nanoporous carbon adsorbents from waste plastic for CO2 capture: Breakthrough adsorption study. Microporous and Mesoporous Materials, 282, pp. 146–158. doi.org/10.1016/j.micromeso.2019.03.025.
- Wang, Q., et al. (2016) Control of uniform and interconnected macroporous structure in polyHIPE for enhanced CO2 adsorption/desorption kinetics. Environmental Science & Technology, 50, pp. 7879–7888. doi.org/10.1021/acs.est.6b00579.