AZoCleantech speaks with Markus Leidinger, Application Manager, and Arnd Ohme, Business Development & Platform Manager at Aerzener Maschinenfabrik, about Liebenwalde, a wastewater treatment plant in the east of Germany, and its journey from a failing plant to a successful one. In 2018, the plant was in very poor condition. Liebenwalde was considered to be one of the worst wastewater treatment plants regarding energy efficiency, and the plant had no money to change that.
Why was this project considered a mission impossible?
Markus Leidinger: The energy consumption of the entire plant was 560,000 kilowatt-hours per year. The plant manager faced a capacity increase of 42%. The oxygenation in the aeration basin was only 0.5 milligrams per liter. However, the required value was and still is 1.5 milligram per liter. These bad values can primarily form an old and defective pipe membrane diffuser aeration system combined with an old and economical blower system.
The energy evaluation of the plant was extremely bad, with 42 kilowatt-hours per population equivalent per year. Thus, it was a very, very big challenge. Nonetheless, together with an expert company for the current application, we were able to regenerate a funding program. Within three years, three different treatment processes were completely rebuilt.
We started in 2019 with a new fine bubble aeration system, including new rotary piston compressors, a second grit chamber, and two new rakes. The investment cost amounted to 700,000 euros. We got 80% funding for this project, and this corresponds to 550,000 euros. In 2020, a new sludge humification plant was built, which cost 2 million euros, and 1.6 million of that was funded. One year later came the photonic photovoltaic system, this cost 220,000 euros, and we were able to optimize the plant with a charming funding program of 2.5 million euros.
Can you provide a brief history of the Liebenwalde wastewater treatment plant?
Markus Leidinger: The plant was constructed in 1992 with a capacity of 14,000 population equivalent. The aeration basin had a volume of 5,400 cubic meters with a water depth of 3.9 meters. The polluting load is lying at 630,000 cubic meters per year. We have an oxygen set point at 1.5 milligrams per liter, and the big challenge was the 42% capacity increase due to truck deliveries from the neighboring communities.
The previous operating mode in the oil compressor room consisted of three blowers that were over 30 years old that were delivering intermittent air into the aeration basin via an old pipe membrane diffuser. The installed power for each machine was 18.5 kilowatts. We had a volume flow of 950 cubic meters per hour per machine. And the pressure difference was 520 milligram. All machines ran together for 15 hours in full load operation mode.
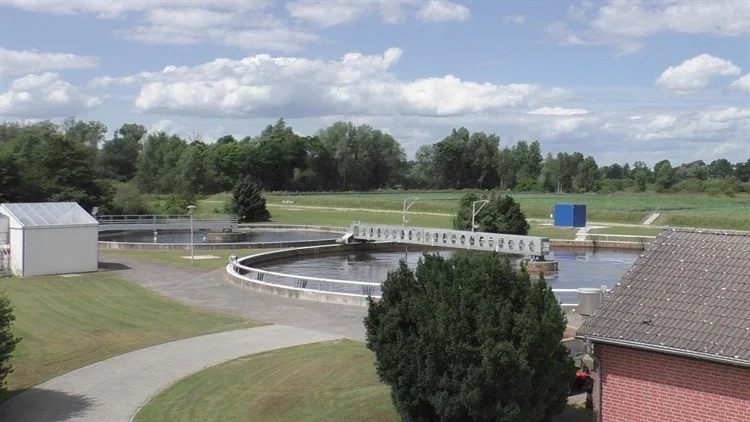
Image Credit: Aerzener Maschinenfabrik GmbH
What are the disadvantages of this outdated aeration system?
Markus Leidinger: There were many disadvantages with this old aeration system; the pipe membrane diffusers were inefficient and partly defective due to aging. This can be seen in the turbulent water surface in the aeration tank. The old blowers were uneconomic and so were equipped without a frequency converter. All these circumstances were responsible for a bad oxygen value of 0.5 milligrams per liter.
It was also very difficult to get new spare parts due to the aging of all the components. In terms of energy efficiency, we had high pressure losses because of our long pipelines up to the basin. The complete system was uneconomical, and a 42% capability increase was still not possible.
How did you overcome the challenges associated with this old system?
Markus Leidinger: To resolve these issues, the customer opted for an entirely new aeration system. We placed two Delta Hybrid machines in a container solution as close as possible to the aeration basin. In this way, we avoided unnecessary pressure loss into the pipe systems. Via a collecting pipe, the air entered the aeration basin in intermittent operation. Inside of the basin, we installed a fine bubble membrane aeration system.
How did the new AERZEN container solution perform?
Markus Leidinger: In our container, we packed two Delta Hybrid D 52 S machines. Both machines have exactly the same performance data. The machines are configured for a volume flow between 800 to 2,500 cubic meters per hour. The installed power is 55 kilowatts per machine, and the pressure difference is only 450 milligrams. The machines run in frequency converter mode for 13 hours per day.
The container solution saved considerable costs in terms of CAPEX and OPEX. The station was built as close as possible to the aeration basin. In this way, we were able to guarantee the lowest pressure loss in the pipe system, saving considerable energy and money.
A short pipe system to the basin saved money in terms of both material cost and pipeline cost. We did not need a new compressor building, and with the outdoor installation, we had the best possible oxygen input into the biology. The conveying chamber of the machine is 100% oil-free. Our sound absorber has no absorption material, and therefore we avoid a blocking of the aeration plates from inside over the years.
With all this action we could realize a cost reduction of more than 200,000 euros.
How does the energy comparison between the old compressor system and the new compressor systems compare?
Markus Leidinger: When considering energy, there are two very important things to consider. The new machines run with a frequency converter. The control unit is able to decide whether one or two machines need to run. With the old solution, the only option is to start or stop all three machines at the same time, and the aeration process is 15 hours. The new solution brings significant energy cost savings.
In 2017, the plant required 294,000 kilowatt-hours of energy, but with the new solution in 2021, only 160, 000 kilowatt-hours were required, and that is with a 42% increase in capacity. This means we can save 47% energy, which is equivalent to 30,000 euros per year.
In short, there has been a 47% energy saving despite there being a 42% capacity increase, 80% of the plant investment cost was funded, the plant saved over 65,000 euros a year on energy, and new solar power was installed that had a capacity for 130,000 kilowatt-hours per year. A top value of 17-kilowatt hours per population equivalent per year was obtained, and CO2 emissions were reduced by 210 tons per year.
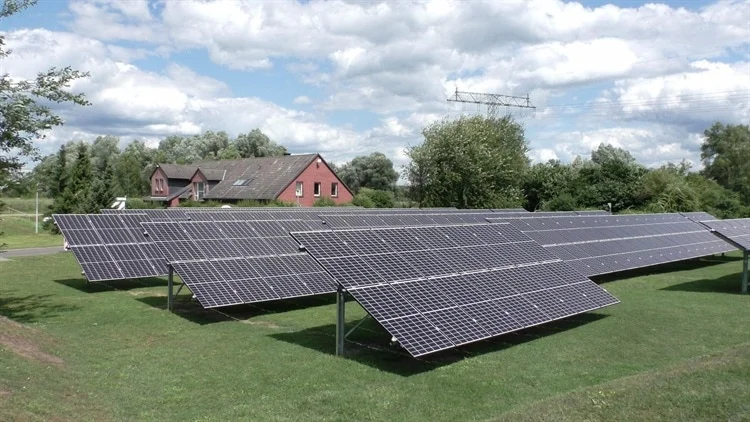
Image Credit: Aerzener Maschinenfabrik GmbH
Please could you introduce yourself and your role at AERZEN Systems?
Arnd Ohme: My name is Arnd Ohme, and I am the Business Development Manager at AERZEN Systems. Using my experience, I would like to inform you of how digital services can optimize machine maintenance with more transparency and intelligent machine data analytics.
Using intelligent machine data analytics, how can digital services help to optimize machine maintenance?
Arnd Ohme: Customers often discuss machine maintenance. One customer told me that in order to understand the condition of a machine, I would have to go and visit the machine on site. However, as Business Development Manager, I am often extremely busy and thus do not have the time to physically go to the machine on site. Moreover, some customers replace parts on a recurring basis, regardless of the condition of the parts. This also means spending money unnecessarily.
On the other end of the spectrum, we document the maintenance work on paper and file it in a folder, which is very old school. Thus, in the event of a failure, we would sometimes have to spend more time looking for the case as we do not have detailed machine data records.
Therefore, when we look at preventive maintenance, the goal here is to replace components before they fail. And this is the most common maintenance strategy. Here components are replaced regardless of their condition but based on the time in which they have been in use. It does not matter whether the machine has high or low utilization. In wastewater treatment plans, the blowers do not run permanently and with different loads. This results in a different type of wear than blowers that run permanently on the full load. But this usage-based maintenance is more suitable as a form of preventive maintenance.
There is a huge difference between preventive maintenance and predictive maintenance, especially for machines that do not work permanently with the same load. Thus, predictive maintenance results in an optimization of the maintenance interval base on the condition of the machine, especially when the machine load is lower and the operation time is less. Maintenance intervals can be optimized as needed, which can ultimately result in cost savings.
By collecting machine data and data analytics, the optimal time for maintenance can be defined much better. Furthermore, there are fewer undiscovered cases of higher wear and tear.
How can AERprogress Condition Monitoring be used to help monitor maintenance needs?
Arnd Ohme: With our product AERprogress Condition Monitoring, we collect the machine data like pressure and temperatures together with the vibration at the bearing of the stage and the engine. This data is then analyzed using a modern algorithm, and the health index of the machine as a whole, and individual wear parts are calculated from it.
In practice, the pressure and temperature data, as well as the operating hours, come from the machine control system, the AERtronic. With additional vibration sensors at the bearings of the stage and the drive motor, the bearing vibrations are measured in detail. This data is then sent to the AERprogress cloud, where the AERZEN IoT gateway uses mobile communications.
In the cloud, the data is stored and analyzed with the modern algorithm. You, as a user, have access to the data and information via a web interface using a web browser. The data communication is secured by using a high level cyber security mechanism.
As a user, you can easily access the AERZEN Digital Platform with any web browser and your user account. Via the digital platform, you also receive information when limit values are exceeded and information about the health index of the blower and the relevant wear parts. This allows you to easily and quickly get an overview of the condition of your blower at any time from anywhere.
This health index is very smart. In the background of the digital platform, complex and intelligent calculations are being run. Using our intelligence data analytics algorithm based on the received machine date, a clear overview of the health of the machine can be obtained. With this information, you have the time to clearly and easily understand information about the condition of the relevant components of your machine.
Can you provide some examples of how the AERprogress Condition Monitoring program can potentially be used to monitor machine maintenance?
Arnd Ohme: First, I will use an example that is based on a wastewater treatment plant with a D 52 S blower and outline how, with optimal maintenance, savings can be made.
In the past, a customer only used to change their air filter once a year. The air filter was thus always clogged, which means that the energy consumption of the machine continuously increased to work against the clogging. As a result, the energy consumption and operating costs increased accordingly.
To help, we updated the machine with progress-condition monitoring. The permanent operating data analytics of progress condition monitoring showed that based on the clogging of the filter, a filter change four times a year is optimal.
The customer, as a result of this clogging, also has higher maintenance costs. Thus, upon following the advice of the condition monitoring program, he saw a reduction in total operating costs by approximately 1,711 euros a year. Thus, savings enabled by using condition monitoring would allow the customer to pay off the investment after less than three years. Based on this and the fact that energy prices are currently rising very sharply, the payoff could possibly be even earlier.
The additional vibration monitoring of the bearings has so far shown that the bearings at the time of the time-based maintenance did not have sufficient wear; therefore, a replacement was not yet necessary. The customer, in turn, saved additional costs for the maintenance of the bearings.
Digital services and intelligent data analytics offer additional added value. They offer additional opportunities to reduce operating costs and increase the service life of the machine.
In short, progress condition monitoring has great potential for money and cost savings. To take advantage of progress condition monitoring and benefit from it with ease, contact Aerzener Maschinenfabrik GmbH today.
Will the procedure be able to get state funding?
Markus Leidinger: In Germany, you need pretension analysis first, which is then followed by a concept study. This study includes which treatment processes have a high potential for saving energy or reducing CO2 and what concrete replacements are required. Then you can apply for state funding. My experience tells me the processes are similar in every country. It is important to know whether there is a state funding set as the base.
Why didn't the customer in the presentation decide on turbo blowers?
Markus Leidinger: In the case of the wastewater treatment plant in Liebenwalde, using two Delta Hybrid machines was the better solution. Reason number one, with the Delta Hybrids, we can realize a wider volume flow range, and via this flow range, we achieved good energy efficiency. Reason number two, in this case, we could install the power and control cabinet from our machine inclusive to frequency converter in an existing building. This was a significantly cheaper and better solution for the required treatment process.
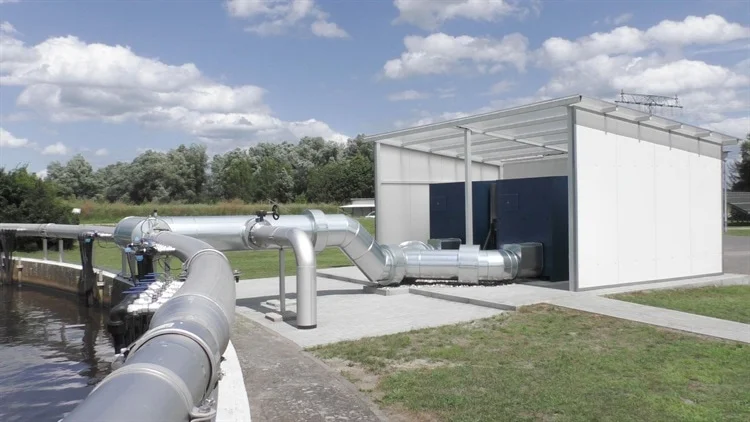
Image Credit: Aerzener Maschinenfabrik GmbH
Do you produce a container solution at Aerzener Maschinenfabrik?
Markus Leidinger: Of course. We are able to deliver and complete a container solution with all the needed components. This includes the machine, of course, the power and control cabinet includes the frequency converter, the room ventilation, the pipe connection, and the digitalization as an option. We deliver a complete block and place solution for the customer.
Digitalization is a big topic for your customer. Is air progress also available without the cloud?
Arnd Ohme: We are focused on the cloud solution because the cloud solution gives us a lot of opportunities and a lot of advantages against a solution that is only placed on site by the customer. The big advantage of this is that all the data comes together in our cloud application, and the data will be used for our automation machine learning for optimizing the complete analytics process and so on. This will benefit our artificial intelligence in many ways.
When you have only a few machines used to train the artificial intelligence for the analytics algorithm, then the learning process is not as powerful as it could be. This is why we focus on cloud applications. The cloud is the best solution for this topic, especially when we are talking about data analytics and machine learning and a lot of artificial processes in the background.
Can the data also be linked to a SCADA system?
Arnd Ohme: There are a lot of different SCADA systems currently on the market with different interfaces. Currently, we are offering the Modbus/TCP as a standard interface; other interfaces are coming in the future. But in practice, not every connection is the same connection, and the interfaces are often different. Thus, there is a point where we have to take a deeper look at the interface of the SCADA system. It is then a decision of what we can do onsite when we have more details from the SCADA system.
Can a hacker manipulate the machine via a cellular connection?
Arnd Ohme: This is something that we are often asked, especially when we are talking about wastewater treatment plants and applications that have special policies around IT security and cybersecurity. During the developing process of our product, we are very strongly focused on this topic. As this is the main issue that we have to solve, and so directly, we developed product and transmission and communication protocols that are very secure. It is based on the German IT Security Guidelines for Critical Infrastructure (Energy supply, water supply, etc.) application and the international ISO 62443 applications. So, we have a very secure application that is state of the art in terms of cybersecurity and IT security.
On the other hand, in terms of the IoT gateway, when we are communicating, the data in the cloud that is transmitted is encrypted, so we have the possibility to bring the data safe to the cloud with no real chance of being able to decrypt it.
At the other end, we have a gateway that works in the same way as a firewall. It blocks wrong and critical access from outside, and as an additional security functionality, in the current summit version of the IoT gateway, it is not possible to control the machine remotely over the IoT gateway. The IoT gateway also blocks reading processes and writing processes.
Markus Leidinger & Arnd Ohme

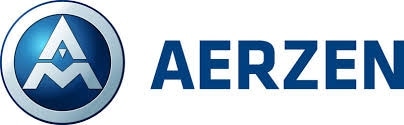
This information has been sourced, reviewed and adapted from materials provided by Aerzener Maschinenfabrik GmbH.
For more information on this source, please visit Aerzener Maschinenfabrik GmbH
Disclaimer: The views expressed here are those of the interviewee and do not necessarily represent the views of AZoM.com Limited (T/A) AZoNetwork, the owner and operator of this website. This disclaimer forms part of the Terms and Conditions of use of this website.