AZoCleantech speaks to Michael O’Kronley, CEO of Ascend Elements, about the importance of battery recycling for the environment and the future of the electric vehicle industry. This interview highlights the innovative technology, challenges, and collaborations driving Ascend Elements' mission to create a closed-loop source of battery materials, reducing the need for mining and advancing a more eco-friendly future for electric vehicles.
Can you explain the importance of recycling lithium batteries and how it contributes to sustainability in the electric vehicle (EV) industry?
Lithium-ion batteries power the global clean energy transition in electric vehicles and grid-scale applications with wind, solar, and hydroelectric power. But the sun does not always shine, and the wind does not always blow, so lithium-ion batteries are needed to store the renewable energy produced.
When batteries reach the end of their life, we cannot send them to landfills to contaminate the environment. Even beyond the environmental concerns, lithium, cobalt, and nickel are in such short supply that we cannot allow these elements to go into landfills. Our goal is to keep 100% of lithium-ion batteries out of landfills. Once critical battery materials are pulled out of the earth at a tremendous environmental and societal cost, we are responsible for conserving those elements for repeated use.
By recycling lithium-ion batteries and returning those valuable materials to the EV battery supply chain, we are helping to meet the demand for new EV batteries, minimizing the need for mining and reducing the carbon footprint of new electric vehicles. Ultimately, this helps accelerate the global transition to zero carbon emissions.
Your company emphasizes going beyond battery recycling to manufacture engineered materials for EV batteries. Could you elaborate on why this approach is essential for the industry's future?
Ascend Elements is moving beyond EV battery recycling to engineer and manufacture sustainable engineered cathode precursor (pCAM) and cathode active material (CAM) made with up to 100% recycled lithium-ion battery content to power a new generation of cleaner electric vehicles and accelerate the global transition to zero carbon emissions.
We believe this is essential to the EV industry’s future to help meet the growing demand for critical metals like lithium, nickel, and cobalt and make new electric vehicles as clean and sustainable as possible. The criticism of electric vehicles is that their batteries are often very carbon-intensive, so reducing the carbon footprint of EV batteries will help alleviate that concern.
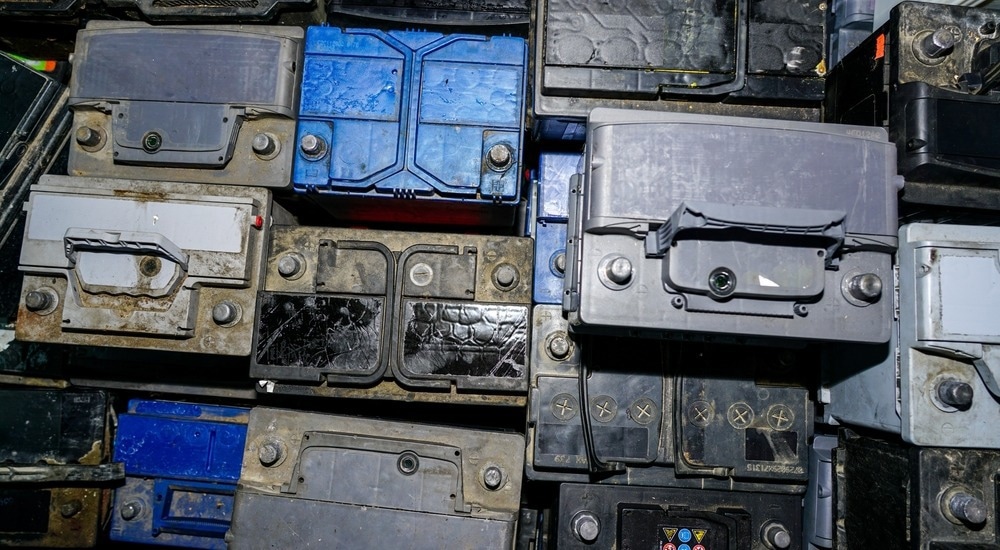
Image Credit: Zigmunds Dizgalvis/Shutterstock.com
Could you describe the process of recycling lithium batteries and how it differs from traditional recycling methods? What are the environmental benefits?
There are several ways to recycle lithium-ion batteries; some are more efficient.
Pyrometallurgy: This traditional method burns and melts the batteries and is very energy and carbon-intensive, producing commodity metals that may or may not go back into the battery supply chain.
Hydrometallurgy: Another way (hydrometallurgy) eliminates burning but still requires many intermediate steps and produces commodities metals that may or may not go back into the battery supply chain.
Hydro-to-Cathode®: Our Hydro-to-Cathode® direct precursor synthesis technology is similar to hydrometallurgy, but is much more efficient. It is purpose-built for recycling lithium-ion batteries and is the best approach for a truly circular supply chain.
Hydro-to-cathode is the most efficient and economical way to return used batteries and scrap to the electric vehicle battery materials supply chain. This technology produces premium, sustainable precursor (pCAM) and cathode active material (CAM) according to customer specs. This process ensures critical battery materials stay in the battery supply loop. The key to our efficiency and reduced cost is direct precursor synthesis. Rather than extracting individual metals in series, our process extracts impurities from the combined metals and allows us to adjust the elemental ratio to produce any cathode material specified.
What are the key challenges in recycling lithium batteries and ensuring the materials can be used in new EV batteries?
It is essential to define what we mean by “recycling.” You can put a lithium-ion battery in a recycling bin at a big box store and say you have recycled that battery, but what happens to it next?
Some companies process old lithium-ion batteries into a raw material called black mass. That is recycling, but that material needs further processing before returning to new electric vehicle batteries. So, recycling does not necessarily mean circularity. We are focused on transforming the raw materials produced by recycling operations, including ours, into an engineered EV battery material called pCAM or CAM. These materials can return to new EV batteries, which is true circularity.
Can you provide insights into the technology and innovation behind your company's approach to producing engineered materials for new EV batteries?
Ascend Elements’ Hydro-to-Cathode® direct precursor synthesis process transforms a mixed stream of used lithium-ion batteries and manufacturing scrap into active, battery-grade cathode material – maximizing the value of these materials while driving down costs and carbon emissions.
Other processes leach metals out of spent battery materials, but our patented process leaches out impurities, keeping the valuable cathode materials intact and in solution. This eliminates multiple steps in the recycling process for lower GHG emissions and energy use.
How do these engineered materials compare in terms of performance, cost, and sustainability with traditional materials used in battery production?
Several peer-reviewed studies have shown Ascend Elements’ recycled battery materials perform as well as similar materials made from virgin (or mined) sources. This independent research has been instrumental in alleviating automotive industry concerns about the use and performance of recycled battery materials.
Today, major electric vehicle OEMs and manufacturers use recycled battery materials and sustainable cathode (pCAM and CAM) from Ascend Elements to accelerate their net zero and zero carbon emission goals. Made locally from recycled lithium-ion batteries using our patented Hydro-to-Cathode® process, carbon emissions can be reduced by up to 90% compared to traditional cathode manufacturing methods.
From a cost perspective, making new cathode material from recycled battery feedstock is much more economical than using virgin metals.
What kind of partnerships or collaborations does your company engage in to ensure a steady supply of lithium battery materials for new EV batteries?
Many people do not understand that the most significant source of lithium-ion battery material to be recycled today comes from gigafactory manufacturing scrap, not end-of-life batteries. We work with many EV battery manufacturers, including SK Battery America, to recycle truckloads of gigafactory manufacturing scrap daily. We also work with electric vehicle OEMs like Honda and others to recycle end-of-life batteries.
In the context of the growing EV market, how do you see the demand for sustainable lithium battery materials evolving in the coming years?
Using recycled lithium-ion battery materials is essential to meet industry demand for battery materials and offset the need to mine new metals out of the earth. Recycled EV battery materials from Ascend can also help reduce the carbon footprint of electric vehicles, which is why companies like Honda Motor Co. see recycled battery materials as an essential tool to achieve zero environmental impacts by 2050.
Ascend Elements also began commercializing its Hydro-to-Anode® graphite recovery and purification process in 2023. While graphite recycling is nothing new, traditional methods do not produce a battery-grade product. The graphite recovered in most battery recycling processes is typically of a lower purity and must be used in non-battery applications. However, Ascend Elements’ Hydro-to-Anode® process can produce 99.9% pure graphite, above battery grade. It is a game changer for the industry.
What is the role of government policies and regulations in promoting sustainable battery materials production and recycling, and how do these factors impact your company's operations?
First and foremost, you need a good business model that can be profitable regardless of the regulatory environment.
EV battery recycling is a capital-intensive endeavor, and the Bipartisan Infrastructure Law (BIL) is helping to fund many essential battery materials infrastructure projects in the United States, including our Apex 1 cathode manufacturing project in Hopkinsville, Ky.
Ascend Elements is focused on constructing this one-of-a-kind facility on a 140-acre site in southwest Kentucky. The 1-million-square-foot facility will produce enough sustainable pCAM for 750,000 electric vehicles annually. Building a facility of this size and scope requires significant capital.
The Inflation Reduction Act (IRA) creates additional demand for our custom-engineered battery materials, which is good for business.
How does your company address concerns related to the scalability of sustainable battery materials production to meet the increasing demand for EVs?
Access to capital is the most significant barrier to scalability. EV battery recycling is a capital-intensive endeavor.
In September 2023, Ascend Elements announced $542 million in new equity investments, including $460 million in Series D investments and $82 million of additional investments.
Ascend Elements’ Series D round was led by Decarbonization Partners, Temasek, and Qatar Investment Authority (QIA). The $542 million investment will be paired with two U.S. Department of Energy grants totaling $480 million, part of the Bipartisan Infrastructure Law (BIL).
Are there any ongoing research and development efforts within your company to further enhance the sustainability and performance of engineered materials for EV batteries?
Yes. Ascend Elements was founded on innovation. Our co-founders filed the first patent for an ultra-efficient EV battery cathode precursor synthesis process in 2012 at Worcester Polytechnic Institute. Today, we have 77 patents granted or pending - all of them focused on improving the circularity of EV battery materials.
In addition to our research into cathode precursor synthesis, we are actively researching graphite purification processes to recover battery-grade graphite from used lithium-ion batteries. We are also developing a new process to recover nickel from a lower-cost feedstock called MHP.
Lastly, how does your company envision contributing to a more sustainable and eco-friendly future for the electric vehicle industry?
Ascend Elements is helping prepare for the tsunami of retired and end-of-life EV batteries expected in the coming decade. By unlocking the total value of used EV batteries and improving the economic return on recycling, Ascend Elements’ innovative technology may be the best way to increase recycling rates and keep potentially hazardous battery materials out of landfills. The Ascend Elements process creates a genuinely closed-loop source of new battery materials, minimizing the need to mine nickel, cobalt, and lithium.
Concerns about electric vehicles' sustainability and environmental impact are significant for many people considering an EV purchase. Mining for cobalt, nickel, and lithium can have significant environmental, safety, and social justice impacts. Unsafe work conditions and child labor have been associated with mining operations in central Africa.
Mining is an energy-intensive activity that generates significant greenhouse gas emissions. Sourcing critical battery metals via recycling or “urban mining” is far more environmentally friendly, socially just, and energy efficient. Ascend’s recycling technology recovers 98% of the critical metals in used lithium-ion batteries and will offset the need for mining.
Where can readers find more information?
https://ascendelements.com/
https://www.scientificamerican.com/article/recycled-lithium-ion-batteries-can-perform-better-than-new-ones/
https://www.sciencedirect.com/science/article/pii/S2542435121004335
Ascend Elements will attend the Advanced Automotive Battery Conference on 11-14 December 2023, putting recycled battery materials on the agenda and examining the steps needed to develop new, battery-ready cathode active material (CAM).
About Michael O’Kronley
Michael O’Kronley was named CEO of Ascend Elements in March 2020 and has served on the company's board since 2017. Before Ascend Elements, he was Head of Corporate Strategy at A123 Systems.
He has worked in the automotive and EV battery industries for over 25 years, with previous business development, operations and engineering roles at Metaldyne Corp. and Robert Bosch. He holds bachelor's and master's degrees in Engineering from the University of Michigan.
Disclaimer: The views expressed here are those of the interviewee and do not necessarily represent the views of AZoM.com Limited (T/A) AZoNetwork, the owner and operator of this website. This disclaimer forms part of the Terms and Conditions of use of this website.