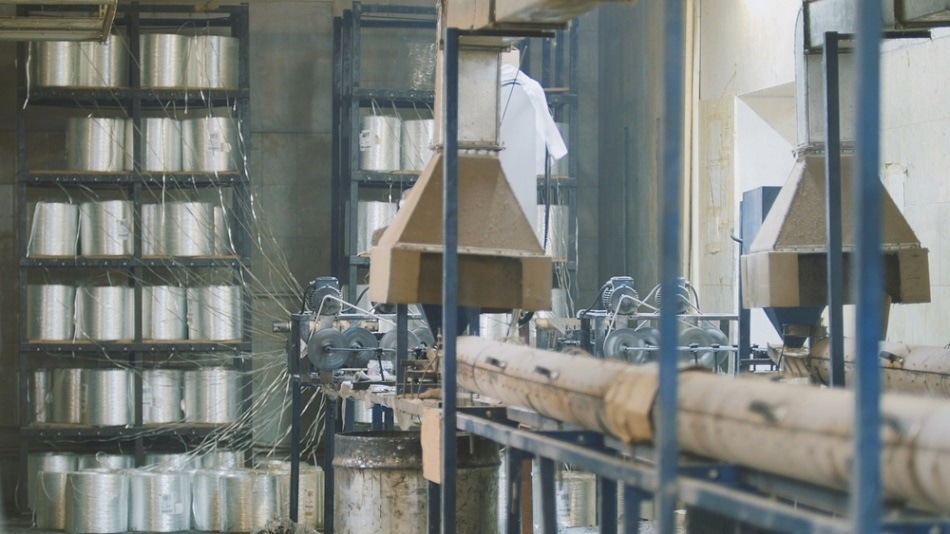
Image Credits: Studio 72/shutterstock.com
Fiber-reinforced plastics (FRP) belong to a category of composite materials which comprise of a polymer matrix and another supporting fibrous material. The matrix is usually a hard thermoset resin, possessing resistance to chemical or abrasive damage. However, it is typically not mechanically robust. The addition of the fiber component produces a new compound with much higher performance.
Typical core polymers include epoxy, polyesters or vinyl ester resins. The fiber used retains its own form but shares its unique characteristics with the matrix, making the new compound lighter, stiffer and mechanically much stronger.
Commonly used fibers are derived from carbon, basalt, glass, wood, hemp, sisal or flax. Natural fibers are cheaper, leave a smaller environmental footprint and are recyclable. They offer excellent thermal and acoustic insulation, are easier to machine, and produce less air pollution and fewer occupational skin and respiratory symptoms.
What advantages do FRP offer over other plastics?
The inclusion of fibers in FRP reduces the weight, and improves the elastic modulus and mechanical strength. As a result, these materials can be used to make components that must be precisely engineered and require predefined tolerance limits, low fatigability, high impact tolerance and good compression properties. They allow simpler component design, boosting production and operational efficiency. FRPs also offer excellent thermal and acoustic insulation and resist corrosive chemical attack, sea wave impact, humid conditions and storm winds/waters.
Important applications of FRP
Some important areas of FRP application include:
- Aerospace industry
- Automotive industry
- Construction field
- Consumer goods
- Power industry
- Protective equipment
- Marine infrastructure
Automotive industry
A high strength-to-weight ratio is the holy grail for the automotive industry. FRPs are valuable as metal substitutes in the bodies of luxury automobiles and in truck and trailer body sidings. With higher fracture points than steel, these strong, stiff and light materials also improve fuel consumption while increasing the speed. They are also easily molded to form the desired components. Almost a third of FRP utilization is in this field.
Glass-FRPs are for engine components like the intake manifold, reducing up to 60% of its weight and streamlining the design. Multiple components can be combined, saving costs. Glass FRPs are weaker and more pliable compared to carbon FRPs.
Gas and clutch pedals may be as single molded units from glass-FRPs instead of aluminum, enhancing production rates at lower cost. The fibers can be oriented as desired for stress-specific strength, increasing component safety.
Construction industry
Over 20% of fiber-reinforced plastics are currently taken up by the construction industry, including bridges and roads. FRPs may be used to retrofit existing structures (as with slabs, columns, or beams) to enhance their load-bearing capacity or to repair damage. This is extremely cost-effective and useful when it comes to equipping older structures which are faced with loads far greater than they were originally designed to bear.
FRPs are also used to manufacture highway structures like guardrails, signboards, drainage systems and bridge decks, as well as auto skyways, utility poles and pipelines for gas, water and sewage.
FRPs may be ideal for building prefabricated houses, while household and business office furniture, household appliances, swimming pools, rain gutters, bathroom equipment and pipe fittings and hoods made of FRPs are already popular.
Aerospace applications
This area uses only about 0.6% of FRPs at present, but with further development and lower environmental costs it will require much more.
Carbon fibers in FRPs reduce the weight by 25% but ensure equal or greater strength when compared to aluminum sheets. They offer excellent tensile strength and tolerate harsh environments and extremes of temperatures. They expand little with heat and possess high stiffness. Though initially expensive, they save money for the aerospace industry where every gram of additional weight is grudged because of the effect on the fuel consumption, journey length and costs, and aerodynamic safety.
Carbon-FRP also allows for complex molded part production, reducing the number of parts by an astonishing 95%. This makes production simpler, faster and cheaper compared to other materials like steel or cast aluminum. Many giant modern aircraft are made of more than 50% carbon-FRP. Helicopter rotor blades on high-end drones are also increasingly being made using FRPs.
Consumer goods
Many sportspeople are finding it easier to heft their equipment nowadays, thanks to the use of carbon and other FRPs in all kinds of sporting goods. Musical instruments or their components, firearms, camping tents and camera tripods have all benefited from these versatile materials, with 6% of FRPs being used in this area.
Protective equipment
When compounds called aramids are used in FRPs, they produce materials with extremely high thermal and impact resistance, and exceptional mechanical strength, ideal for use in bullet-proof and fire-resistant suits, as well as blast protection vehicles and structures.
Marine infrastructure
FRPs are ideal replacements for wood, in marine waterfront environments, or on ships, where they reduce the structural weight and enhance corrosion resistance. Rolling bridges, floating causeways and platforms for sea bases are other applications.
Power industry
FRP demand is expected to grow by over 300% in industry and energy applications over the coming decade, mostly in electronic and electrical components.
Most FRPs are electrically insulative, tolerate rugged environmental chemicals (even corrosive ones), resist degradation due to heat, are relatively non-flammable, have excellent structural integrity, and can tolerate ultraviolet radiation. Glass-FRPs are non-magnetic and also resist sparking, making them useful in power components.
Reinforced plastics are also used to construct wind turbine blades and for the storage modules of gas tanks.
Techniques to improve the strength of FRP composites
Specific 3D printing techniques can increase FRP strength by 30-50% and shear strength by up to 250% compared to their 2D counterparts. Certain nanoparticles may also enhance FRP strength.
Conclusions
While the array of potential applications is dazzling, more technological development is vital to make the process cost-effective and ensure extreme durability of the final FRP component. Materials sciences and production engineering need to join hands to deal with the current issues and make these composites the first choice over a full range of uses.
Sources and Further Reading
Disclaimer: The views expressed here are those of the author expressed in their private capacity and do not necessarily represent the views of AZoM.com Limited T/A AZoNetwork the owner and operator of this website. This disclaimer forms part of the Terms and conditions of use of this website.