Jul 12 2010
Minus 20 degrees Celsius: A frozen pizza must not get any warmer than that before it makes its way into the consumer’s freezer. And polyurethane rigid-foam insulation made by BASF Polyurethanes is an integral part of this logistical “cooling feat”. But the insulation not only has to be efficient in terms of retaining the cold but also has to behave sustainably when it comes to energy and material consumption.
Polyurethane experts from Lemfoerde have conducted an Eco-Efficiency Analysis in order to determine how large the differences are when insulating materials of different thicknesses are used in freezer warehouses or freezer trucks where frozen pizza is stored or transported. The findings indicate that if all of the storage facilities, freezer chests and transport vehicles were to be insulated with polyurethane rigid foam having an optimized insulating thickness, then 16 times more energy could be saved than is needed for the production of the insulating material.
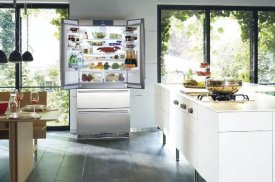
Eco-Efficiency Analysis of the cold chain
Already back in 1996, BASF cooperated with the consultancy Roland Berger to develop the Eco-Efficiency Analysis. It is a comparative instrument that yields a holistic evaluation of products and processes by looking at the entire life cycle of a given object. Using this instrument, BASF Polyurethanes specialists from Lemförde together with the Öko-Institut (Institute for Applied Ecology) in Freiburg, Germany, have examined the eco-balance of the cold chain.
The cold chain starts when a freshly made pizza is quick-frozen and subsequently deep-frozen. It goes to the freezer warehouse, travels in the freezer truck, is put into the freezer chest of the supermarket and then into the freezer of the final consumer. On the average, the journey of a complete pallet of frozen food takes 75 days from the warehouse to the household freezer. If the latest generation of polyurethane insulation made by BASF Polyurethanes is used in optimal thickness in all of the cooling segments, the analysis shows that, already after this short period of time, 16 times more energy is saved than the amount that went into the production of the insulating material. At the same time, modern insulation made of polyurethane not only improves the energy balance but also reduces CO2 emissions.
Three PU grades for the cold chain
Fundamentally speaking, the better the insulation effect, the less energy has to be used for the actual cooling. Various polyurethane systems are used nowadays for insulation purposes. BASF Polyurethanes has three innovative system groups in its portfolio: Elastocool®, Elastopir® and Elastopor®. Thanks to this polyurethane insulation tailored for use and efficiency – Elastocool for refrigerators and freezers, Elastopir for refrigerated warehouses and cold-storage cells, and Elastopor for freezer chests, truck trailers and transportation boxes – the energy and raw material consumption as well as the emissions can be considerably reduced. The rigid-foam insulation made of polyurethane stands out especially for its very low thermal conductivity resulting from the combination of a fine, closed-cell foam structure and heat-insulating cell gases. Owing to the low thermal conductivity and the good physical properties such as the low density, polyurethane is the insulation material most frequently found in the cold chain.
Clear-cut energy savings with thicker insulation layer
For every specific cooling step, the Eco-Efficiency Analysis of the cold chain compared polyurethane insulation made of the same material but with different thicknesses. Accordingly, the difference does not lie in the material itself, but rather, in the thickness of the insulation since the PU foam is already highly efficient. The thinner insulation used as the reference in the analysis is the thinnest insulation layer used in the cold-chain segment and still available on the market today. A closer look at an appliance such as a freezer shows that a model whose insulating material is 50 millimeters thick can be compared to a freezer that is optimally insulated with polyurethane that is 60 millimeters thick. The Eco-Efficiency Analysis shows that a modern appliance with BASF polyurethane insulation has an energy-savings factor of 20:1. Such an appliance literally becomes a piggy bank since within a mere seven days – this is the duration of this part of the examined cold chain – this freezer saves 20 times more energy than is required for the production of the polyurethane. Extrapolated over an entire year, this would rise to a factor of roughly 1040:1.
This energy balance, which is related only to the polyurethane insulation, not only affects the monthly energy costs but also has a lasting impact on the carbon dioxide emissions. Calculated on the basis of an average cold chain of such an appliance, this translates into an improvement of 15 percent. Whereas a freezer with insulation that is 50 millimeters thick emits 23 kilograms of CO2 in seven days, the model with insulation that is 60 millimeters thick, emits only 15.5 kilograms of CO2 over the same period of time. These figures already include the production and the disposal of the polyurethane rigid foam. At the same time, more than 15 percent of the requisite resources can be saved during the production of the insulating material – currently primarily fossil fuel resources whose supply is known to be finite.
Consequently, consumers who own freezers with insulation that is ten millimeters thicker make a huge contribution to energy savings. And such savings are already achieved when the frozen pizza makes its way through the cold chain and stays in the freezer for a mere seven days before it is eaten.
As far as the total cold chain of 75 days is concerned, the Eco-Efficiency Analysis of BASF Polyurethanes demonstrates that each pallet of frozen food will emit 5.3 kilograms less CO2. This is an improvement of 13 percent. And in spite of the need for more resources to produce the thicker polyurethane insulation, the amount of resources saved during the utilization phase is so great that a plus of 12 percent remains at the end of the cold chain. This result is the outcome of just the difference in the thickness of the insulation of this generation of BASF polyurethane rigid foams which are, in fact, already very efficient.