Feb 3 2011
For the last ten years, biodiesel in the form of fatty acid methyl ester has been promoted as a replacement for fossil-fuel-based diesel fuel. It was soon found that this has its problems because the required plants, such as rape, occupy cropland that can then no longer be used to grow food. A second-generation biodiesel is now supposed to be gained from plant waste.
In the journal Angewandte Chemie, Avelino Corma and his team at the Universidad Politécnica de Valencia (Spain) have introduced a highly promising new process that is energy efficient and delivers high-quality biodiesel fuel.
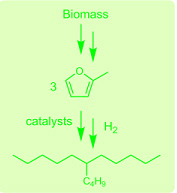
The usable materials in biomass - oat hulls, almond shells, bagasse (fibrous remains of sugar production from cane), sunflower-seed shells, corncobs, waste from olive oil production - consist mainly of cellulose-like carbohydrates. “A number of different approaches have been developed,” reports Corma, “many of them suffer from an unfavorable energy balance because they require a lot of energy themselves.”
Corma and his team have now successfully developed a simple, cost-effective process that is energy-efficient and also does not require any organic solvents. The first step is the conversion of biomass into furfural an established industrial process. In an adaptation of another current process, furfural can be converted with high selectivity into 2-methyl-furfural (2MF), a ring consisting of four carbon atoms and one oxygen atom, with a side chain consisting of a methyl group (–CH3).
“This 2MF is the starting material for our new diesel synthesis”, says Corma. First, three molecules of 2MF are linked together. This requires water and an acid catalyst. This reaction causes one third of the rings to open and each link to two other rings (hydroxy alkylation/alkylation). The aqueous phase, which also contains the catalyst, separates from the organic phase, which contains the intermediate product, on its own. It can easily be removed and the catalyst recycled. In a second reaction, the two other rings must also be opened and their oxygen atoms removed. This reaction uses a special platinum-containing catalyst (hydrodeoxygenation).
“In the end we obtain 87% of the diesel fraction in the form of branched hydrocarbon chains with nine to 16 carbon atoms,” claims Corma. “This is the best yield reported in the literature thus far for biodiesel synthesis.” Gas-phase and lower molecular weight byproducts can be used to produce heat. The resulting biodiesel is of excellent quality (cetane number 71, pour point 90 °C) and can be mixed directly with conventional diesel fuels.