PureCycle Technologies has announced it has successfully completed purified waste carpet from its Feedstock Evaluation Unit (FEU), transforming discarded carpet into clear, odorless, Ultra-Pure Recycled Polypropylene (UPRP) resin through its proprietary plastics recycling technology, developed and invented by Procter & Gamble.
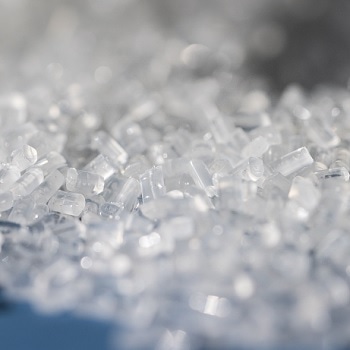
The successful scaling of the technology unlocks the value for a wide range of waste polypropylene (PP) that can be restored to its original virgin-like condition. This technology will result in a substantial increase in demand for waste PP and will help to provide alternatives to landfilling and exporting plastic waste.
105 Million Pounds of Virgin-like PP/Year
The FEU is the first of two phases for PureCycle’s plant in Hanging Rock, Ohio. The second phase, which will come online in the summer of 2021, will process 119 million pounds of waste PP each year. The plant is expected to produce over 105 million pounds of virgin-like PP per year.
This will be used in:
- Consumer goods packaging
- Home furnishings
- Other applications that currently have very limited recycled PP options
PureCycle is also working towards submitting for a letter of non-object from the FDA for their ultra-pure recycled polypropylene to be used in food grade applications.
Fulfilling Demand for High-quality Recycled PP
“There is an overwhelming demand for high-quality recycled polypropylene, and this milestone is a huge step for us—and the industry—toward addressing a growing market that is demanding recycled applications,” said Mike Otworth, CEO of PureCycle Technologies. “This achievement not only proves the technology at scale, but also builds on the momentum of the business as we move closer towards scaling operations beyond our first plant.”
The development of the technology began when P&G was looking for more ways to incorporate additional recycled content into their applications, specifically targeting PP. With limited amounts of rPP available in the market, P&G set out to develop their own process to purify waste polypropylene. This groundbreaking innovation is the heart of PureCycle and continues to be a key initiative for P&G and their goal of reducing petroleum plastic in their packaging by 50%.
Oncoming Large-scale Operation in Europe
The PureCycle process removes color, odor and impurities, producing virgin-like resin. This Ultra-Pure Recycled Polypropylene (UPRP) delivers a consistent product that meets virgin-like specifications to meet the demands of various industries. In fact, demand for recycled PP is so high, PureCycle’s first plant is fully subscribed and has begun site selection for our large-scale operation in Europe.
Contaminants-free from Recycled Resin
“Our approach to innovation not only includes products and packaging, but technologies that allow us and others to have a positive impact on our environment. This technology, which can remove virtually all contaminants and colors from used plastic, has the capacity to revolutionize the plastics recycling industry by enabling P&G and companies around the world to tap into sources of recycled plastics that deliver nearly identical performance and properties as virgin materials in a broad range of applications,” said Kathy Fish, P&G’s Chief Research, Development and Innovation Officer.
While the FEU is located at the first plant’s site, it is a perpetual asset to the company that will allow PureCycle to refine the operating conditions and process waste polypropylene from around the world to help with the sizing for future plants in other geographies. Plant 1 will process a broad range of feedstocks, ranging from carpet and food packaging to toys, automotive components and other plastic waste.
“This milestone exemplifies our team’s incredible dedication and drive to bring this world-changing technology to life. Our progress continues to break barriers as we head towards commercial scale, and I could not be prouder of the team making it happen,” said Tayt Rule, COO of PureCycle Technologies.