Scientists, including an Oregon State University College of Engineering faculty member, have made a critical step toward significantly increasing the variety of recyclable plastics.
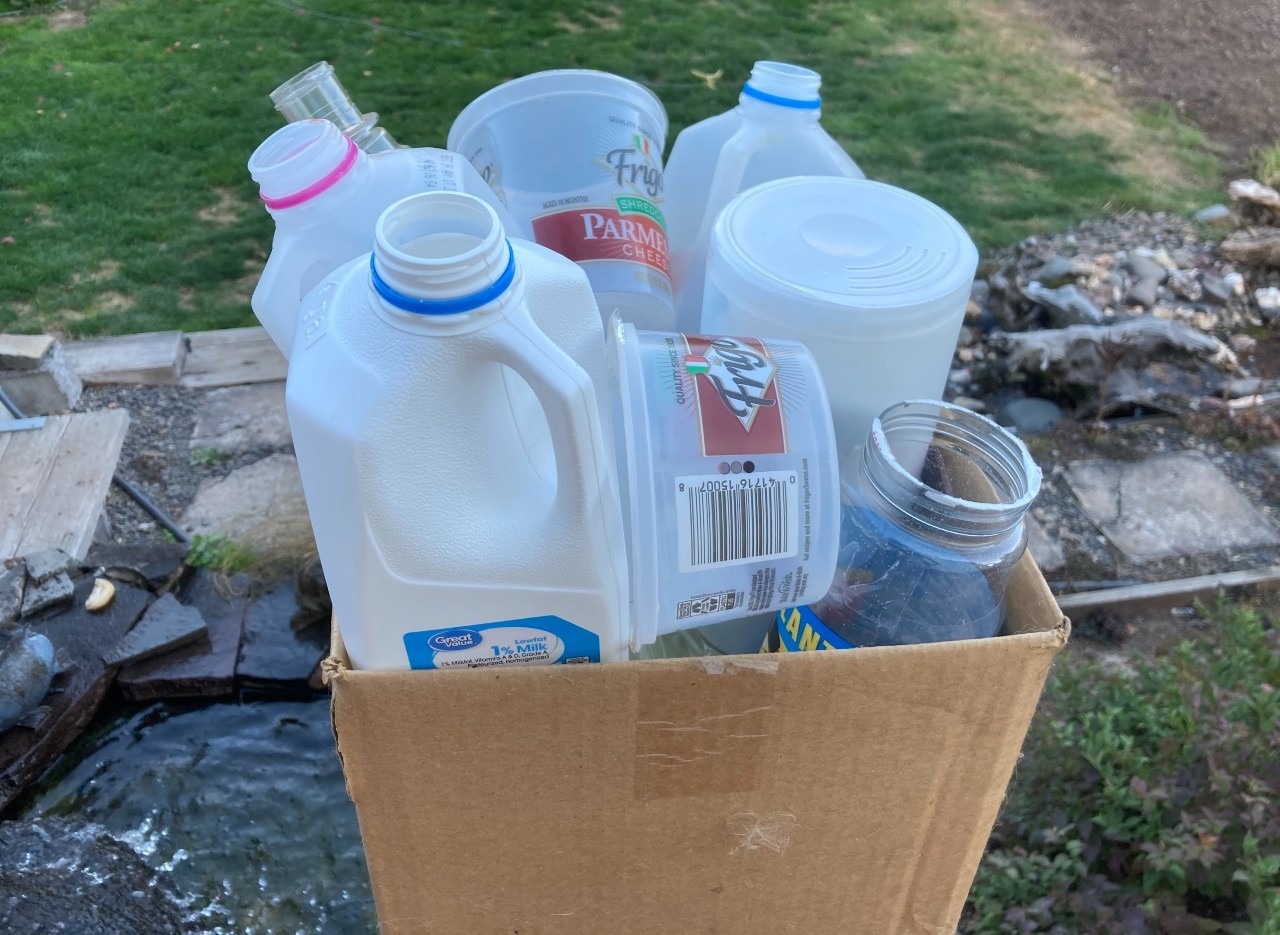
Plastic waste. Image Credit: Oregon State University
The research results are significant as plastic waste is a huge concern worldwide. In the United States, in particular, only about 5% of used plastic is recycled, according to the National Renewable Energy Laboratory of the United States Department of Energy, which led the study. The research was published in the journal Science.
According to NREL, packaging materials, containers, and other abandoned items are accumulating in landfills and polluting the environment so rapidly that scientists estimate that by 2050, the ocean will contain more plastic by weight than fish.
In a proof of concept to “valorize”—valorize means to increase the worth of something—mixed plastic waste, a partnership headed by NREL’s Gregg Beckham and including Lucas Ellis, an OSU scientist who was an NREL postdoctoral fellow during the project, integrated chemical and biological processes.
The study builds on the utilization of chemical oxidation to break down a range of plastic varieties, a technology pioneered by chemical industry titan DuPont a decade ago.
We developed a technology that used oxygen and catalysts to break down plastics into smaller, biologically friendly chemical building blocks. From there we used a biologically engineered soil microbe capable of consuming and ‘funneling’ those building blocks into either a biopolymer or a component for advanced nylon production.
Lucas Ellis, Assistant Professor, Chemical Engineering, Oregon State University
Beckham, a senior research fellow at NREL and the head of the Bio-Optimized Technologies to keep Thermoplastics out of Landfills and the Environment Consortium, BOTTLE, stated that the research offers a “potential entry point into processing plastics that cannot be recycled at all today.”
Beckham argues that the input plastics must be clean and sorted into different types for the current recycling technology to work efficiently.
Different polymers, with their own chemical building blocks, are used to create plastics. Recycling is expensive and almost impossible when polymer chemistries are combined in products like multilayer packaging or mixed-in collection bins since the polymers frequently need to be separated before they can be recycled.
Our work has resulted in a process that can convert mixed plastics to a single chemical product. In other words, it is a technology that recyclers could use without the task of sorting plastics by type.
Lucas Ellis, Assistant Professor, Chemical Engineering, Oregon State University
The authors examined the method on a mix of three widely used plastics: high-density polyethylene, which is used in milk jugs and numerous other consumer products; polyethylene terephthalate, serving as the foundation for carpets, polyester clothing, and single-use beverage bottles; polystyrene, which is used in disposable coffee cups.
Plastics were broken down into various chemicals throughout the oxidation process, including benzoic acid, terephthalic acid, and dicarboxylic acids, which in the absence of the engineered soil microorganism would call for sophisticated and expensive separations to produce pure products.
The microbe, Pseudomonas putida, was genetically modified to biologically funnel the mixture into one of two products: polyhydroxyalkanoates, a new type of biodegradable bioplastic, and beta-ketoadipate, which may be utilized to make performance-advantaged nylon.
Future work will concentrate on testing the process with different plastics, such as polypropylene and polyvinyl chloride, according to the researchers.
The chemical catalysis process we have used is just a way of accelerating a process that occurs naturally, so instead of degrading over several hundred years, you can break down these plastics in hours or minutes.
Kevin Sullivan, Study Co-Author and Postdoctoral Researcher, the National Renewable Energy Laboratory
The research was carried out as part of the BOTTLE Consortium and was funded by the US Department of Energy’s Advanced Manufacturing Office and Bioenergy Technologies Office.
The research included scientists from the Massachusetts Institute of Technology, the University of Wisconsin-Madison, and the Oak Ridge National Laboratory.
NREL is the primary national laboratory of the US Department of Energy for renewable energy and energy efficiency research and development. The Alliance for Sustainable Energy, LLC operates it for the department.