In a recent study in Nature Communications, researchers presented a novel method for producing free-standing ultrathin silicon wafers and solar cells with a thin silicon with reinforced ring (TSRR) structure. This innovative approach aimed to decrease breakage rates, enhance efficiency, and introduce flexibility to thin silicon solar cells. This research also investigated the mechanical and optoelectrical properties of the TSRR structure while showcasing its compatibility with industrial processes.
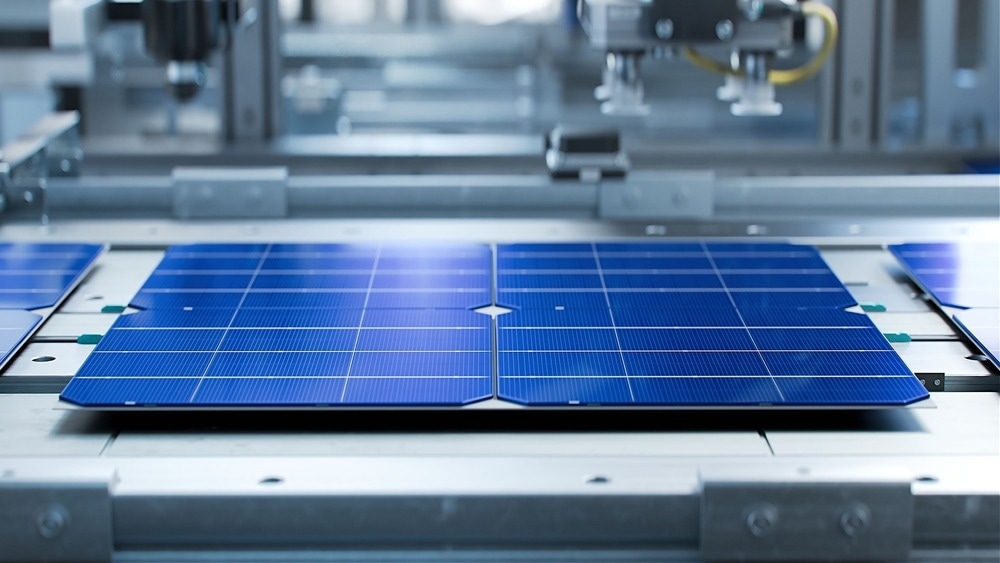
Image Credit: IM Imagery/Shutterstock.com
Background
Silicon is the most widely used material for photovoltaic applications, accounting for over 95% of the market share. However, conventional silicon solar cells are rigid and thick, which limits their potential for lightweight and flexible applications.
To overcome this limitation, practitioners have been exploring thinning silicon wafers and making them more bendable, such as epitaxy, spalling, micro-machining, and silicon-on-insulator (SOI) technologies. However, these methods are either too complex, costly, or incompatible with industrial production. Moreover, due to their brittle nature, thin silicon wafers are prone to breakage during fabrication and handling.
About the Research
In this article, the authors propose a cost-effective method for fabricating the TSRR structure, which enables free-standing ultrathin silicon wafers and high-performance solar cells with minimal breakage. The TSRR structure features a thin silicon core (less than 50 μm) surrounded by a robust ring (around 200 μm thick) at the wafer's edge.
This structure is achieved by depositing a silicon nitride (SiNx) layer on both sides of a conventional silicon wafer, selectively removing the SiNx layer from the center region on one side, and then etching the wafer to the desired thickness in an alkaline solution. The remaining SiNx layer protects the edge region from etching, forming the reinforced ring.
The paper demonstrated that the TSRR structure offers mechanical support and stress relief for the thin silicon region during fabrication, significantly reducing breakage rates compared to conventional all-thin silicon (ATS) structures. The researchers further showed that the TSRR structure can achieve high optical and electrical performance by optimizing the width of the reinforced ring and the thickness of the thin silicon region.
They fabricated free-standing thin silicon solar cells with a dopant-free and interdigitated back contact design using the TSRR structure, achieving an efficiency of 20.33% (certified value: 20.05%) on a 28-μm silicon solar cell with a breakage rate of ~0.67%. This was the highest efficiency reported for thin silicon solar cells with a thickness of less than 35 μm.
Research Findings
The authors conducted a comprehensive series of experiments and simulations to analyze the mechanical and optoelectrical characteristics of the TSRR structure and compared them with the ATS structure. Their findings were as follows:
- Mechanical properties: The TSRR structure exhibited superior resistance to external forces and deformations due to the stress-sharing mechanism of the reinforced ring. This feature prevented crack initiation and propagation from the wafer's edge, a common issue in thin silicon wafers.
- Optoelectrical properties: By adjusting the width of the reinforced ring and the thickness of the thin silicon region, the TSRR structure achieved high light absorption and carrier collection efficiency. The optimal parameters were a reinforced ring width of less than 10% of the wafer's width and a thin silicon region thickness of around 30 μm. These parameters balanced optical and electrical performance with mechanical stability.
- Compatibility: The TSRR structure proved compatible with various silicon technologies and solar cell architectures, including passivated emitter and rear cell (PERC), silicon heterojunction (SHJ), tunnel oxide passivating contact (TOPCon), and dopant-free passivating contact, as well as front and back contacts (FBC) and interdigitated back contacts (IBC) structures. The authors demonstrated the feasibility of fabricating thin silicon solar cells with the TSRR structure using a dopant-free IBC structure, achieving high open-circuit voltage and fill factor.
These results highlighted the versatility and effectiveness of the TSRR structure in enhancing both mechanical robustness and optoelectrical performance while maintaining compatibility with diverse silicon technologies and solar cell architectures.
Applications
The TSRR structure can enable the development of lightweight and flexible thin silicon solar cells with high efficiency and low cost, which can expand the potential applications of silicon photovoltaics in various fields, such as building-integrated photovoltaics, remote power generation, electric vehicles, aircraft, and wearable electronics. It can also reduce silicon solar cells' material and energy consumption, which can contribute to the environmental sustainability of the photovoltaic industry.
Conclusion
The novel TSRR method effectively fabricates free-standing ultrathin silicon wafers and solar cells with heightened performance and reduced breakage rates.
The researchers suggested that future work could optimize the TSRR structure and the fabrication process to further improve the efficiency and stability of thin silicon solar cells. They recommended investigating the environmental and economic impacts of the TSRR method compared to conventional silicon solar cell methods.
Journal Reference
Wu, T., Liu, Z., Lin, H. et al. Free-standing ultrathin silicon wafers and solar cells through edges reinforcement. Nat Commun 15, 3843 (2024). https://doi.org/10.1038/s41467-024-48290-5, https://www.nature.com/articles/s41467-024-48290-5.
Disclaimer: The views expressed here are those of the author expressed in their private capacity and do not necessarily represent the views of AZoM.com Limited T/A AZoNetwork the owner and operator of this website. This disclaimer forms part of the Terms and conditions of use of this website.