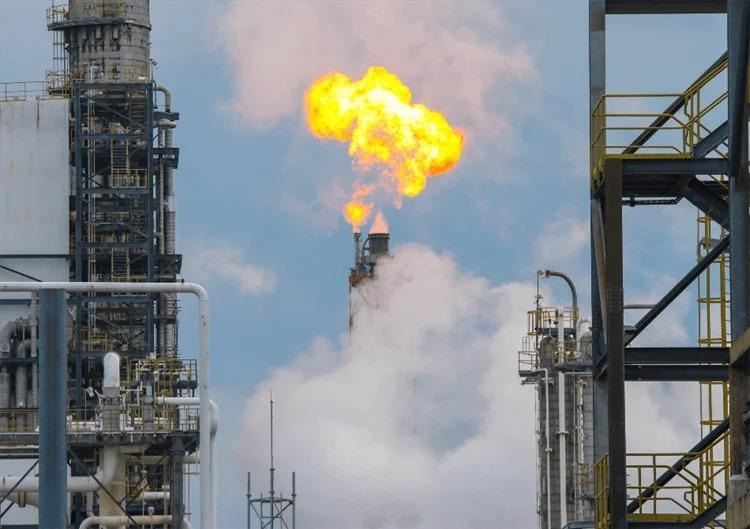
Image Credit: Thermo Fisher Scientific – Environmental and Process Monitoring Instruments
National, regional and local government bodies require processing companies to carry out monitoring of emissions from plant and flare stacks. This is aimed at reducing levels of pollution which have been entering the atmosphere at an increasing rate.
While oil refinery flares were the initial focus of such interventions, chemical and petrochemical plant flares have also been pinpointed as potential sources of hazardous airborne pollutants.
Petrochemical Plants
The EPA signed off on a number of Risk and Technology Review (RTR) rules in March 2020. Among these were the National Emission Standards for Hazardous Air Pollutants (NESHAP): Generic Maximum Achievable Control Technology Standards for Ethylene Production (EMACT).
The EPA ruled that the requirements presently in place for EMACT flares were not adequate to ensure the 98% destruction efficiency benchmark needed to meet current standards.
Both EMACT flares and refineries are subject to the same flare requirements and definitions, which means that EMACT flares must be monitored constantly.
Pre-existing ethylene crackers have up to three years after the publication of the final rule in the Federal Register to adhere to the requirements. New crackers, or crackers where construction began after October 9, 2019, need to comply by the date of publication of the final rule or on initial start-up, whichever date is later.
Organic Chemicals Manufacturer
The EPA finalized the amendments to 2003’s Miscellaneous Organic Chemical Manufacturing National Emission Standards for Hazardous Air Pollutants (NESHAP) (known as MON) in May 2020.
These amendments added operational and monitoring requirements for flares, designed to control emissions from processes that generate olefins, polyolefins, as well as flares that control ethylene oxide emissions.
They also allow any facilities falling outside of this subset to opt into these flare requirements instead of conforming to the current flare standards.
It is estimated by the EPA that these finalized amendments will lead to a reduction in hazardous air pollutant (HAP) emissions of 107 tons per year. Additionally, it will result in reductions of ethylene oxide emissions of ~0.76 tons per year. A reduction of approximately 260 tons per year in HAP emissions from flares is also anticipated.
Oil Refineries
The regulations followed the EPA’s November 2018 amendments to Refinery Sector Rule (RSR) 40 CFR Part 63 affecting flares. These regulations meant that by January 30, 2019, flares had to comply with the new §63.670 Requirements for Flare Control Devices.
The new requirements define five flare operating limits:
- Dilution net heating value (NHVdil)
- Flare tip exit velocity
- Pilot flame presence
- Visible emissions
- Combustion zone net heating value (NHVCZ)
An NHVCZ minimum operating limit of 270 BTU/scf was also specified, based on a 15-minute block period.1
NHVCZ can be calculated by measuring the net heating value of the vent gas (NHVVG). As a result, flare gas analysis is a cornerstone of any compliance strategy.
Where the NHVCZ approaches 270 BTU/cscf, other fuel gases such as natural or propane gas must be added to the process. Steam may then need to be added to the flare to avoid the production of visible emissions.
Measurement of Flare Gas Streams by Process Mass Spectrometry
There are a number of challenges to the analysis of flare gases, regardless of their origin. For example, such emissions are generally comprised of a complicated combination of inorganic and organic species.
Where the process conditions change, the composition and concentration of these species can be very different over time.
Regulations may require that only the total values of total heating value, sulfur, or total hydrocarbon values be collected.
Measuring the concentrations of individual components helps to identify the source of the emission. This can help pinpoint any issues to a particular part of the plant.
Heating values of flares can change rapidly, and as a result, analysis speed is vital; failure to meet emission standards is more likely when the analysis times are measured over time periods of minutes.
Process Mass Spectrometry allows for accurate, rapid, multicomponent analysis. The makes it an appropriate tool for measuring flare gas streams. For example, Table 1 illustrates a flare gas stream that contains hydrogen, nitrogen, and hydrocarbons up to C6.
Analysis of these 19 components can be performed in under 30 seconds. This allows one mass spectrometer to monitor multiple flares, dependant on the distances involved.
Advantages of Prima PRO Process Mass Spectrometer
The Prima PRO Process Mass Spectrometer from Thermo Fisher ScientificTM has a magnetic sector analyzer at its core (see Figure 1). When compared to other mass spectrometers, it delivers unrivaled precision and accuracy.
Table 1. Example of flare gas stream composition. Source: Thermo Fisher Scientific – Environmental and Process Monitoring Instruments
Component |
Molecular Weight |
Flare Gas Typical Composition %mol |
Hydrogen |
2 |
0-40 |
Methane |
16 |
15-95 |
Water |
18 |
0-8 |
Carbon
Monoxide |
28 |
0-1 |
Nitrogen |
28 |
0-40 |
Ethylene |
28 |
0-12 |
Ethane |
30 |
2-15 |
Oxygen |
32 |
0-5 |
Hydrogen
Sulfide |
34 |
0-10 |
Propylene |
42 |
0-20 |
Carbon
Dioxide |
44 |
0-10 |
Propane |
44 |
0-5 |
1-3, Butadiene |
54 |
0-0.2 |
Butenes |
56 |
0-15 |
i-Butane |
58 |
0-10 |
n-Butane |
58 |
0-5 |
C5 and C6 |
70+ |
0-15 |
Carbonyl
Sulfide |
60 |
0-10 ppm |
Carbon
Disulfide |
76 |
0-1 ppm |
Thermo Fisher ScientificTM has over three decades of industrial experience in the production of quadrupole and magnetic sector mass spectrometers. Magnetic sector-based analyzers provide the best performance for industrial on-line gas analysis.
Among the key advantages of magnetic sector analyzers are:
- Long intervals between calibrations
- Accuracy
- Improved precision
- Resistance to contamination
Analytical precision can range from 2 to 10 times better than a quadrupole analyzer, depending on the complexity of the mixture and the gases under analysis.
Neutral gas molecules and atoms are initially converted into positively charged ions in the Prima PRO Process Mass Spectrometer ion source. Being an enclosed type, it allows for high sensitivity, minimum background interference and maximum contamination resistance.
As a high energy (1000 eV) analyzer, the Prima PRO Process Mass Spectrometer provides extremely rugged performance in the presence of gases and vapors that may contaminate internal vacuum components.
With its proven track record, the Prima PRO Process Mass Spectrometer can monitor high percent levels of organic compounds concentrations without suffering drift or contamination.
Ions are accelerated through a flight tube, causing them to separate by their mass to charge ratios in a magnetic field of variable strength. A uniform response can be observed over a finite mass width and the peak shape produced is ‘flat-topped.’ This is due to the magnetic sector mass spectrometer producing a focused ion beam at the detector.
The height of the peak is directly proportional to the number of ions striking the detector. The peak is also directly proportional to the measured component’s concentration. As long as the measurement is taken anywhere on the peak’s flat top, then high precision analysis will be performed.
In order to precisely measure varying composition levels in flare gas, the Prima PRO Process Mass Spectrometer’s ability to measure over a wide dynamic reach is essential.
The independent specialist company EffecTech UK provides accredited testing and calibration services to the power and energy industries for gas flow, quality and total energy metering.
It accredited the Prima PRO Process Mass Spectrometer to internationally recognized ISO/IEC 17025:2005 standards. These standards stipulate the general requirements for the competence to perform calibrations and/or tests, including sampling.
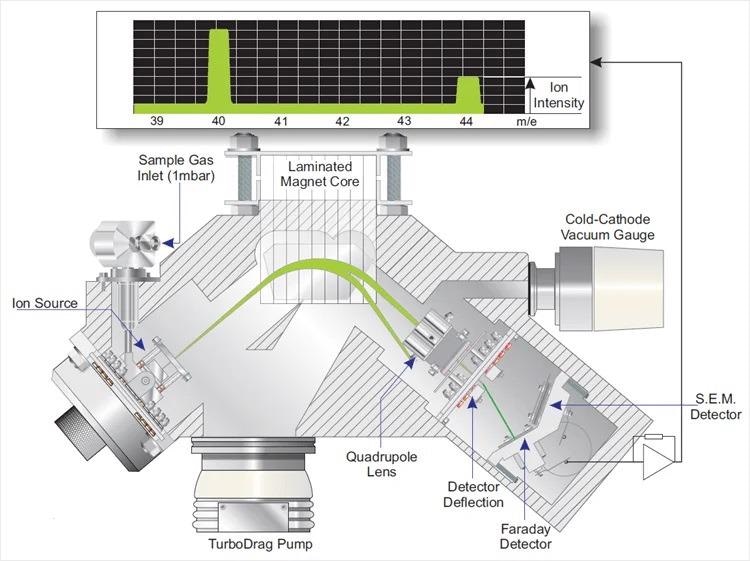
Figure 1. Prima PRO Process Mass Spectrometer magnetic sector analyzer. Image Credit: Thermo Fisher Scientific – Environmental and Process Monitoring Instruments
Rapid Multi-stream Sampling
Thermo Fisher ScientificTM developed its unique Rapid Multi-stream Sampler (RMS) to allow for rapid and reliable switching between streams. This allows the mass spectrometer is to monitor flare streams and process streams or multiple flare streams.
This also avoids the use of rotary valves, which suffer from poor reliability, and solenoid valve manifolds, which can include too much dead volume.
The RMS offers an unparalleled combination of reliability and sampling speed and allows for sample selection from 1 of 32 or 1 of 64 streams. Stream settling times are application dependent as well as being fully configurable by the user. It also includes digital sample flow recording for each stream selected by the user.
In instances where the sample flow drops, this event can be utilized to activate an alarm or warning. Alerting a user to a blocked filter in the sample conditioning system is one such example of where this can be applied.
The position of the stream selector is optically encoded, and the RMS can be heated to 120°C, allowing for reliable, software-controlled stream selection.
The internal network of the Thermo Fisher ScientificTM Prima PRO Process Mass Spectrometer communicates the temperature and position control signals.
With a three-year warranty as standard and a proven track record of performing 10 million operations between maintenance, the RMS offers a level of guaranteed dependability not provided by other multi-stream sampling devices.
Measuring Fuel Properties with Prima PRO Process Mass Spectrometer
The Prima PRO Process Mass Spectrometer allows for a number of fuel properties to be derived as a matter of routine.
By utilizing the value of 1212 BTU/scf for Hydrogen as recommended by EPA 40 CFR Parts 60 and 63, rather than the theoretical value of 274 BTU/scf, users can calculate the Lower Heating Value. This provides the user with a more reliable indication of flare performance, meeting the minimum operating limit of 270 BTU/scf.
Source: Thermo Fisher Scientific – Environmental and Process Monitoring Instruments
. |
. |
Lower Heating Value (LHV) |
Also known as Net Heating Value or
Lower Calorific Value |
Higher Heating Value (HHV) |
Also known as Gross Heating Value or
Higher Calorific Value |
Compressibility |
|
Actual Lower Heating Value |
Ideal Lower Heating Value
--------------------------------------
Compressibility |
Density |
|
Specific Gravity |
|
Lower Wobbe Index |
Lower Heating Value
--------------------------------
√(Specific Gravity) |
Higher Wobbe Index |
Higher Heating Value
----------------------------------
√(Specific Gravity) |
Air Requirement |
|
Combustion Air Requirement Index (CARI) |
Air Requirement
-----------------------------
√(Specific Gravity) |
Precise analysis of hydrogen across a wide dynamic range is essential because this has such a high combustion potential.
The Prima PRO Process Mass Spectrometer’s magnetic sector analyzer does not suffer from the ‘zero blast’, which makes the analysis of light molecules challenging on most quadrupole analyzers. As a result, it is ideally suited to hydrogen analysis.
HHV considers the latent heat of vaporization of water in the combustion products. The Prima PRO Process Mass Spectrometer supplies measurements with a precision that is typically better than 0.1% relative.
Figure 2 outlines how the Ideal LHV of the flare gas stream is calculated by Thermo Fisher ScientificTM GasWorks’ software Derived Values. This is based on the individual components’ Ideal LHVs.
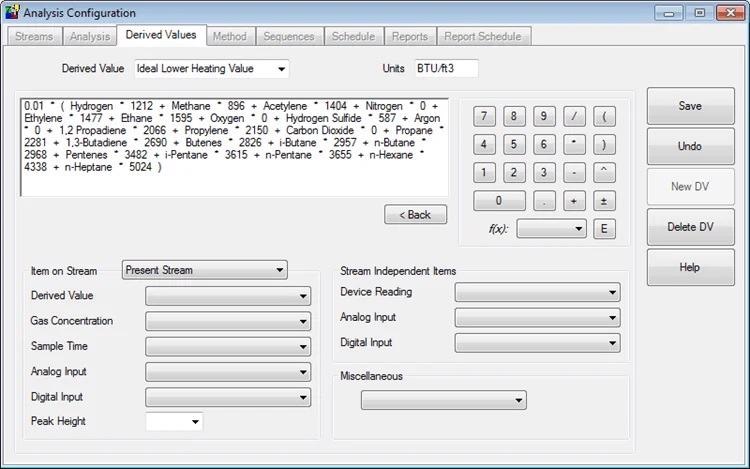
Figure 2. GasWorks Derived Value for Ideal Lower Heating Value. Image Credit: Thermo Fisher Scientific – Environmental and Process Monitoring Instruments
Including settling time, analysis times are generally 30 seconds or less. As they are measured by various techniques available, for example, 4-20 mA or 0-10 V analog outputs, Modbus, Profibus, or OPC, acquired data is communicated to the plant’s host computer.
Analytical Set-up
GasWorks software facilitates an unlimited range of analysis techniques, allowing the analysis to be optimized on a per-stream basis. The most appropriate speed versus precision settings and the most efficient peak measurements can be selected for each gas stream, depending on process control requirements.
There are a number of different analysis techniques available. For example, Figure 3 shows an example of the analytical technique for a flare gas stream, while Figure 4 demonstrates this for a process stream.
Along with additional process techniques, both approaches outlined here are being utilized on a single Prima PRO Process Mass Spectrometer to measure a combination of flare gas and process streams.
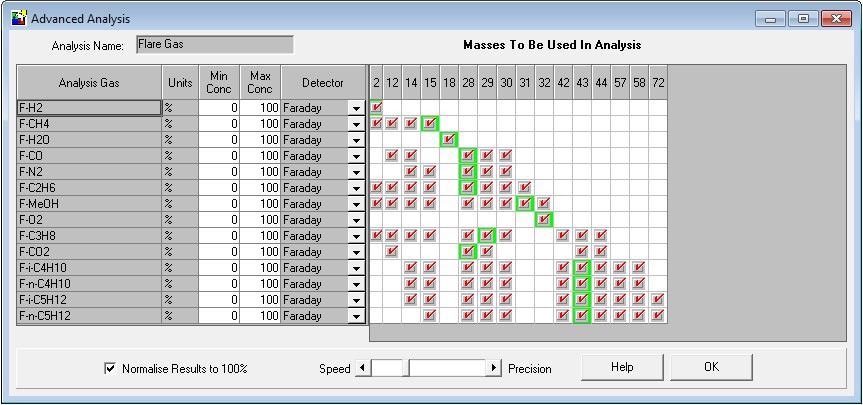
Figure 3. Example of flare stream method. Image Credit: Thermo Fisher Scientific – Environmental and Process Monitoring Instruments
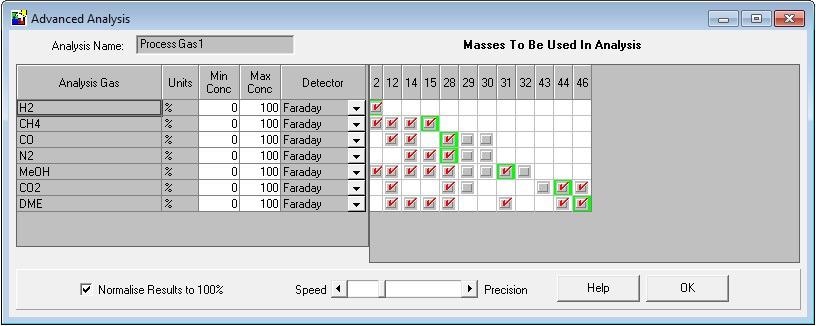
Figure 4. Example of process stream method. Image Credit: Thermo Fisher Scientific – Environmental and Process Monitoring Instruments
Both techniques visibly show the level of spectral overlap in the MS fragmentation patterns. It is important to measure these fragmentation patterns separately from the actual components of interest. The utilization of substitute compounds may simplify the calibration process, but this will inevitably result in reduced levels of accuracy.
Flare Gas Test Data
During a factory assessment, the Prima PRO Process Mass Spectrometer was tested on a gravimetric cylinder containing 21 components. These included inorganics and hydrocarbons, from C1 to C6, with the aim of checking its operation on a refinery flare gas application.
Table 2. Factory test on a gravimetric cylinder containing 21 inorganic and hydrocarbon compounds, analyzed over 18 hours. Source: Thermo Fisher Scientific – Environmental and Process Monitoring Instruments
Component |
Concentration
%mol |
Prima PRO Specification
for Standard Deviation
%mol (8 hours) |
FAT test Ave
%mol (8 hours) |
FAT Test
Actual Standard Deviation
%mol (8 hours) |
Hydrogen |
10 |
≤0.02 |
9.8835 |
0.0077 |
Methane |
64.53 |
≤0.05 |
64.6662 |
0.0125 |
Carbon
Monoxide |
5 |
≤0.05 |
5.0829 |
0.0264 |
Nitrogen |
10 |
≤0.05 |
9.8557 |
0.0469 |
Ethylene |
2 |
≤0.02 |
1.9867 |
0.0010 |
Ethane |
2 |
≤0.02 |
2.0367 |
0.0012 |
Oxygen |
1 |
≤0.001 |
0.9941 |
0.0006 |
Hydrogen
Sulfide |
0.05 |
≤0.0005 |
0.0484 |
0.0003 |
Propylene |
1 |
≤0.001 |
0.9961 |
0.0011 |
Carbon
Dioxide |
1 |
≤0.001 |
0.9597 |
0.0007 |
Propane |
1 |
≤0.001 |
1.0910 |
0.0007 |
1,3 Butadiene |
0.1 |
≤0.005 |
0.0992 |
0.0003 |
Butenes |
0.5 |
≤0.005 |
0.5023 |
0.0005 |
i-Butane |
0.5 |
≤0.005 |
0.4892 |
0.0011 |
n-Butane |
0.5 |
≤0.005 |
0.5059 |
0.0026 |
Carbonyl
Sulfide |
100 ppm |
≤1 ppm |
100.5319 |
0.4470 |
Pentenes |
0.1 |
≤0.005 |
0.0992 |
0.0004 |
i-Pentane |
0.3 |
≤0.005 |
0.3083 |
0.0012 |
n-Pentane |
0.3 |
≤0.005 |
0.2792 |
0.0042 |
Carbon
Disulfide |
100 ppm |
≤1 ppm |
100.4589 |
0.2733 |
n-Hexane |
0.1 |
≤0.005 |
0.0957 |
0.0010 |
NHV (BTU/scf) |
|
≤0.1% relative |
899.5394 |
0.07% |
Applications of Gas Analysis Mass Spectrometer in Fermentation
Table 2 shows the Thermo Fisher ScientificTM Prima PRO Process Mass Spectrometer’s quoted performance (standard deviation over 8 hours), the composition of the cylinder, and the results gathered from the test. Over a period of 8 hours, the measured standard deviations for all 21 components were found to be less than the specified standard deviations.
The Prima PRO Process Mass Spectrometer also calculated the Net Heating Value over the 8 hours of the test. As was found with the component concentrations, the measured NHV standard deviations were considerably less than the specified 8-hour standard deviations.
Figures 5a to 5d display the trend data for sulfur components, minor components, major components and NHV over the 8 hours of the test.
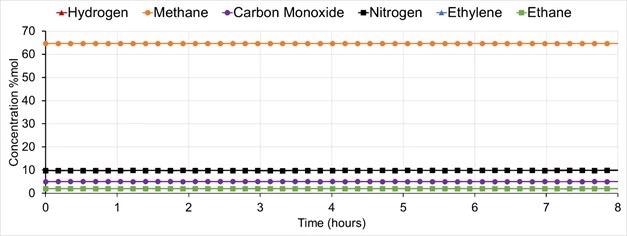
Figure 5a. Major component concentrations obtained during factory test on a gravimetric cylinder containing 21 inorganic and hydrocarbon compounds, analyzed over 8 hours. Image Credit: Thermo Fisher Scientific – Environmental and Process Monitoring Instruments
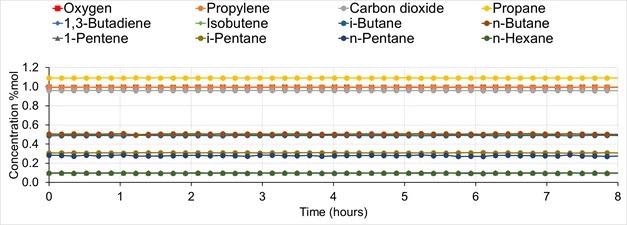
Figure 5b. Major component concentrations obtained during factory test on a gravimetric cylinder containing 21 inorganic & hydrocarbon compounds, analyzed over 8 hours. Image Credit: Thermo Fisher Scientific – Environmental and Process Monitoring Instruments
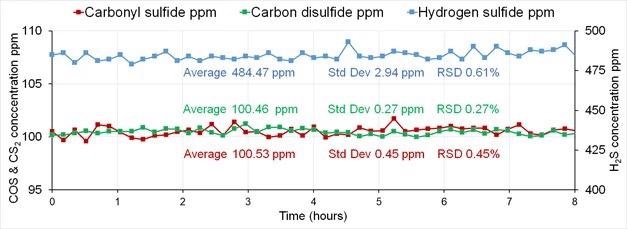
Figure 5c. Sulfur component concentrations obtained during factory test on a gravimetric cylinder containing 21 inorganic & hydrocarbon compounds, analyzed over 8 hours. Image Credit: Thermo Fisher Scientific – Environmental and Process Monitoring Instruments
9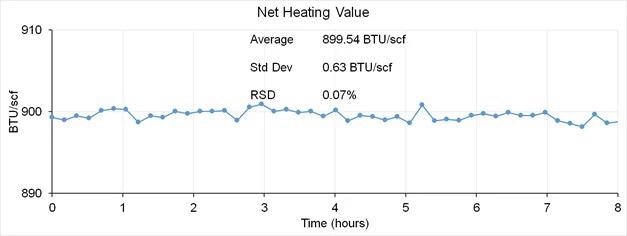
Figure 5d. NHV obtained during factory test on a gravimetric cylinder containing 21 inorganic & hydrocarbon compounds, analyzed over 8 hours. Image Credit: Thermo Fisher Scientific – Environmental and Process Monitoring Instruments
Analysis of Total Sulfur
Refinery regulators are usually interested in the values for hydrogen sulfide (H2S) and Total Reduced Sulfur (TRS). TRS is sometimes defined as H2S together with carbonyl sulfide (COS) and carbon disulfide (CS2).
TRS may also be defined as a mix of compounds containing a sulfur component in the reduced form. These are generally methanethiol (methyl mercaptan, CH3SH), dimethyl sulfide (DMS, (CH3)2S), H2S and dimethyl disulfide (DMDS, CH3S2CH3).
Mass spectrometers are capable of quantifying a number of sulfur compounds down to ppm levels. Table 3 shows typical performance figures for the Prima PRO Process Mass Spectrometer. The analysis time is below 30 seconds, and this includes stream switching time and standard deviations measured over 8 hours.
Table 3. Typical Prima PRO Process Mass Spectrometer performance specification for sulfur compounds. Source: Thermo Fisher Scientific – Environmental and Process Monitoring Instruments
Component |
Typical Composition
%mol |
Precision of analysis by
Prima PRO Process MS
(single standard deviation) ≤ |
Hydrogen Sulfide |
3 ppm |
0.5 ppm |
Methyl Mercaptan |
10 ppm |
0.5 ppm |
Ethyl Mercaptan |
10 ppm |
0.5 ppm |
n-Propyl Mercaptan |
10 ppm |
0.5 ppm |
n-Butyl Mercaptan |
10 ppm |
0.5 ppm |
To demonstrate the Prima PRO Process Mass Spectrometer’s excellent linearity when analyzing sulfur species, a single unit was calibrated for carbonyl sulfide, hydrogen sulfide and carbon disulfide at a single concentration using three cylinders.
It was then utilized to analyze a series of cylinders containing the three sulfur species.
- COS was calibrated at 0.2006%. Then MS analyzed COS concentrations from 0% to 0.2006%
- CS2 was calibrated at 0.198%, then MS analyzed COS concentrations from 0% to 0.198%
- H2S was calibrated at 0.0506%; then MS analyzed H2S concentrations from 0% to 89.88%
Table 4 shows the test gases utilized to show system linearity. The calibration gases are in red. Figure 6 displays the linearity achieved for the three sulfur species.
Table 4. Sulfur test gases used to demonstrate Prima PRO Process Mass Spectrometer linearity. Source: Thermo Fisher Scientific – Environmental and Process Monitoring Instruments
H2S Actual
Concentration %mol |
H2S Measured
Concentration %mol |
COS Actual Concentration %mol |
COS Measured Concentration %mol |
CS2 Actual Concentration %mol |
CS2 Measured Concentration %mol |
0 |
0.0001 |
0 |
0 |
0 |
0.0002 |
0.003 |
0.0028 |
0.003 |
0.0029 |
0.003 |
0.0039 |
0.0506 |
0.0503 |
0.0502 |
0.0513 |
0.0498 |
0.0576 |
0.2505 |
0.261 |
0.2006 |
0.2015 |
0.198 |
0.2006 |
0.4997 |
0.526 |
|
|
|
|
2 |
2.08 |
|
|
|
|
50.03 |
51.1 |
|
|
|
|
89.88 |
89.88 |
|
|
|
|
The data shows that not only can the Prima PRO Process Mass Spectrometer measure up to 100% concentrations, but it can also safely be calibrated for hydrogen sulfide at trace levels, for example, 0.05% in this instance.
A figure for Total Sulfur can also be provided by the GasWorks software, utilizing its Derived Value capability to sum the individual component concentrations. The total sulfur value only represents the sum of the sulfur compounds that the MS has analyzed. Any unknown or unidentified compounds will not be stated.
For an accurate Total Sulfur reading, Thermo Fisher Scientific recommends the Thermo Fisher Scientific SOLA iQ Flare System, providing accurate and constant determination of total sulfur in flare gas streams.2
The SOLA iQ Flare uses pulsed ultraviolet fluorescence (PUVF) spectrometry to calculate total sulfur. All organically bound sulfur is converted to sulfur dioxide (SO2) by process of sample combustion.
The SO2 is irradiated with ultraviolet light at a specific wavelength, forming an excited form of SO2. The emission of light or fluorescence relaxes the excited SO2 to its ground state. The intensity of the emitted light and the flare stack’s total sulfur concentration is directly proportional to the SO2 concentration.
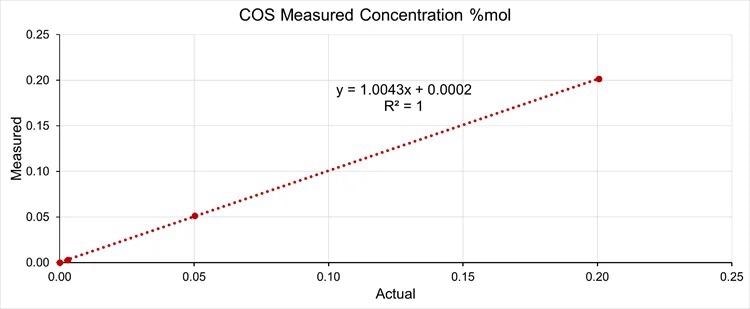
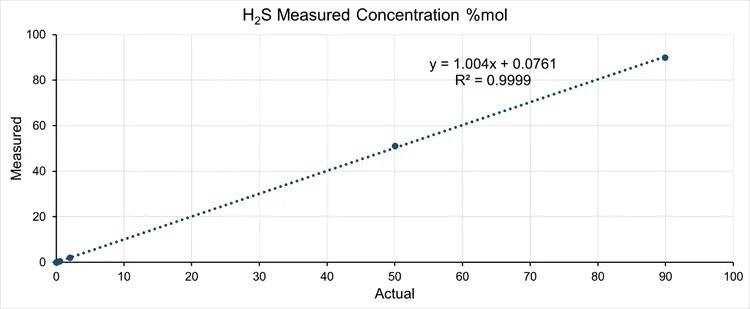
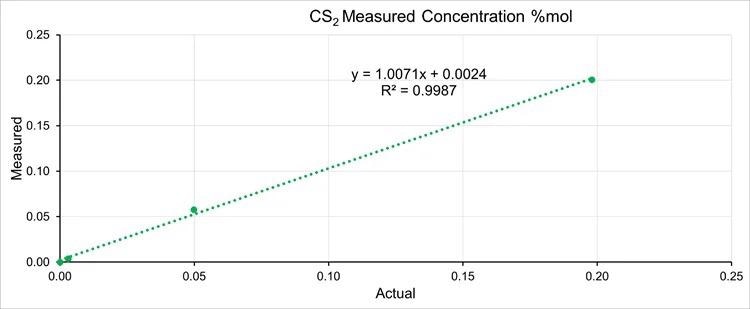
Figure 6. Prima PRO Process Mass Spectrometer linearity for hydrogen sulfide, carbonyl sulfide and carbon disulfide. Image Credit: Thermo Fisher Scientific – Environmental and Process Monitoring Instruments
Summary
The Prima PRO Process Mass Spectrometer gives timely and accurate online analysis of process gas composition and flare gas when monitoring refinery flare gases.
It has a proven track record in monitoring ethylene furnaces and ethylene oxide processes. This means it is ideal for monitoring flare gas streams from these same processes as concerns over hazardous emissions grow and grow.3,4
When it is combined with the flexibility of GasWorks software, mass spectrometry’s power and flexibility allow a single Prima PRO Process Mass Spectrometer to monitor multiple process streams, as well as flare gas streams.
By facilitating the comparison of detailed composition data from the flare gas stream with that of the multiple process streams, this approach also allows for the performance of root cause fault analysis.
The Prima PRO Process Mass Spectrometer provides accurate fuel gas properties, including HHV, LHV, density, stoichiometric air requirement, specific gravity, CARI and Wobbe Index to in order to facilitate compositional analysis.
This helps ensure that unburned pollutants are burnt to complete combustion rather than being emitted from the flare waste gases.
References
- EPA 40 CFR § 63.670 – Requirements for Flare Control Devices, US Government Publishing Offices
- Continuous flare stack emission monitoring: Thermo Fisher Scientific SOLA iQ Flare Analyzer, Thermo Fisher Scientific Application Note, 2020
- Advancing Process Control and Efficiency During Ethylene Production Using the Thermo Fisher Scientific Prima PRO Process Mass Spectrometer, Thermo Fisher Scientific Application Note, 2014
- Thermo Fisher Scientific™ Prima PRO Process Mass Spectrometer: Improving ethylene oxide process control, Thermo Fisher Scientific Application Note, 2017
Acknowledgments
Produced from materials originally authored by Daniel Merriman from Thermo Fisher Scientific.
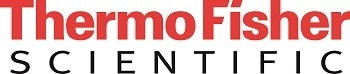
This information has been sourced, reviewed and adapted from materials provided by Thermo Fisher Scientific – Environmental and Process Monitoring Instruments.
For more information on this source, please visit Thermo Fisher Scientific – Environmental and Process Monitoring Instruments.