Commercial uses of lithium metal batteries (LMBs) that are based on organic electrolyte systems have been negatively affected by concerns of safety and the already known challenges of Li metal anodes. Several researchers have tried to resolve these issues using solid-state electrolytes (SSEs), porous scaffolds, and artificial SEI layers.
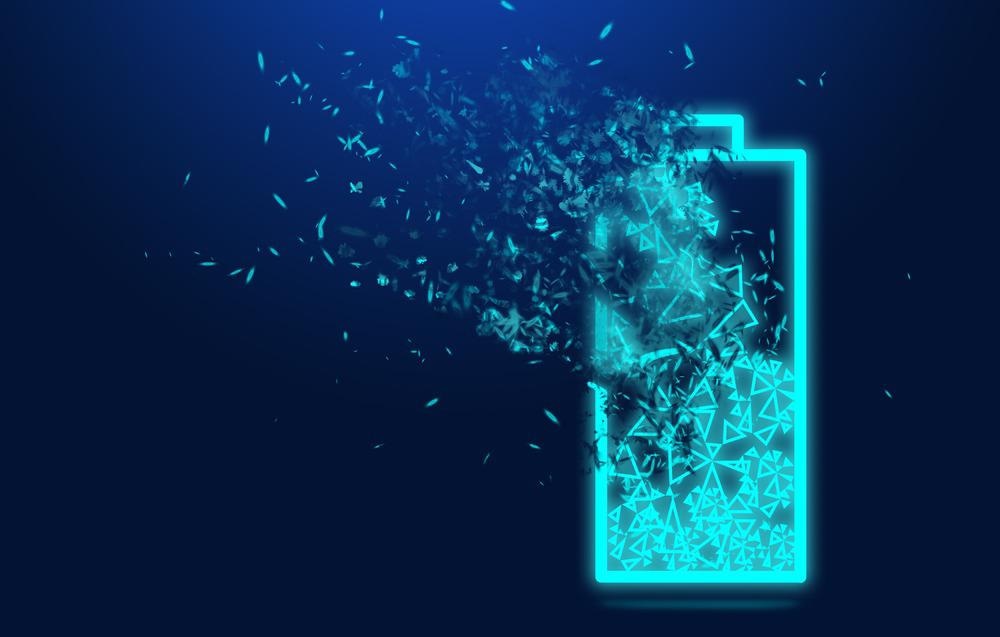
Image Credit: New Africa/Shutterstock.com
As a result, solid-state LMBs have become a potential component, as they provide a considerable safety upgrade by eliminating flammable organic solvents. Solid polymer electrolytes (SPEs) are also a promising candidate, owing to their non-toxicity, low-manufacturing cost, and comparatively soft nature that allows the development of a seamless interface with the electrodes.
Polymerization-induced phase separation (PIPS) controls the connectivity of phase-separated structures and domain size, enabling the co-continuous nanostructures’ formation. Researchers of a study published in Nature envisioned that outstanding mechanical and ionic properties could be realized, provided ionic conducting materials form a 3D interconnected phase inside a mechanically strong elastomer matrix via PIPS.
Plastic-crystal-embedded elastomer electrolytes (PCEEs) are co-continuous structures, developed through PIPS between polymers and plastic crystals in cells. Due to its superior mechanical properties, high-ionic conductivity, and mechanical elasticity, the PCEE formed within the cells successfully accommodates the considerable volume changes of Li at the rapid charge-discharge cycling.
For achieving high-efficiency and reliable solid-state LMBs, this elastomeric electrolyte system proves to be a promising strategy.
Results
To design elastomeric electrolytes, a built-in PCEE was made. A representative plastic crystal, SN, was chosen as an ionic conductive material due to its high ionic conductivity with Li salts. Three-dimensional tomography and scanning electron microscopy (SEM) images revealed that PCEE had an interconnected network structure, where worm-shaped polymer ducts were three-dimensionally connected (Figure 1).
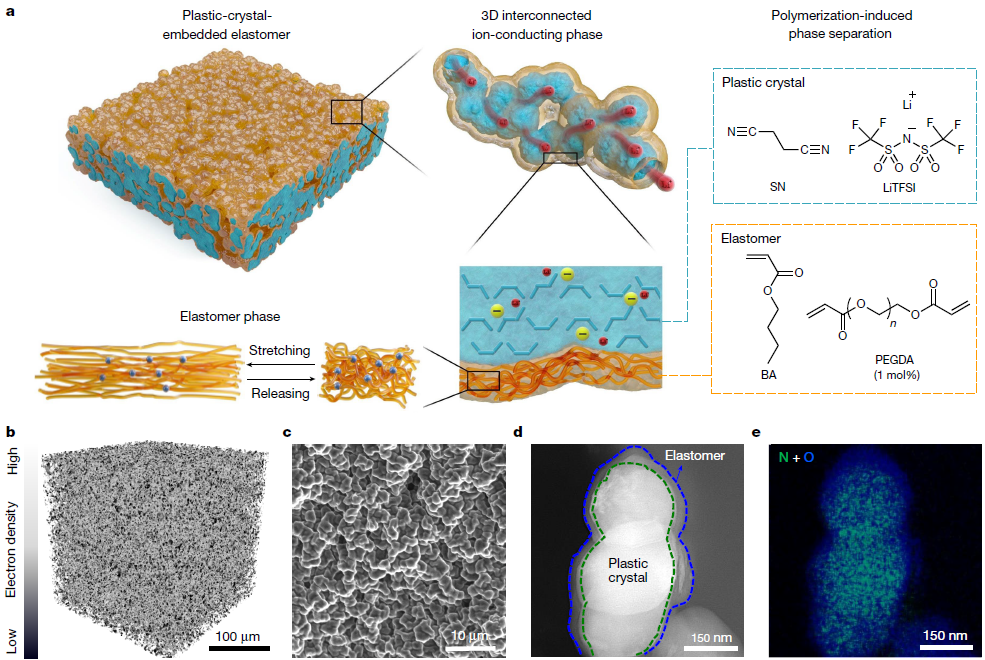
Figure 1. Design of plastic-crystal-embedded elastomer electrolyte. (a) Schematic illustration of the design and structure for PCEE. The structure of PCEE shows that the 3D interconnected plastic crystal phase (cyan) is surrounded by the elastomer phase (orange). The plastic crystal phase supports a fast ion-conducting pathway, whereas the elastomer phase provides superior mechanical extensibility. (b) A 3D tomography image of PCEE constructed by an X-ray microscope. c, d, SEM (c) and cross-sectional TEM (d) images of PCEE film. (e) Electron energy-loss spectroscopy elemental mapping of the TEM image in d. Image Credit: Lee, et al., 2022
Figure 2 depicts the properties of the built-in PCEE.
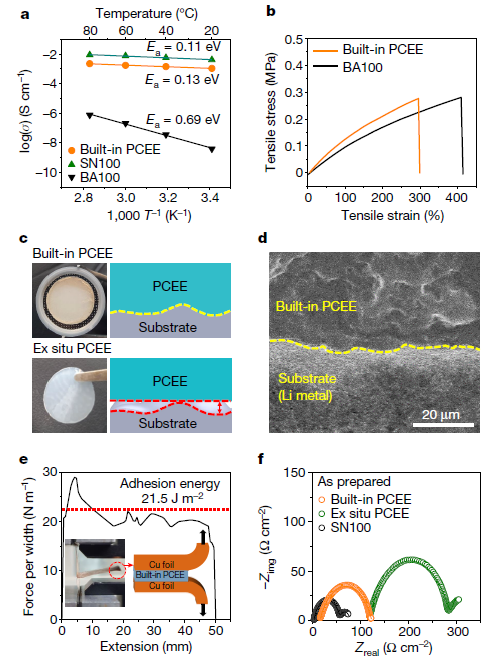
Figure 2. Properties of the built-in PCEE. (a) Arrhenius plots of the built-in PCEE and its components (BA100 and SN100) based on measurements of ionic conductivity (σ) versus temperature (T). (b) Stress–strain curves of the built-in PCEE and BA100 at an extension rate of 100 mm min−1. The tensile property of SN100 could not be measured owing to its brittleness. (c) Photo images and schemes showing the ex situ and the built-in PCEEs. (d) Cross-sectional SEM image of the built-in PCEE on Li metal anode. (e) Interfacial adhesion test between the built-in PCEE and the Cu foil. The red dotted line indicates the average force per width. (f) Nyquist plots of as-prepared symmetric Li cells configured with various electrolytes. The solid lines correspond to the equivalent circuit fits. Image Credit: Lee, et al., 2022
It was revealed that the distinct structure of PCEE is totally different from that of a usual blend. The ionic conductivity and tensile toughness of the blend are considerably lower by factors of 32 and 47, respectively, when compared with those of PCEE.
PCEE showed high ionic conductivity. This result showed that the ion-conductive pathways of the high-connectivity continuous SN domains were efficiently developed within PCEE’s elastomer matrix. Also, the results of X-ray diffraction showed the successful maintenance of the crystallinity of the SN phase inside the elastomeric phase, contributing to the PCEE’s high ionic conductivity.
These findings demonstrate that the in situ-polymerized PCEE can successfully decrease the interfacial resistance at the solid–solid interfaces, allowing super-reliable Li plating and stripping cycles. When the morphologies of the Li metal anodes with varying electrolytes were compared, Li metal exhibited a porous structure that contained mossy and dead Li within a few cycles that explains the sudden failure of Li cell.
In comparison, the Li anodes that had both the ex-situ and the built-in PCEEs exhibited a uniform and dead Li structure with no dendritic Li even after 100 cycles (200 hours) (Figure 3).
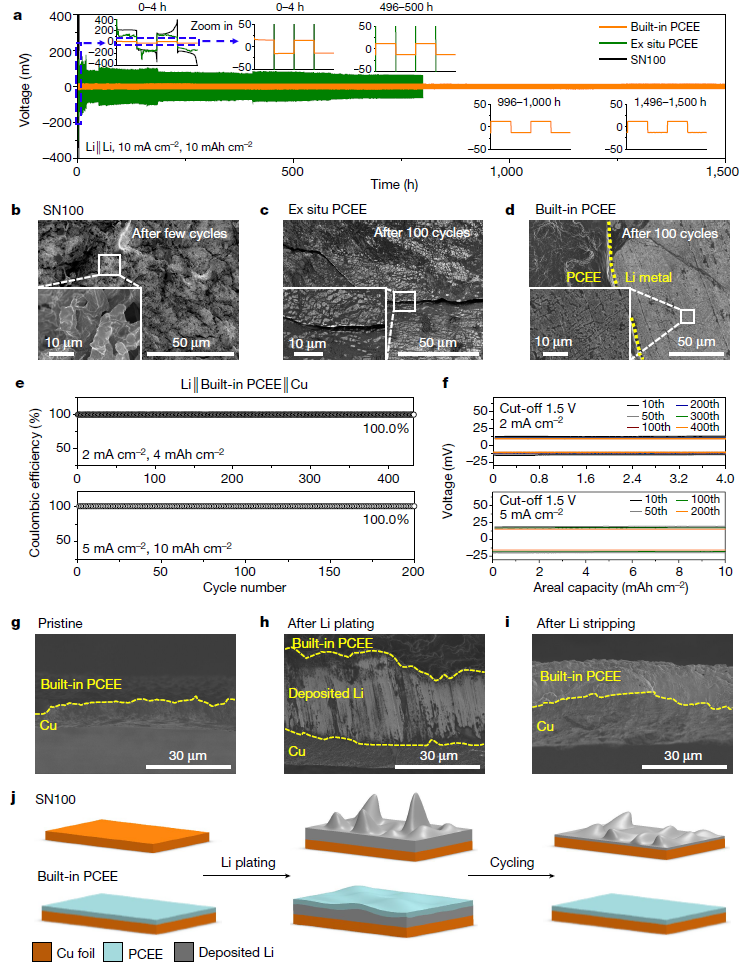
Figure 3. Built-in PCEE in symmetric Li and asymmetric Li||Cu cells. (a) The cycling performance of the symmetric Li cells with various electrolytes. Insets: enlarged voltage profiles for different times. (b–d) Top-view SEM images of the Li metal anodes with SN100 after cell failure (b), ex situ PCEE (c) and built-in PCEE (d) after 100 cycles at a current density of 10 mA cm−2 with a capacity of 10 mAh cm−2. Insets: magnified top-view SEM images. (e) Coulombic efficiencies for the asymmetric Li||Cu cells with the built-in PCEE at current densities of 2 mA cm−2 and 5 mA cm−2 with capacities of 4 mA cm−2 and 10 mAh cm−2, respectively. (f) Corresponding enlarged voltage profiles. (g–i) Cross-sectional SEM images of pristine (g), Li-plated (h) and Li-stripped (i) Cu electrodes assembled with the built-in PCEE. (j) Schematic illustration of Li plating and stripping with different electrolytes. Image Credit: Lee, et al., 2022
In addition to that, the built-in PCEE’s resilience enabled the system to revert to its original state without any deformation—after the stripping process—thus forming the super-reliable cell cycling process with PCEE stems from its superior interfacial and mechanical properties (Figure 4).
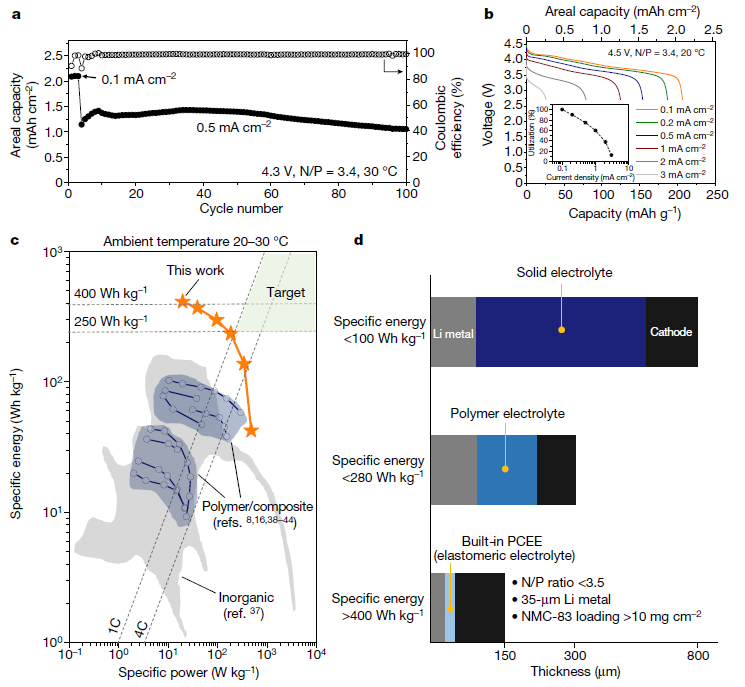
Figure 4. Towards a high-energy all-solid-state LMB with elastomeric electrolyte. (a) Thc cycling performance of the full cell as a function of cycle number in the voltage range of 2.7–4.3 V. The cell was initially cycled at a current density of 0.1 mA cm−2 for 3 cycles before cycling at 0.5 mA cm−2. (b) Rate capability of the full cell in the voltage range of 2.7–4.5 V at equal current densities. Inset: the capacity utilization at different areal current densities. (c) Ragone plot for the full cells at ambient temperature (20–30 °C). Specific energy and power in the respective references are depicted within the light-shaded regions (blue, polymer/composite electrolyte; grey, inorganic electrolyte). Specific energy and power are normalized by the mass of the cells (anode, solid electrolyte and cathode), excluding the weight of the cell casing and current collectors. (d) Schematic illustration of all-solid-state LMB that comprises a thin Li metal anode, thin built-in PCEE and high-loading NMC-83. All full cells were configured with 35-μm-thick Li anode, 25-μm-thick built-in PCEE and high-loading NMC-83 (>10 mg cm−2). Image Credit: Lee, et al., 2022
Methodology
For the generation of PCEE, electrolyte preparation and cell assembly were implemented. Characterization was carried out using Fourier transform infrared spectroscopy spectra and thermogravimetric analysis testing. The morphologies of the built-in PCEE were visualized by SEM and TEM.
The 3D tomography image was constructed using an X-ray microscope. A universal testing machine was used to analyze the mechanical tensile stress and interfacial adhesion strength. X-ray photoelectron spectroscopy was employed to analyze the compositions of the SEI developed on the Li metal anodes.
The electrochemical performances of all cells were tested. The ionic conductivity of the electrolytes was measured using EIS.
Conclusion
The applications of the built-in PCEE with various cathodes were investigated by the researchers of this study. They reported a class of SPEs depending on an in-situ development of an elastomer electrolyte that contains a 3D interconnected plastic crystal phase.
It efficiently combines the benefits from both plastic crystal and elastomer, with superior mechanical properties, high ionic conductivity, electrochemical stability, high Li-ion transference number, and low interfacial resistance.
The researchers believe that this elastomeric electrolyte system can be broadly used in the operation of several different post-metal batteries, including metal–sulfur, and metal–air batteries, due to its high ionic conductivity and outstanding mechanical properties.
Journal Reference:
Lee, M. J., Han, J., Lee, K., Lee, Y. J., Kim, B. G., Jung, K.-N., Kim, B. J., and Lee, S. W. (2022) Elastomeric electrolytes for high-energy solid-state lithium batteries. Nature, 601, pp. 217–222. Available Online: https://www.nature.com/articles/s41586-021-04209-4.
References and Further Reading
- Armand, M & Tarascon, J-M Building better batteries. Nature, 451, pp. 652–657. doi.org/10.1038/451652a.
- Choi, J W & Aurbach, D (2016) Promise and reality of post-lithium-ion batteries with high energy densities. Nature Reviews Materials, 1, p. 16013. doi.org/10.1038/natrevmats.2016.13.
- Bai, P., et al. (2016) Transition of lithium growth mechanisms in liquid electrolytes. Energy & Environmental Science, 9, pp. 3221–3229. doi.org/10.1039/C6EE01674J.
- Lin, D. C., et al. (2017) Reviving the lithium metal anode for high-energy batteries. Nature Nanotechnology, 12, pp. 194–206. doi.org/10.1038/nnano.2017.16.
- Wan, J. Y., et al. (2019) Ultrathin, flexible, solid polymer composite electrolyte enabled with aligned nanoporous host for lithium batteries. Nature Nanotechnology, 14, pp. 705–711. doi.org/10.1038/s41565-019-0465-3.
- Lee, Y.-G., et al. (2020) High-energy long-cycling all-solid-state lithium metal batteries enabled by silver-carbon composite anodes. Nature Energy, 5, 299–308. doi.org/10.1038/s41560-020-0575-z.
- Liu, W., et al. (2017) Enhancing ionic conductivity in composite polymer electrolytes with well-aligned ceramic nanowires. Nature Energy, 2, p. 17035. doi.org/10.1038/nenergy.2017.35.
- Zhao, Q., et al. (2019) Solid-state polymer electrolytes with in-built fast interfacial transport for secondary lithium batteries. Nature Energy, 4, pp. 365–373. doi.org/10.1038/s41560-019-0349-7
- Zhang, X. Y., et al. (2020) Long cycling life solid-state Li metal batteries with stress self-adapted Li/garnet interface. Nano Letters, 20, pp. 2871–2878. doi.org/10.1021/acs.nanolett.0c00693.
- Zhu, Y., et al. (2019) High electrochemical stability of a 3D cross-linked network PEO@nano-SiO2 composite polymer electrolyte for lithium metal batteries. Journal of Materials Chemistry A, 7, pp. 6832–6839. doi.org/10.1039/C9TA00560A.
- Lee, W., et al. (2019) Ceramic-salt composite electrolytes from cold sintering. Advanced Functional Materials, 29, p. 1807872. doi.org/10.1002/adfm.201807872.
- Yang, X., et al. (2020) Determining the limiting factor of the electrochemical stability window for PEO-based solid polymer electrolytes: main chain or terminal –OH group? Energy & Environmental Science, 13, pp. 1318–1325. doi.org/10.1039/D0EE00342E.
- Chen, R.-J., et al. Addressing the interface issues in all-solid-state bulk-type lithium ion battery via an all-composite approach. ACS Applied Materials & Interfaces, 9, pp. 9654–9661. doi.org/10.1021/acsami.6b16304.
- Bouchet, R., et al. (2013) Single-ion BAB triblock copolymers as highly efficient electrolytes for lithium-metal batteries. Nature Materials, 12, pp. 452–457. doi.org/10.1038/nmat3602.
- Zhou, D., et al. (2015) In situ synthesis of a hierarchical all-solid-state electrolyte based on nitrile materials for high-performance lithium-ion batteries. Advanced Energy Materials, 5, p.1500353. doi.org/10.1002/aenm.201500353.
- Jiang, T., et al. (2020) Solvent-free synthesis of thin, flexible, nonflammable garnet-based composite solid electrolyte for all-solid-state lithium batteries. Advanced Energy Materials, 10, p. 1903376. doi.org/10.1002/aenm.201903376.
- Markvicka, E. J., et al. (2018) An autonomously electrically self-healing liquid metal–elastomer composite for robust soft-matter robotics and electronics. Nature Materials, 17, pp. 618–624. doi.org/10.1038/s41563-018-0084-7.
- Pan, C., et al. (2019) A liquid-metal–elastomer nanocomposite for stretchable dielectric materials. Advanced Materials, 31, p. 1900663. doi.org/10.1002/adma.201900663.
- Kim, H. J., et al. (2020) Ionoelastomer junctions between polymer networks of fixed anions and cations. Science, 367, pp. 773–776. doi.org/10.1126/science.aay8467.
- Park, M., et al. (2012) Highly stretchable electric circuits from a composite material of silver nanoparticles and elastomeric fibers. Nature Nanotechnology, 7, pp. 803–809. doi.org/10.1038/nnano.2012.206.
- Chen, L., et al. PEO/garnet composite electrolytes for solid-state lithium batteries: From “ceramic-in-polymer” to “polymer-in-ceramic”. Nano Energy, 46, pp. 176–184. doi.org/10.1016/j.nanoen.2017.12.037.
- Wang, F., et al. Progress report on phase separation in polymer solutions. Advanced Materials, 31, p. 1806733. doi.org/10.1002/adma.201806733.
- Seo, M. & Hillmyer, M A (2012) Reticulated nanoporous polymers by controlled polymerization-induced microphase separation. Science, 336, pp. 1422–1425. doi.org/10.1126/science.1221383.
- Schulze, M. W., et al. (2014) High-modulus, high-conductivty nanostructured polymer electrolyte membrane via polymerization-induced phase separation. Nano Letters, 14, pp. 122–126. doi.org/10.1021/nl4034818.
- Alarco, P. J., et al. (2004) The plastic-crystalline phase of succinonitrile as a universal matrix for solid-state ionic conductors. Nature Materials, 3, pp. 476–481. doi.org/10.1038/nmat1158.
- Choi, K. H., et al. (2014) Thin, deformable, and safety-reinforced plastic crystal polymer electrolytes for high-performance flexible lithium-ion batteries. Advanced Functional Materials, 24, pp. 44–52. doi.org/10.1002/adfm.201301345.
- White, T. J., et al. (2007) Polymerization kinetics and monomer functionality effects in thiol-ene polymer dispersed liquid crystals. Macromolecules, 40, pp. 1112–1120. doi.org/10.1021/ma061828u.
- Serbutoviez, C., et al. (1996) Polymerization-induced phase separation. 2. Morphology of polymer-dispersed liquid crystal thin films. Macromolecules, 29, pp. 7690–7698. doi.org/10.1021/ma960293.
- Phillip, W. A., et al. Diffusion and flow across nanoporous polydicyclopentadiene-based membranes. ACS Applied Materials Interfaces, 1, pp. 472–480. https://doi.org/10.1021/am8001428.
- Watson, B. L., et al. (2017) Scaffold-reinforced perovskite compound solar cells. Energy & Environmental Science, 10, pp. 2500–2508. doi.org/10.1039/C7EE02185B.
- Meng, J., et al. (2017) Scaffold-reinforced perovskite compound solar cells. Energy & Environmental Science, 10, pp. 2500–2508. doi.org/10.1039/C7EE02185B.
- Albertus, P., et al. (2018) tatus and challenges in enabling the lithium metal electrode for high-energy and low-cost rechargeable batteries. Nature Energy, 3, pp. 16–21. doi.org/10.1038/s41560-017-0047-2.
- Bruce, P. G., et al. (1988) Conductivity and transference number measurements on polymer electrolytes. Solid State Ionics, 28, pp. 918–922. doi.org/10.1016/0167-2738(88)90304-9.
- Diederichsen, K. M., et al. (2017) Promising routes to a high Li+ transference number electrolyte for lithium ion batteries. ACS Energy Letters, 2, pp. 2563–2575. doi.org/10.1021/acsenergylett.7b00792.
- Timachova, K., et al. (2015) Effect of molecular weight and salt concentration on ion transport and the transference number in polymer electrolytes. Macromolecules, 48, pp. 7882–7888. doi.org/10.1021/acs.macromol.5b01724.
- He, M., et al. (2015) Fluorinated electrolytes for 5-V Li-ion chemistry: probing voltage stability of electrolytes with electrochemical floating test. Journal of The Electrochemical Society, 162, pp. A1725–A1729. doi.org/10.1149/2.0231509jes.
- Randau, S., et al. Benchmarking the performance of all-solid-state lithium batteries. Nature Energy, 5, pp. 259–270. doi.org/10.1038/s41560-020-0565-1.
- Duan, H., et al. (2019) Extended electrochemical window of solid electrolytes via heterogeneous multilayered structure for high-voltage lithium metal batteries. Advanced Materials, 31, p. 1807789. doi.org/10.1002/adma.201807789.
- Yu, X., et al. (2020) Selectively wetted rigid-flexible coupling polymer electrolyte enabling superior stability and compatibility of high-voltage lithium metal batteries. Advanced Energy Materials, 10, p. 1903939. doi.org/10.1002/aenm.201903939.
- Lopez, J. et al. (2018) A dual-crosslinking design for resilient lithium-ion conductors. Advanced Materials, 30, p. 1804142. doi.org/10.1002/adma.201804142.
- Zhang, W., et al. (2018) A durable and safe solid-state lithium battery with a hybrid electrolyte membrane. Nano Energy, 45, pp. 413–419. doi.org/10.1016/j.nanoen.2018.01.028.
- Wang, C., et al. (2019) Solid-state plastic crystal electrolytes: effective protection interlayers for sulfide-based all-solid-state lithium metal batteries. Advanced Functional Materials, 29, p. 1900392. doi.org/10.1002/adfm.201900392.
- Sun, J., et al. (2021) Hierarchical composite-solid-electrolyte with high electrochemical stability and interfacial regulation for boosting ultra-stable lithium batteries. Advanced Functional Materials. 31, p. 2006381. doi.org/10.1002/adfm.202006381.
- Yao, P., et al. (2018) PVDF/palygorskite nanowire composite electrolyte for 4 V rechargeable lithium batteries with high energy density. Nano Letters, 18, pp. 6113–6120. doi.org/10.1021/acs.nanolett.8b01421.
- Fu, C., et al. (2020) A dual-salt coupled fluoroethylene carbonate succinonitrile-based electrolyte enables Li-metal batteries. Journal of Materials Chemistry A, 8, pp. 2066–2073. doi.org/10.1039/C9TA11341J.
- Mackanic, D. G., et al. (2019) Decoupling of mechanical properties and ionic conductivity in supramolecular lithium ion conductors. Nature Communications, 10, p. 5384. doi.org/10.1038/s41467-019-13362-4.
- Fu, C., et al. (2020) Universal chemomechanical design rules for solid-ion conductors to prevent dendrite formation in lithium metal batteries. Nature Materials, 19, pp. 758–766. doi.org/10.1038/s41563-020-0655-2.
- Xia, S., et al. (2019) High-rate and large-capacity lithium metal anode enabled by volume conformal and self-healable composite polymer electrolyte. Advanced Science, 6, p. 1802353. doi.org/10.1002/advs.201802353.
- Liu, Y., et al. (2016) Lithium-coated polymeric matrix as a minimum volume-change and dendrite-free lithium metal anode. Nature Communications, 7, p.10992. doi.org/10.1038/ncomms10992.
- Chen, T., et al. (2018) Ionic liquid-immobilized polymer gel electrolyte with self-healing capability, high ionic conductivity and heat resistance for dendrite-free lithium metal batteries. Nano Energy, 54, pp. 17–25. doi.org/10.1016/J.NANOEN.2018.09.059.
- Lu, Q., et al. (2017) Dendrite-free, high-rate, long-life lithium metal batteries with a 3D cross-linked network polymer electrolyte. Advanced Materials, 29, p. 1604460. doi.org/10.1002/adma.201604460.
- Dong, T., et al. (2018) A multifunctional polymer electrolyte enables ultra-long cycle-life in a high-voltage lithium metal battery. Energy & Environmental Science, 11, pp. 1197–1203. doi.org/10.1039/C7EE03365F.