Synthesis gas, also known as syngas, is a fuel gas that contains a combination of carbon monoxide, hydrogen, and occasionally carbon dioxide. Its name stems from its utilization in the synthesis of important chemicals such as methanol and ammonia and the production of synthetic natural gas (SNG).
Additionally, it is a key intermediate in the Direct Reduction Iron (DRI) process, which reduces iron oxide to iron with the use of natural gas. With 50% of the energy density of natural gas, syngas cannot be burnt directly,¹ but it can be converted into various energy products.
Examples include synthetic petroleum production via the Fischer-Tropsch process and bioethanol production from biomass gasification. Syngas may be produced from a broad range of carbon-containing sources, such as coal, natural gas, organic waste, and wood.
The carbon source is reacted with carbon dioxide (dry reforming), steam (steam reforming), or oxygen (partial oxidation). Figure 1 displays some examples of sources and uses of syngas.

Figure 1. Examples of sources and uses of syngas. Image Credit: Thermo Fisher Scientific – Environmental and Process Monitoring Instruments
The chemical composition of syngas differs considerably depending on the carbon source and the process utilized to produce the desired intermediate.
The chemical processes that use syngas are usually multi-stage, have a variety of gas analysis needs, and are typically dynamic, i.e., they are dependent on process gas analysis for optimization. Rapid, multi-component, multistream gas analysis is a crucial element for efficiently controlling such processes.
Process Analytical Requirements
Carbon monoxide and hydrogen are always present in syngas, but depending on the process involved, they may be present in broadly different concentrations. A wide variety of other chemicals may also be present, and analysis of these is required for an efficiently controlled process and for the desired products to be generated.
These include carbon dioxide, methane, and other hydrocarbons and may also include nitrogen, ethanol, helium, and argon. Examples of the analytical requirements for some of the main syngas processes are discussed below, with Thermo Scientific™ Process Mass Spectrometers holding a strong track record in all these applications.
Ammonia Synthesis
Steam and natural gas undergo numerous processes to transform the hydrocarbon stream into a hydrogen-rich stream. This hydrogen is subsequently reacted with nitrogen from the air in a ratio of 3:1 to generate ammonia.
Eleven or more process streams need to be analyzed, and gas analysis mass spectrometry’s combination of speed, multi-component analysis, and dynamic range enables one MS to analyze all the process streams.
For instance, it is crucial to provide the complete composition of the natural gas feed stream to establish the volume of steam needed to react with methane and the other present hydrocarbons; this parameter is the steam-to-carbon ratio.
Through monitoring the complete composition of natural gas, the costs of steam generation may be minimized by controlling the volume of steam to match the composition of the natural gas.
Table 1 shows an example of Prima PRO’s specification for one of the key ammonia process streams, syngas feed to the ammonia converter. Analysis time, inclusive of stream switching, is approximately 20 seconds, and precision is measured over eight hours.
Table 1. Prima PRO analytical specification for ammonia process syngas analysis. Source: Thermo Fisher Scientific – Environmental and Process Monitoring Instruments
Component |
Concentration vol.% |
Precision absolute % |
Hydrogen |
65.0 – 70.0 |
0.02 |
Methane |
3.0 – 10.0 |
0.01 |
Helium |
0.5 – 1.0 |
0.002 |
Nitrogen |
20.0 – 26.0 |
0.01 |
Argon |
0.1 – 5.0 |
0.002 |
At this point in the process, carbon monoxide has been removed from the syngas as it poisons the ammonia catalyst. Thermo Scientific™ Prima PRO conducts an analysis of all five components, including helium and argon.
The ammonia converter stream is recycled to increase the production of ammonia. This also increases the concentration of helium and argon. If their concentrations are too high, then the energy utilized for compression is wasted, and the ammonia yield is decreased.
The prices of raw materials are heavily impacted by the demand for power generation and heating fuels, and downstream fertilizer prices are impacted by economic, political, and environmental aspects. This places pressure on the ammonia production unit to maximize efficiency, and process analytical data plays a vital part in this.
The process analyzer requires a broad dynamic range to monitor methane slippage (the decrease in methane concentration from over 90% in natural gas to a few percent in the secondary reformer effluent) and rapid yet accurate measurement of both the steam-to-carbon ratio and the hydrogen-to-nitrogen ratio.
Ideally, syngas consists of 75% hydrogen and 25% nitrogen; in practice, it will also contain residual methane and inerts from the air. For optimum efficiency, it is essential to maintain the ratio of hydrogen and nitrogen to be as close as possible to the stoichiometric ratio of 3:1.
Prima PRO has a strong track record in fulfilling all of the above requirements.
Direct Reduction Iron
Iron is traditionally produced in blast furnaces, using coke to reduce iron ore. DRI does not require large stocks of coal to be converted to coke; instead, natural gas is converted to syngas, and iron oxide is reduced by carbon monoxide and hydrogen.
These ‘reducing’ gases are produced by the reaction of natural gas (methane) with the by-products of the DRI process:
CH₄ + CO₂ → 2CO + 2H₂
CH₄ + H₂O → CO + 3H₂
Global DRI production increased from 78 million tonnes in 2016 to 111 million tonnes in 2019 and only reduced slightly to 104 million tonnes due to the COVID pandemic. Blast furnaces still produce the majority of the world’s iron, but production has continued to be relatively flat at approximately 1,300 million tonnes.²
Several process stages are involved (typically eight to ten), similar to the ammonia process, and process MS provides the ability to quickly monitor all process streams fully. An example of Prima PRO’s specification for the DRI syngas stream, typically named ‘Reformed Gas’ in the industry, is displayed in Table 2.
Table 2. Prima PRO analytical specification for direct reduction iron syngas analysis. Source: Thermo Fisher Scientific – Environmental and Process Monitoring Instruments
Component |
Concentration vol.% |
Precision absolute % |
Hydrogen |
~ 58 |
0.05 |
Methane |
~ 1 |
0.01 |
Carbon monoxide |
~ 38 |
0.05 |
Nitrogen |
~ 1 |
0.05 |
Carbon dioxide |
~ 2 |
0.01 |
Analysis time, including stream switching, is approximately 20 seconds, with precision measured over eight hours.
For the DRI process to operate efficiently, rapid but accurate online monitoring is required of several gas streams containing numerous combinations of methane, hydrogen, carbon dioxide, carbon monoxide, and nitrogen over a broad range of concentrations.
Prima PRO has a strong track record of delivering the best combination of accuracy and speed in comparison to other methods of gas analysis, such as gas chromatographs or infrared analyzers.
It optimizes the DRI process by enhancing the generation of reducing gases, optimizing fuel gas mixing, and decreasing energy consumption.
Biomass Gasification
Biomass is usually reacted at temperatures exceeding 700 °C without combustion, with a controlled volume of steam and/or oxygen to generate syngas.
This may be utilized directly as a fuel (which is more efficient than direct combustion of the original biomass) or to generate biofuels using microorganisms to convert carbon monoxide and hydrogen to ethanol.
Thermo Scientific™ Prima BT and Prima PRO Mass Spectrometers have been utilized in a wide variety of processes involving biomass. An example of a performance specification for a syngas-based bioethanol process is displayed in Table 3.
Analysis time, inclusive of stream switching, is approximately 22 seconds, with precision being measured over eight hours.
A Prima PRO was utilized to assess the conversion of syngas and other gas mixtures into alcohols in continuously gassed batch cultivation experiments. Carbon monoxide was identified as the preferred electron and carbon source for the growth and production of alcohols.
However, the total yield of moles of carbon (mol-C) per electrons consumed was nearly identical across all setups, which highlights electron availability as the key aspect influencing product formation.³
Prima PRO delivers a rapid, linear, and reproducible measurement of alcohols such as ethanol; alcohol measurement is very reproducible with its magnetic sector analyzer, and the measurement of ethanol may be measured with high precision at concentrations as low as 10ppm.
Additionally, the Prima PRO offers valuable, reliable composition data on other species present in the process, such as nitrogen, hydrogen, oxygen, carbon dioxide, and argon.
Table 3. Prima PRO analytical specification for syngas based bioethanol process. Source: Thermo Fisher Scientific – Environmental and Process Monitoring Instruments
Component |
Concentration vol.% |
Precision absolute % |
Hydrogen |
~ 60 |
0.05 |
Methane |
~ 1 |
0.005 |
Carbon monoxide |
~ 10 |
0.05 |
Nitrogen |
~ 20 |
0.05 |
Carbon dioxide |
~ 10 |
0.01 |
Argon |
~ 1 |
0.002 |
Ethanol |
~ 1 – 5 |
2% relative |
Gas-to-Liquid Process Using Fischer-Tropsch
Breakthroughs in synthetic fuel, such as the Fischer–Tropsch GTL process, stemmed from the desire to be ‘petroleum independent’ following a national threat of war, crisis, or oil embargo.
At present, synthetic fuel catalyst research has expanded to thermochemical methods for converting anthropogenic carbon dioxide as intermediates for fuel and chemical production.
Along with the future developments in carbon dioxide capture from the environment and renewable energy, this provides encouraging solutions to mitigate anthropogenic carbon dioxide increases.⁴
The two key components of a GTL plant are:
- A steam reformer to react natural gas with steam for the generation of syngas that is rich in carbon monoxide and hydrogen. Natural gas feed is observed to determine the ratio of steam to carbon.
A complete composition analysis is necessary to establish the volume of steam needed to react with the methane and other hydrocarbons present in natural gas.
- A Fischer-Tropsch reactor for the conversion of carbon monoxide and hydrogen into liquid hydrocarbons. The reactor requires the H₂/CO ratio to be 2:1, but the steam reformer usually produces a ratio of approximately 5:1. Any excess hydrogen must be removed, and gas analysis is utilized to control this removal.
Excess hydrogen is utilized as fuel for the reformer or as a fuel or feedstock for an alternative process on an adjoining plant. Analysis of this gas is also required, and if it is to be utilized as fuel for the reformer, then its air requirement and calorific value must be monitored.
The light gas outlet of the Fischer-Tropsch reactor also requires monitoring as this is recycled using the reformer.
There are various types of Fischer-Tropsch reactors, such as fluidized-bed, fixed-bed, and slurry-phase reactors. Prima PRO offers a rapid, precise, and complete analysis of all significant gaseous components in all process streams.
Table 4. Example of Prima PRO analytical specification for Fischer-Tropsch GTL process. Source: Thermo Fisher Scientific – Environmental and Process Monitoring Instruments
Component |
Concentration vol.% |
Precision absolute % |
Hydrogen |
Balance |
0.05 |
Methane |
5.5 |
0.01 |
Carbon Monoxide |
15 |
0.05 |
Nitrogen |
2 |
0.02 |
Ethene |
0.3 |
0.002 |
Ethane |
0.3 |
0.002 |
Argon |
1 |
0.002 |
Propene |
0.3 |
0.002 |
Carbon Dioxide |
10 |
0.01 |
Propane |
0.3 |
0.002 |
Butene |
0.2 |
0.002 |
N-Butane |
0.2 |
0.002 |
Pentene |
0.15 |
0.002 |
N-Pentane |
0.15 |
0.002 |
Hexene |
0.15 |
0.002 |
Not all components are measured in every type of sample stream, but Table 4 displays a typical Prima PRO performance specification for a Fischer-Tropsch GTL process. Analysis time is 30 seconds, including stream switching time, with precision measured over eight hours.
One Prima PRO instrument is able to analyze several gas samples; it delivers a rapid, precise, and complete analysis of all significant gaseous components, including inorganics such as oxides of carbon and hydrogen to hydrocarbons from C₁ up to C₆.
In some processes, H₂S is analyzed at ppm levels to observe natural gas being desulfurized.
Prima PRO’s detailed natural gas composition data is utilized to reduce the costs of steam generation by controlling steam production to fit the natural gas composition.
Reformer outlet stream composition is utilized for the optimization of the reformer, and the Fischer-Tropsch reactor’s light gas outlet also requires monitoring as it is recycled via the reformer.
Additionally, Prima PROs are being utilized to improve and advance processes through the evaluation of the performance of various catalysts in both the reformer and the Fischer-Tropsch reactor.
Benefits of Magnetic Sector Mass Spectrometry
Two main types of mass spectrometers may be utilized for process gas analysis, with the magnetic sector MS offering better stability and precision than the quadrupole MS. The quadrupole generates a Gaussian peak, dissimilar to the flat-topped peak produced by the magnetic sector.
This means it is ‘fault sensitive,’ i.e., any shift in the mass scale will cause an error in the peak height measurement by measuring intensity on the shoulder of the peak instead of the peak maxima. This needs to be corrected by increasing the frequency of calibration.
Figure 2 presents a schematic of the magnetic sector analyzer, combined with the characteristic flat-top peaks it generates.
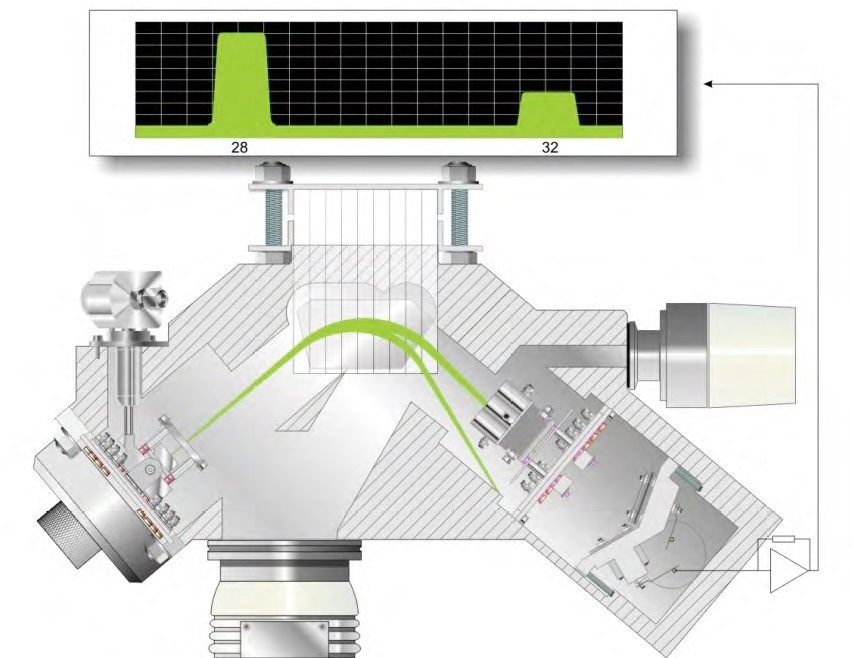
Figure 2. Schematic of Thermo Scientific™ Magnetic Sector Analyzer and flat-topped peaks for mass 28 (nitrogen) and mass 32 (oxygen). Image Credit: Thermo Fisher Scientific – Environmental and Process Monitoring Instruments
Table 5 displays the magnetic sector analyzer’s capability of running for long periods without calibration and still meeting the demands of the performance specification. On a customer site, a Prima PRO had been running for eight months without calibration.
It was subsequently utilized for analysis of a 16-component certified calibration cylinder for 11 consecutive analyses. The analyzer remained within specification, and the user is confident the MS could run for up to a year without calibration being required.
Table 5. Example of Prima PRO calibration check after 8 months without calibration. Source: Thermo Fisher Scientific – Environmental and Process Monitoring Instruments
Component |
Cylinder certified value |
Prima PRO data |
Mean |
Absolute standard deviation |
%RSD |
Helium |
0.2 |
0.196 |
0.001448 |
0.7384 |
Hydrogen |
43.997 |
44.103 |
0.020100 |
0.0456 |
Methane |
10 |
9.961 |
0.001592 |
0.016 |
Carbon Monoxide |
25 |
25.039 |
0.016700 |
0.0667 |
Nitrogen |
2.001 |
1.937 |
0.025400 |
1.3128 |
Ethylene |
0.301 |
0.3 |
0.000689 |
0.2293 |
Ethane |
0.4 |
0.399 |
0.001228 |
0.308 |
Argon |
1.001 |
1.004 |
0.000702 |
0.0699 |
Propylene |
0.299 |
0.292 |
0.001488 |
0.5093 |
Carbon Dioxide |
15 |
14.972 |
0.006544 |
0.0437 |
Propane |
0.5 |
0.498 |
0.000824 |
0.1654 |
Butene |
0.3 |
0.296 |
0.001263 |
0.4271 |
N-Butane |
0.4 |
0.401 |
0.000404 |
0.1008 |
Pentene |
0.2 |
0.2 |
0.000444 |
0.2223 |
N-Pentane |
0.2 |
0.201 |
0.000834 |
0.4155 |
Hexene |
0.1 |
0.101 |
0.000452 |
0.4484 |
N-Hexane |
0.1 |
0.1 |
0.000686 |
0.6841 |
H2/CO Ratio |
1.76 |
1.761 |
0.000991 |
0.0563 |
Independent Tests on Magnetic Sector MS
In accordance with ISO10723, the Prima PRO was tested for fuel gas quality metering in Effectech UK’s ISO17025 accredited laboratory, Calibration of the MS for relative sensitivity was conducted with a single calibration gas containing the nine components displayed in Table 6.
Subsequently, eight different fuel mixes were prepared, containing the same nine components but over a wide range of concentrations, to test the repeatability and linearity of the MS.
Each gas was analyzed for 30 cycles over 5 minutes (10-second cycle time). Figure 3 displays the linearity plots, while Table 7 displays the Coefficients of Determination (R²) for the nine components.
Table 6. ISO 17025 accredited calibration gas used for relative sensitivities. Source: Thermo Fisher Scientific – Environmental and Process Monitoring Instruments
Component |
Concentration %mol |
Nitrogen |
9.00 ± 0.0150 |
Carbon dioxide |
5.00 ± 0.0150 |
Methane |
9.00 ± 0.0200 |
Ethane |
5.00 ± 0.0130 |
Propane |
10.00% 0.0250 |
Ethylene |
5.00 ± 0.0015 |
Propene |
5.00 ± 0.0130 |
Hydrogen |
43.00 ± 0.0700 |
Carbon monoxide |
9.00 ± 0.0150 |
Table 7. Coefficients of Determination for nine components shown in Figure 3. Source: Thermo Fisher Scientific – Environmental and Process Monitoring Instruments
Linearity Test: Coefficients of Determination (R²) |
H2, CH4, C2H4, C2H6, C3H6 |
1.0000 |
C3H8 |
0.9999 |
CO2 |
0.9995 |
CO, N2 |
0.9994 |
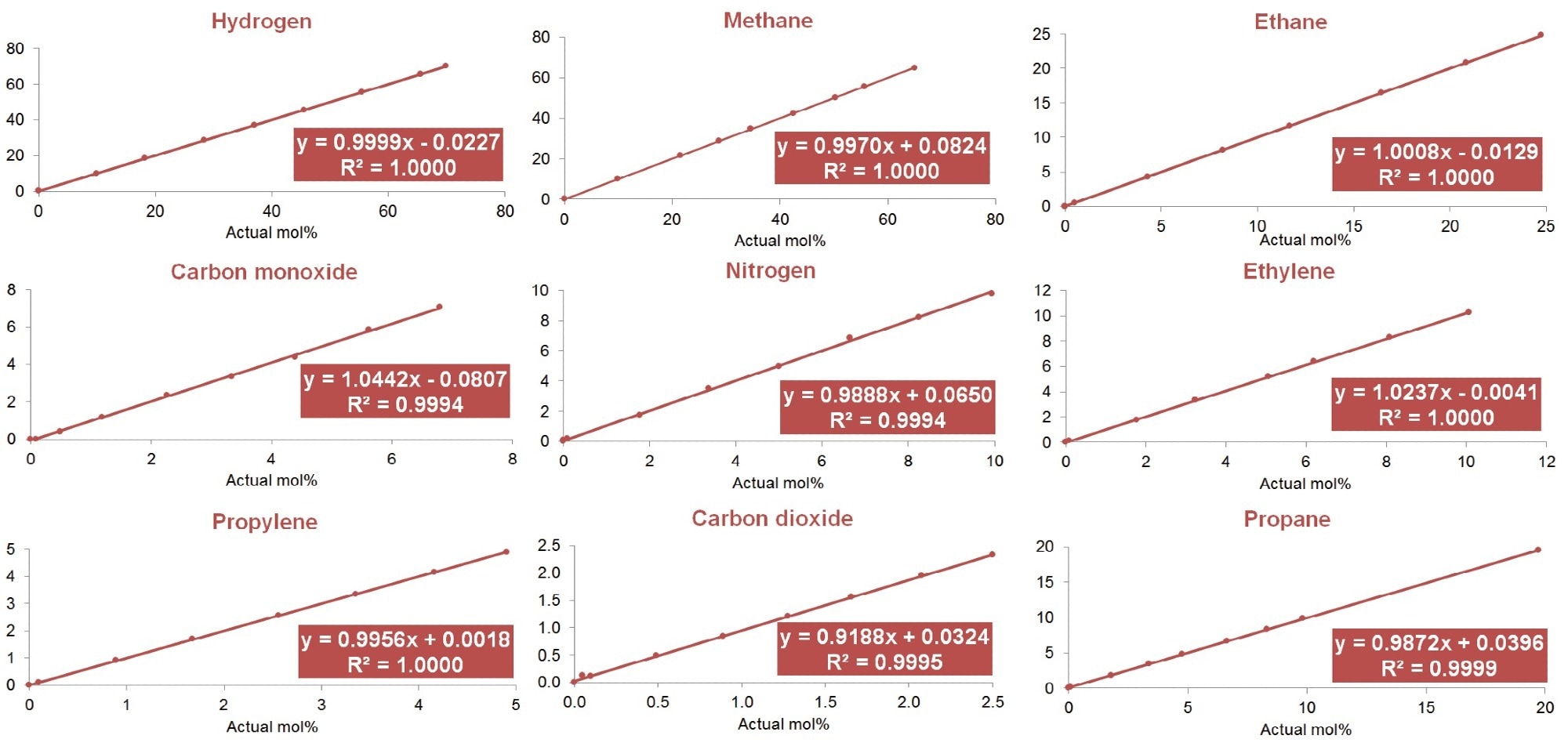
Figure 3. Linearity data for nine fuel gas components. Image Credit: Thermo Fisher Scientific – Environmental and Process Monitoring Instruments
Rapid Multistream Sampling
For the MS to monitor all process streams, a quick, reliable method of switching between streams is necessary. Since rotary valves have poor reliability and solenoid valve manifolds have too much dead volume, the unique RMS Rapid Multistream Sampler was developed.
It provides a superior combination of reliability and sampling speed and enables sample selection from either one of 32 or one of 64 streams. Stream settling times depend on the application and are fully configurable by the user.
The RMS includes digital sample flow recording for every chosen stream. This may be utilized to trigger an alarm if the sample flow decreases, such as when a filter in the sample conditioning system becomes blocked.
The Prima PRO RMS may be heated to a temperature of 120 °C, and the location of the stream selector is optically encoded for reliable, software-controlled stream selection. Position and temperature control signals are communicated using the internal network of Prima PRO.
Figure 4 displays a schematic of the RMS. The RMS has a three-year warranty as standard, with no alternative multistream sampling devices offering the same level of proven reliability.
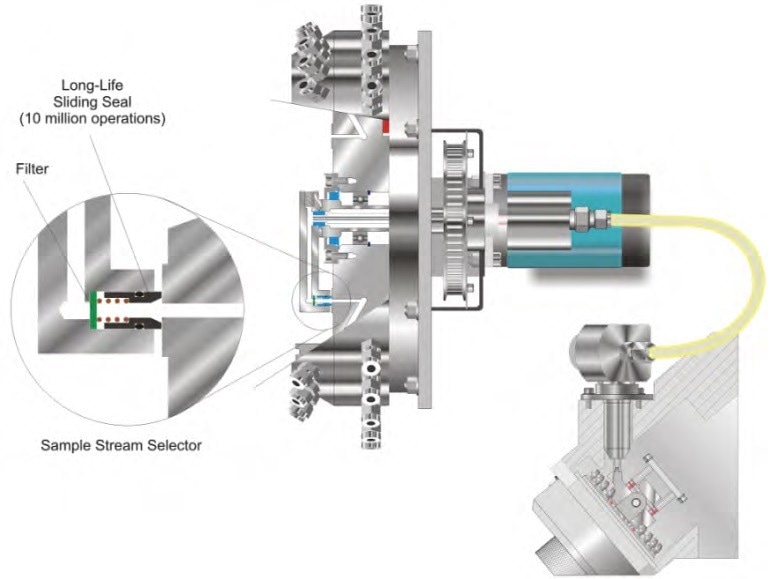
Figure 4. Rapid multistream sampler. Image Credit: Thermo Fisher Scientific – Environmental and Process Monitoring Instruments
Software
Thermo Scientific™ GasWorks™ Software supports the analysis of an unlimited quantity of components per stream as well as an unlimited quantity of user-defined calculations (named Derived Values), such as the ratio of hydrogen-to-carbon monoxide.
An unlimited quantity of analytical methods may be set up, enabling different analyses to be defined for different process streams. Analog signals from pressure and temperature sensors may also be logged, displayed, and utilized in calculations of Derived Values.
A variety of industry-standard protocols are available for communication with plant process control systems.
Performance Specification
There is no single composition specification for syngas. However, Table 8 provides a ‘typical’ Prima PRO syngas performance specification.
Analysis cycle time is around 20 seconds, inclusive of stream settling time, and performance is demonstrated during on-site commissioning by periodic analysis with a certified calibration gas over 16 hours. Additional components may also be monitored if required, with a consultation with the manufacturers advised.
Table 8. Example of typical Prima PRO syngas performance specification.Source: Thermo Fisher Scientific – Environmental and Process Monitoring Instruments
Component |
Range %mol |
Prima PRO precision %mol |
Prima PRO Lower Detection Limit %mol |
Hydrogen |
0 – 75 |
≤0.05 |
≤0.01 |
Carbon Monoxide |
0 – 25 |
≤0.05 |
≤0.3 |
Carbon Dioxide |
0 – 25 |
≤0.02 |
≤0.01 |
Methane |
0 – 10 |
≤0.02 |
≤0.01 |
Nitrogen |
0 – 50 |
≤0.05 |
≤0.3 |
Summary
Syngas production requires rapid, multi-component, multistream gas analysis, and Thermo Scientific gas analysis mass spectrometers are being utilized for rapid, accurate analysis of a wide variety of syngas-based processes:
- Direct Reduction Iron
- Production of ammonia and methanol
- Biofuels
- GTL process via Fischer-Tropsch
The magnetic sector analyzer delivers good long-term stability and high precision, with lengthy periods between calibration and exceptional contamination resistance.
Thermo Scientific Prima PRO and Prima BT Magnetic Sector Mass Spectrometers are delivering rapid but precise off-gas analysis through laboratory research to trial plant and full-scale production for this crucially important industry.
Prima BT offers a bench-top solution for monitoring on a laboratory scale, configured with six calibration and 15 sample gas inlets.
Prima PRO is able to monitor over 60 sample streams and is available for Zone 1 and Class 1 Div 2 hazardous area installation. The highly precise and complete gas composition measurements given by both models are straightforward to incorporate into a process control system.
Acknowledgments
Produced from materials originally authored by Daniel Merriman at Thermo Fisher Scientific, Cheshire, UK.
References
- Biofuels UK, What is Syngas? (http://biofuel.org.uk/what-is-syngas.html)
- 2021 World Steel in Figures, page 18, World Steel Association (https://worldsteel.org/wp-content/uploads/2021-World-Steel-in-Figures.pdf)
- Electron availability in CO₂, CO and H₂ mixtures constrains flux distribution, energy management and product formation in Clostridium ljungdahlii, Hermann, Teleki, Weitz, Niess, Freund, Bengelsdorf, Takors, Institute of Biochemical Engineering, University of Stuttgart, Microbial Biotechnology, July 2021 (https://sfamjournals.onlinelibrary.wiley.com/doi/full/10.1111/1751-7915.13625)
- Synthetic Fuel Development, Future Energy (Third Edition) 2020, Pages 561-580 (https://www.sciencedirect.com/science/article/abs/pii/B9780081028865000268)
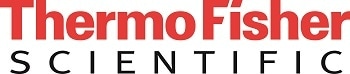
This information has been sourced, reviewed and adapted from materials provided by Thermo Fisher Scientific – Environmental and Process Monitoring Instruments.
For more information on this source, please visit Thermo Fisher Scientific – Environmental and Process Monitoring Instruments.