In this interview, AZoCleantech talks to Thermo Fisher Scientific and CPH2 about renewable hydrogen and how they are teaming up to give it the green light.
Please introduce yourself and tell us about your work at Clean Power Hydrogen.
My name is Bridie Haxby. I am a laboratory supervisor at Clean Power Hydrogen working in the R&D department.
Clean Power Hydrogen (CPH2) manufactures patented membrane-free electrolyzers with cryogenic separation to produce pure hydrogen and oxygen.
The company was founded by Dr. Nigel Williamson and Joe Scott in Ireland in 2012 and established in the UK in 2016. The first demonstrator unit was manufactured in 2018, and from 2012 to 2021, the workforce grew and grew.
I joined in 2020 to test the prototype. The first electrolyzer was installed in Northern Ireland. In 2021, we moved to a more extensive facility.
In 2022, CPH2 floated on the stock market, and since then, it has received 30 million in investment, enabling the technology’s development.
If we look at the electrolyzer economy, the global demand for electrolysis will reach 500 gigawatts by 2050.
CPH2 plans to increase the production of electrolyzers and targets four gigawatts worth of production by 2030, which is 10% of the EU’s hydrogen requirements.
This shows how we can supply green energy input to produce green hydrogen. Applications include transport, powering buildings and industries, and hydrogen storage.
Can you tell us a bit about your projects and collaborations?
We have pilot one-megawatt projects installed and sold globally and two-gigawatt manufacturing and licensing agreements set up with partners in Germany and Northern Ireland.
Our collaborations will assist in the company’s growth and support the hydrogen economy in different parts of the world.
How does the technology work?
Existing stack technologies include proton exchange membranes, membrane-separated alkaline, and solid oxide membrane. These have a membrane, use precious metals, and have a complicated design.
The CPH2 electrolyzer is simple, membrane-free, and does not use precious metals.
Water is fed in, mixed with electrolyte, travels to the stack where the chemical reaction happens, and the gas is generated.
The mixed gas continues its journey to the dryers. Powered by renewable electricity, the stack is fed an electrolyte that contains hydroxide ions dissolved in water.
Water in the electrolyte is consumed by the electrolyzer and separated into hydrogen and oxygen gases by electricity.
The wet gas enters the dryers, the desiccant removes the water from the mixed gas stream, and the gas continues its journey to the cryogen for separation.
The cryogenic system is where the oxygen and hydrogen are separated. The separated gases are passed through the purity meters, where the gas purities are measured, and then they are passed on for use in further applications or storage.
For small installations, the process occurs in a purpose-built container using renewable electricity, producing green hydrogen and medical-grade oxygen.
Using green hydrogen to power and fuel everyday life will accelerate our progress toward a zero-carbon future.
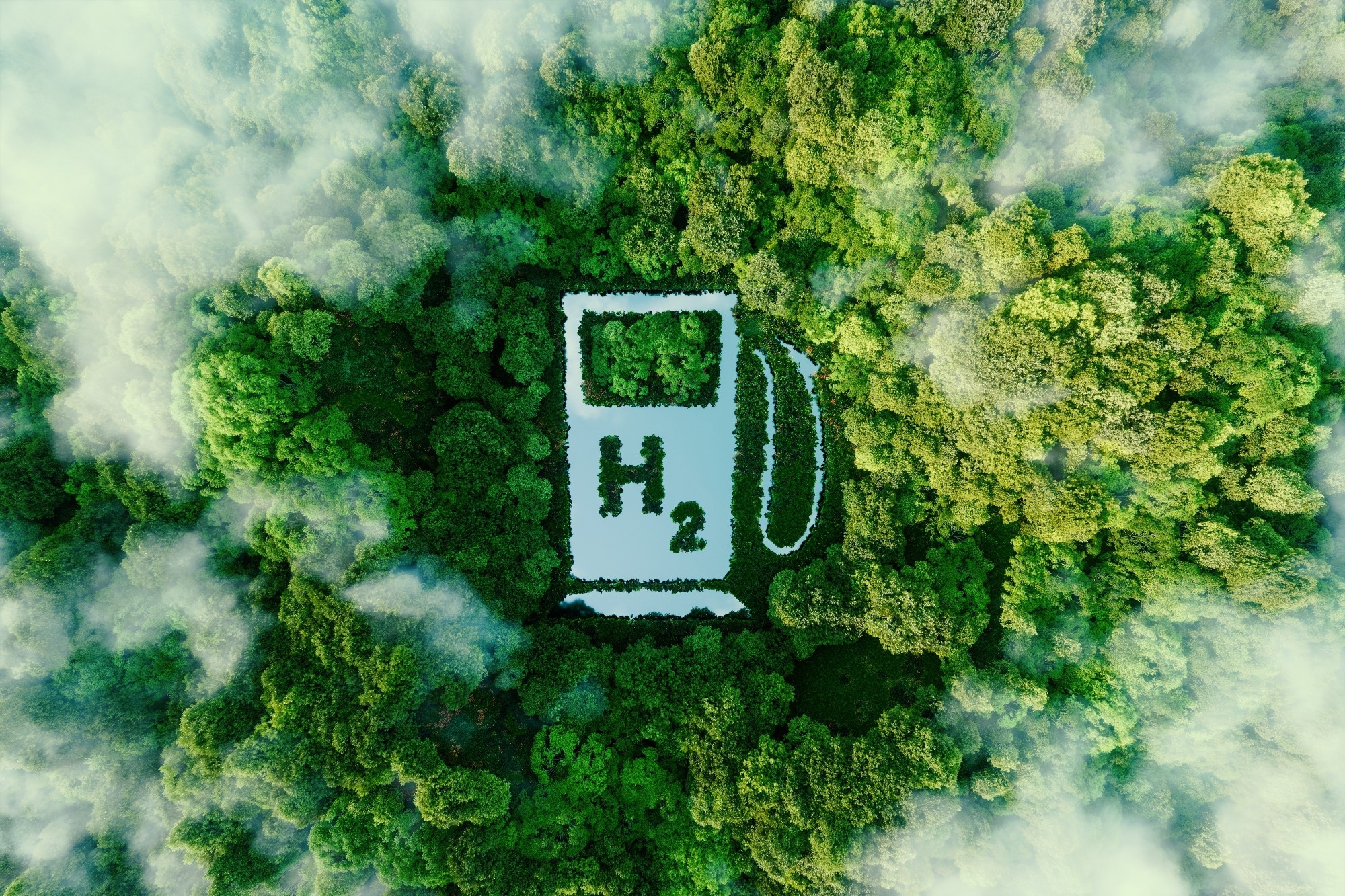
Image credit: shutterstock.com/petrmalinak
How is the CPH2 technology different from other technologies on the market?
The CPH2 technology does not contain precious metals like platinum and has reduced complexity and cost. It is as efficient and responsive to variable input power as proton exchange membrane stacks.
We can output 450 kilograms of hydrogen and 3600 kilograms of oxygen per day from normal water.
The purity of these gases can be tested using the Thermo Scientific Prima PRO Mass Spectrometer supplied by Thermo Fisher.
How can you monitor the electrolyzer process using online mass spectrometry?
Electrolyzer processes can benefit from real-time process monitoring. Mass spectrometry is a technique that can be used in developing and producing clean hydrogen. It provides valuable information on the development and performance of electrolyzers.
It is a very fast and versatile technique that takes just a few seconds per measurement.
It can be used to measure hydrogen, oxygen, and moisture. In addition, it can measure almost any gas in a gaseous phase between concentrations of parts per million and high percentage levels with very linear performance.
Mass spectrometry can monitor most gases in a vapor phase. It does not use separate detectors or other technology to switch between hydrogen, oxygen, and moisture monitoring.
We used mass spectrometry within the CPH2 membrane-free electrolyzers to monitor different sample streams containing mixed gas, hydrogen, or oxygen. Three sample streams are monitored sequentially by a single mass spectrometer. The cycle time for measurement is less than 10 seconds per stream, so it is possible to measure all three sample lines with a cycle time of about 30 seconds.
The performance of the mass spectrometer is excellent. For analysis where the hydrogen is greater than 95%, the precision of the measurement by the online mass spec is better than 0.1% relative, so approximately 200 parts per million standard deviations of the hydrogen measurement.
The water and oxygen can be measured even at low concentrations or trace levels. This mass spectrometer’s detection limit is in the parts per million, so about one and 200 parts per million for oxygen and water, respectively.
Where the sample gas is primarily oxygen, it is at about 99% or higher purity. The precision of the measurement is better than 0.1% relative, so better than 200 parts per million single standard deviations. The detection limits are similar for hydrogen and water in the pure oxygen stream of two to 500 parts per million for water and hydrogen.
Which mass spectrometers did you decide to use for the CHP2 electrolyzers?
We used the Thermo Scientific brand Prima, the fifth generation of mass spectrometers from the Thermo Scientific brand.
There are two types of Prima mass spectrometers. One is designed principally for laboratory installation in a benchtop format. For a more industrial installation, we have the Prima PRO.
They share a common analyzer platform. While they look different externally, internally, they have an identical magnetic sector mass spectrometer. The identical analyzers help with scale-up because applications and experiments developed at the laboratory are easily transferable to the process or industrial scale with confidence that the analyzer will deliver consistent results between development and process.
How does the mass spectrometer work?
There are lots of different types of mass spectrometers. This particular type is a magnetic sector mass spectrometer. When we accelerate ions from the ion source into a magnetic field, they are deflected by the Lorentz force and move in a circular orbit.
The orbit depends on the ion's mass and the flux density or the magnetic field strength and the accelerating voltage. By changing the magnetic field, we can select ions of different masses to enter the detector system.
The magnet is an electrical scanning magnet, an electromagnet rather than a permanent magnet. Ionization occurs by electron impact, the most common ionization method in conventional process mass spectrometers.
Ions are detected using a Faraday detector. The principle of the Faraday is that when positive ions strike the metal surface of the detector, they are discharged, generating an electron flow to an amplifier. The concentration of the sample is proportional to the number of ions that are generated per component.
As the concentration of hydrogen, for example, changes, the number of hydrogen molecules at ionization also changes. The Faraday detector is in effect a means of counting the number of ions of each mass number, hence it is extremely linear. The range of measurement of a Faraday detector, in this instance, is from 10 parts per million up to 100% concentration.
With a magnetic sector mass spectrometer, the magnetic field is varied according to the method programmed into software, ions of selected mass are sequentially directed to the detector for quantification. The "peaks" or signals appear at each mass number as very symmetrical and with a flat top, this is characteristic of magnetic sector technology.
The advantage of having this symmetrical and very flat top peak is that we get a very consistent peak height at the center position, but if you measure slightly off-center, you get the same concentration recorded. It is not necessary to measure the area of the peak because the peak height is directly proportional to concentration. We only measure the size of the peak at the center point.
The mass spectrometer is a highly linear technique. An independent test laboratory has validated this. The laboratory of EffecTech in the UK challenged the mass spectrometer with nine different gas types, each calibrated at a single point. There were up to eight different concentrations in various mixtures that were analyzed by the mass spectrometer, and the data's linearity was plotted. This resulted in almost perfect linearity for all of these gas types.
To monitor multiple sample streams as needed for the three process streams from the CPH2 membrane-free electrolyzers, we have a custom stream selector developed by Thermo Fisher Scientific in front of the mass spectrometer. We call this the Rapid Multi-Stream Sampler, or RMS for short.
At the center, we have a rotating sample arm controlled by a stepper motor. The rotating sample arm picks off any one of 64 sample streams and delivers the selected gas to the ion source of the mass spec. The position of the stream selector sample arm is monitored optically, and the position is fed back to the software so that the analysis method does not begin until the sample arm is sitting at the preferred sample point.
Some stream selectors have fewer sample points. There are 64- and 32-stream versions. The benchtop laboratory process mass spectrometer has a 16-point sample stream selector. To overcome safety concerns when measuring hydrogen and oxygen, either by unwanted mixing or even the sampling of mixed gas streams, users may flow an inert gas such as nitrogen into an unused stream thereby diluting the sample gas to safe concentrations.
There are many analyzers and different methods for measuring the composition of mixed gases and the concentrations of hydrogen and oxygen, including some more straightforward and lower-cost solutions than a mass spectrometer. Why did you decide to go down the mass spectrometry route?
We were looking at gas analyzers to put in our product, but we found the accuracy was lower than we wanted. I looked around to find a more accurate way of measuring the purity of gases, starting by sending a general inquiry out to different suppliers of mass spectrometry, gas chromatography, and even suppliers who visit the site to get gas samples.
The site-visit gas sampling was quite expensive and unreliable - we would not necessarily get a representative sample, and we would have to take many samples.
I looked at getting an in-house instrument. I weighed up between gas chromatography and mass spec, and someone from Thermo Fisher contacted me on LinkedIn to say they had been involved in looking at the crossover of gases in membrane electrolyzers.
After discussing developing this and applying it to our work, I was sure this was the technology we wanted to implement. It was a speedy service. Thermo Fisher wanted to work with us to develop a safe, bespoke product that ticked all the boxes for me. We hired the instrument for a week, where we received training and looked at the software. It was straightforward to set up; from there, we just started using it and getting data.
What challenges did you have to overcome when installing the mass spectrometry?
Making it safe was the main challenge. One benefit was that it had remote access, meaning that we could operate and look at the data from far away.
Another benefit was installing the instrument, as it is plug-and-play. The team set it up, we put the lines in, and we put a nitrogen purge through the sampler and the pump, allowing an inert saturation of the gas mixture to help overcome the explosive risk of the mixed gas.
Once the risk assessment and procedure were implemented, it was simply a case of hooking your laptop up and analyzing the lines. It was straightforward to use after that.
What advantages and disadvantages have you found with the mass spectrometry technology?
When it was commissioned, we hired a Prima BT benchtop mass spec. One of my colleagues used it with me and helped me write a proposal so we could buy the Prima PRO.
When setting up the Prima PRO, we found that going through the initial installation and calibrating using the calibration gases was easy and accessible. You can calibrate it within a couple of minutes. Then getting your vacuum pressure down can take as little as two hours.
Another option is to leave it overnight to get the beneficial effect of the vacuum and then put your lines in and start using it the next day.
The main advantage is that it is easy to use and calibrate. Using the software and analyzing the results was a quick way to implement it into our testing going forward.
Other mass spec applications include looking at the moisture in our gas lines. For example, we needed to know if our dryer was efficient. We can use it to detect if the desiccant is getting saturated because the moisture levels go up.
We could also use the mass spec to purge the system with nitrogen to find traces of hydrogen and oxygen in line. When reading 100% nitrogen, we know those lines are free of mixed gas. This helps with being able to maintain the system, look into the container and make it safe.
How do you plan to utilize gas analysis, either mass spec or any other, in the future? What do you see in the future of analytics at CPH2?
Going forward, I would like to develop a more compact mass spectrometer to analyze the moisture after the dryer before the cryogenic system, measuring hydrogen and oxygen as three streams.
Usually, you would have a moisture meter and two different gas analyzers, but I would like to develop a bespoke mass spectrometer to measure all three and be implemented into our membrane-free electrolyzers.
About Bridie Haxby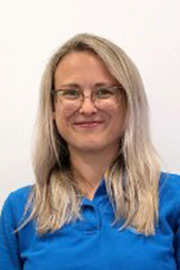
As a lab technician, Bridie Haxby joined Clean Power Hydrogen (CPH2) in March 2020, just before the national lockdown. She was quickly promoted to lead chemist, then lead scientist, and recently promoted to lab supervisor in the R&D department.
Bridie's primary duties are testing the performance of the electrolyzer and how it works in a full system. She's in charge of testing the MFE products by managing a testing schedule to meet the business strategy goals. Bridie provides test data and reports showing how the electrolyzer design meets the standards on the technical specification sheets—discovering new methods to improve the design and performance of the electrolyzers. She is also involved in other exciting projects, such as designing a new R&D test facility and a large-scale test rig.
Bridie Haxby | LinkedIn
About Daniel Merriman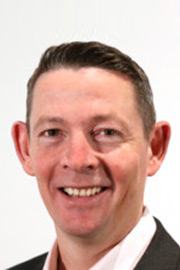
Daniel Merriman has worked in the field of process analytics since joining the former VG Instruments business in 1988 now a part of Thermo Fisher Scientific, holding many positions in technical, sales and marketing – he is now supporting the strategic marketing group within the Environmental and Process Monitoring business of Thermo Fisher Scientific.
Daniel Merriman | LinkedIn
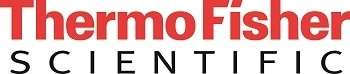
This information has been sourced, reviewed and adapted from materials provided by Thermo Fisher Scientific – Environmental and Process Monitoring Instruments.
For more information on this source, please visit Thermo Fisher Scientific – Environmental and Process Monitoring Instruments.
Disclaimer: The views expressed here are those of the interviewee and do not necessarily represent the views of AZoM.com Limited (T/A) AZoNetwork, the owner and operator of this website. This disclaimer forms part of the Terms and Conditions of use of this website.