The high cost of energy production coupled with the rising awareness of environmental pollution by fuel burning has stimulated companies to optimize production processes for a more cost-effective workflow without compromising on efficiency. One way to do this is to recover heat from industrial processes which produce it. AERZEN has brought out new methods of process heat utilization to provide a long-term reduction in energy costs, which could save up to 90% on energy bills.
With decreasing stocks of fossil fuels and an increasing need for energy in almost every field, renewable technology requires more investment in areas such as solar, wind, geothermal and biologically renewable energy sources. This is also linked to increasing the growth of future markets in target regions of the world. Energy savings from process air generation are especially important as it hits at the heart of industrial lifecycle costs.
In all applications involving compressed air, heat is produced from the electrical energy of the drive power, both as waste heat from the gas compressor, motor and silencer, and by the rise in process gas temperatures. This heat is mostly lost or wasted. However, it can easily be recovered in one of two ways.
Using Cooling Air to Heat Space
Cooling air used to reduce the temperature of the compressor stage, silencer, pipes running through the acoustic hood and the exhaust air of the oil cooler can be used to heat space. The exhaust air (at 30 °C to 60 °C) passes out the waste heat using the same channels in the packaged unit, to spaces which are to be heated, as heating air.
The outlet is temperature-controlled to maintain the room temperature to the set level. After the present heating period, any excess air is vented to the exterior through an exhaust air channel.
Application of Heat Exchangers
Heat can also be recovered using a heat exchanger to draw the stored energy of the compressed gas or other medium. This is a better way in that the heat is pulled into use at the point of production, without having to travel to the final use destination, which leads to energy losses.
In this situation, the compressed medium passes by a heat exchanger through which water is flowing. This water takes up the heat from the compressed medium to reach the preset temperature if the context is that of wastewater treatment plants. Or it may cool down the gas to a temperature of 50 °C or less if a pneumatic application is in view.
In either case, heat transfer must be optimized by planned engineering which considers the speed at which the medium flows through the heat exchanger, the length and surface of the pipe, the type of used materials and the size of the exchanger. These factors decide how much water will be heated and by how much. The heated water could be diverted for use as process water. The fact that most of the hot water goes into the heating system means that over 85% of heat energy is recovered.
Process air generation leads to better energy use and economical operation, but this is often ignored by plant operators. The initial cost of investment (in the form of installation and incorporation into the production cycle) is low, which means the system pays for itself within a few months.
Aerzen is a specialist in heat exchangers, which transmit the greatest amount of heat for the lowest loss of pressure during the process. It can also modify and optimize older air compressors to retrofit them with this aim in view. Aerzen supplies all the equipment, which is another advantage.
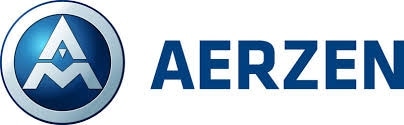
This information has been sourced, reviewed and adapted from materials provided by Aerzener Maschinenfabrik GmbH.
For more information on this source, please visit Aerzener Maschinenfabrik GmbH.