Automation is a key component of modern solar technology manufacturing and enables the industry to scale production, improve quality, and reduce costs. The integration of artificial intelligence, advanced robotics, and digital twin technologies is creating what is described as the "intelligent factory." This growth is demonstrated by the 11 gigawatts (GW) of new solar module manufacturing capacity that came online in the United States during Q1 2024, representing the largest quarter of solar manufacturing growth in American history.1 This expansion demonstrates how automation has become fundamental to meeting increasing global demand while maintaining quality standards.
This article explores how automation has evolved in solar manufacturing, recent technological developments (2023–2024), and its role in supporting next-generation solar technologies and recycling.
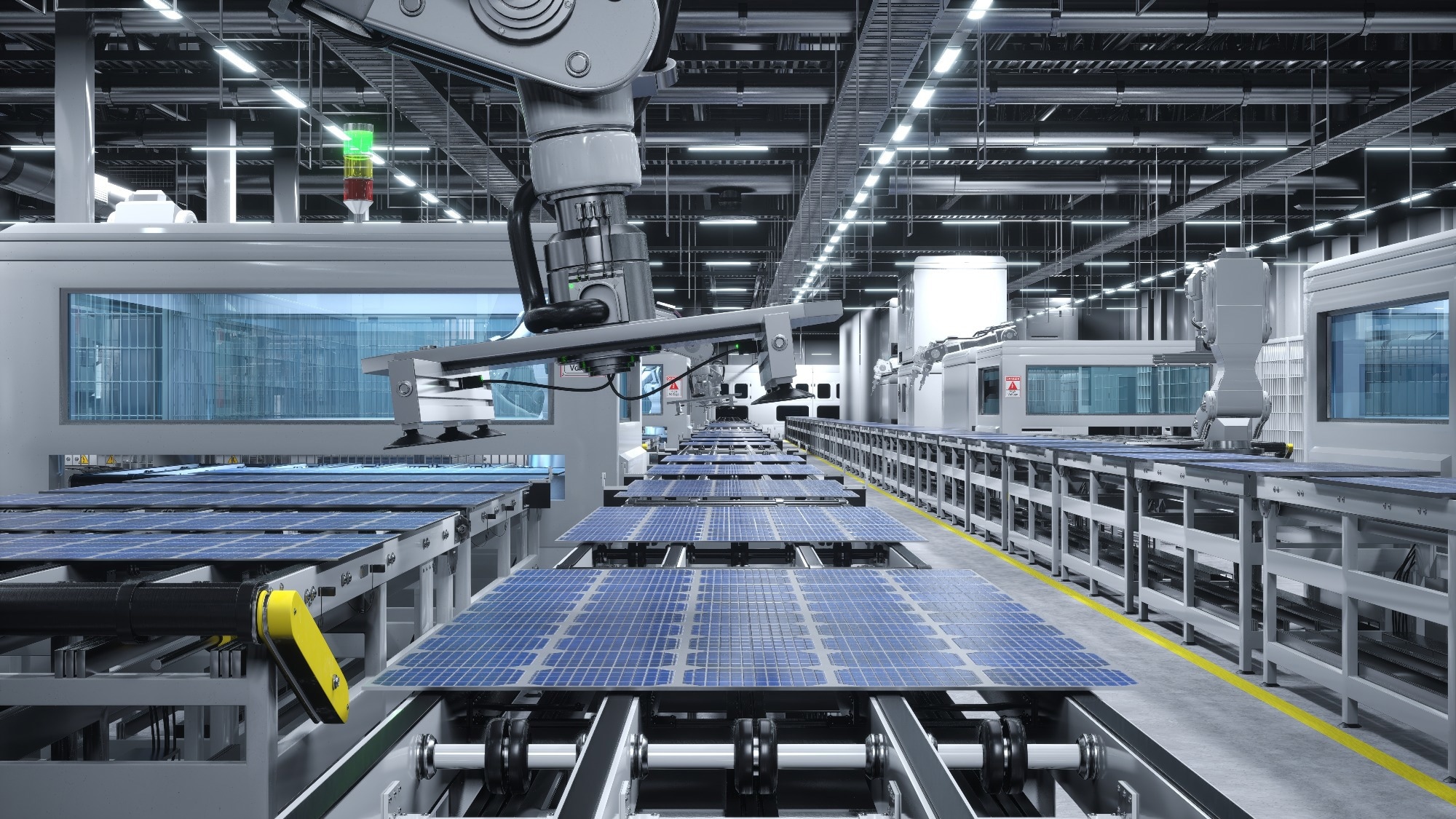
Image Credit: DC Studio/Shutterstock.com
The Path to Automation
Solar manufacturing began in the 1970s and 80s, with largely manual production processes that were slow and costly and resulted in high defect rates. The first wave of automation in the 2000s, driven by rising demand, introduced robotics for specific tasks such as cell handling and stringing. This shift was important for achieving the economies of scale that led to approximately 82-90% drop in solar costs over the following decade, making solar power economically viable. This foundation of automation set the stage for the AI-driven systems being deployed today.2,3
Recent Advances: The Rise of the Intelligent Factory
The principles of Industry 4.0 define the current era of solar manufacturing. Automation is no longer just about performing repetitive tasks but about creating intelligent, self-optimizing production systems. Progress has been concentrated in three key areas.
AI-Driven Process Control and Digital Twins
A recent shift is from reactive defect detection to proactive defect prevention. Manufacturers are increasingly using AI to detect microcracks in finished modules and prevent their formation altogether. This proactive approach involves integrating AI with advanced sensing and prediction technologies to enhance manufacturing and product reliability.
The 'Crack Catcher AI' exemplifies this shift by employing smart stress sensing and fracture prediction to mitigate crack formation in thin silicon cells, which are prone to cracking due to their brittleness and reduced thickness in cost-cutting measures.4
Thousands of Internet of Things (IoT) sensors monitor parameters such as temperature, voltage, and conveyor speed, transmitting data to a central digital twin. Machine learning models analyze this data, identify early signs of process drift, and enable automatic adjustments, supporting the goal of zero-defect manufacturing.5
Download your PDF copy now!
Digital Twins and Intelligent Optimization
AI and machine learning algorithms analyze this data, identifying subtle process drifts or correlations that are invisible to humans. The system can categorize faults, including microcracks, without relying solely on machine learning, allowing immediate alerts and interventions.5
The system then flags these for an engineer or makes micro-adjustments to the process parameters to maintain optimal quality. This approach is central to the concept of zero-defect manufacturing (ZDM), where the goal is to ensure quality is built-in, not inspected-in.
Enabling Next-Generation Technologies
Automation is no longer just making existing technology cheaper; it is the critical enabler for manufacturing next-generation technologies. This is exemplified by efficiency breakthroughs such as perovskite-silicon tandem solar cells achieving records of 34.6%, surpassing the theoretical limits of single-junction silicon cells. These cells utilize the full solar spectrum more effectively, reducing energy loss and enhancing power conversion efficiency.6, 7
Perovskite-Silicon Tandems: These high-efficiency cells are sensitive to atmospheric moisture and require atomic-level precision for manufacturing. Advanced automation is crucial for the precise deposition of perovskite layers, with production pilots using robotic systems to perform multi-layer deposition techniques, such as slot-die coating, inside sealed, and inert-gas environments to prevent degradation.6 The commercialization of these cells relies entirely on such automated manufacturing processes to ensure consistent quality and environmental control.
Advanced Laser Scribing: The interconnection of layers in tandem and thin-film modules involves laser scribing, which must be performed with sub-micron accuracy. Automated systems handle this task consistently, reducing manual errors and improving overall module performance.8
Automation and the Circular Economy
As many solar panels installed decades ago reach end of life, recycling has become a pressing issue. Manual disassembly is slow and expensive, while automated recycling lines offer a potential solution.
Automated Disassembly: Recent research and pilot projects focus on creating automated recycling lines that utilize 3D machine vision to identify the structure of PV panels, enabling precise disassembly. These systems employ robotic arms that remove components such as aluminum frames and junction boxes, reducing manual labor costs and time.9,10 This automated approach addresses the scalability requirements for processing the growing volume of end-of-life solar panels.
Material Recovery: Automation also supports processes like delamination to recover valuable materials, such as silicon and copper. Recovery rates can reach approximately 95% for silicon and 85% for copper.11, 12 Challenges remain in terms of economic feasibility and scaling these processes, but ongoing research aims to address these barriers.
Future Outlook and Conclusion
Current advancements are setting the course for the future of solar manufacturing. By 2030, predictive maintenance is projected to cut downtime by up to 30%, while AI-driven quality control aims to reduce defect rates below 0.1%. Modular and reconfigurable production lines will allow rapid adaptation to new cell technologies and market needs.
Automation is expected to lower production costs by an additional 15–20% by 2028. Autonomous material handling and real-time supply chain optimization will help resolve current bottlenecks. However, fully autonomous factories will need improvements in AI decision-making and clearer standards for human-machine collaboration. Regulatory frameworks must also evolve to address AI-driven quality assurance.
Solar manufacturing has evolved from manual assembly to intelligent, interconnected systems that improve quality, reduce costs, and enable new technologies. The intelligent factory is already taking shape, as shown by record capacity growth and efficiency gains achieved in 2024.
References and Further Reading
- Solar Energy Industries Association. (2024, May 15). American solar panel manufacturing capacity increases 71% in Q1 2024 as industry reaches 200 gigawatts of total installed capacity. https://seia.org/news/american-solar-panel-manufacturing-capacity-increases-71-q1-2024-industry-reaches-200-gigawatt/
- Ritchie, H. (2024, October 2). Solar panel prices have fallen by around 20% every time global capacity doubled. Our World in Data. https://ourworldindata.org/data-insights/solar-panel-prices-have-fallen-by-around-20-every-time-global-capacity-doubled
- Maisch, M. (2020, June 2). Solar costs have fallen 82% since 2010. PV Magazine International. https://www.pv-magazine.com/2020/06/03/solar-costs-have-fallen-82-since-2010/
- Budiman, A. S., Nurmala Putri, D. N., Candra, H., Djuana, E., Sari, T. K., Aji, D. P. B., Putri, L. R., Sitepu, E., Speaks, D., & Pasang, T. (2024). Crack catcher ai – enabling smart fracture mechanics approaches for damage control of thin silicon cells or wafers [Preprint]. SSRN. https://doi.org/10.2139/ssrn.4696629
- Karthik, M., Usha, S., Subha, K., Raja, P. G., Raphel, R., & Thejaswar, M. A. (2024). IoT-based internal fault detection and classification in a solar photovoltaic system. Proceedings of the 2024 International Conference on Intelligent Systems, Computing and Vision (ICICV), 800–807. https://doi.org/10.1109/icicv62344.2024.00133
- Ying, Z., Wang, J., Wang, X., & Ye, J. (2024). Towards the 10‐year milestone of monolithic perovskite/silicon tandem solar cells. Advanced Materials. Advance online publication. https://doi.org/10.1002/adma.202311501
- Wang, H., Lin, W., Wang, Y., Qiu, K., & Yu, X. (2025). Perovskite/silicon tandem solar cells: A comprehensive review of recent strategies and progress. Semiconductor Science and Technology. Advance online publication. https://doi.org/10.1088/1361-6641/adab11
- Aydin, E., Allen, T. G., De Bastiani, M., Razzaq, A., Xu, L., Ugur, E., Liu, J., & De Wolf, S. (2024). Pathways toward commercial perovskite/silicon tandem photovoltaics. Science, 383(6688). https://doi.org/10.1126/science.adh3849
- Peplow, M. (2022). Solar panels face recycling challenge. Chemical & Engineering News, 100(18), 24–28. https://doi.org/10.1021/cen-10018-cover
- Tripathi, A. K., Aruna, M., Thandlam, A. K., Sharma, S., Jhalani, A., & Kumar, R. (2025). Recovery strategies for EoL solar panels: Sustainable and circular economy practices. Green Materials, 1–29. Advance online publication. https://doi.org/10.1680/jgrma.24.00153
- Yadav, R., Singla, A., Ghalwan, M., Mahajan, S., Sharma, P., Mouli, K. C., Vyas, A., & Karthikeyan, R. (2024). Sustainable approaches for recycling solar panel materials: A circular economy perspective. E3S Web of Conferences, 547, 01024. https://doi.org/10.1051/e3sconf/202454701024
- Cheema, H. A., Ilyas, S., Kang, H., & Kim, H.-J. (2023). Comprehensive review of the global trends and future perspectives for recycling of decommissioned photovoltaic panels. Waste Management, 174, 187–202. https://doi.org/10.1016/j.wasman.2023.11.025
Disclaimer: The views expressed here are those of the author expressed in their private capacity and do not necessarily represent the views of AZoM.com Limited T/A AZoNetwork the owner and operator of this website. This disclaimer forms part of the Terms and conditions of use of this website.