Mar 1 2019
Austrian company PET2PET has collaborated with Starlinger to meet the growing demand for recycled material. The joint efforts of the two have resulted in increasing the output by 20%.
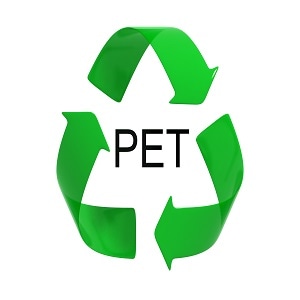
PET2PET located in the east of Austria, processed around one billion PET bottles in 2018 and this marks an increase of nine percent as compared to last year. The five largest domestic beverage producers are responsible for operating the site with the target of recovering recycled material from local sources for reuse in PET bottles. The Austrian brand owners literally stand by the true essence of the buzzword “Circular Economy” because the data reveals that the PET bottles already include 30-50% of recycled material.
Operating Recycling Line with a RecoSTAR PET 125 HC iV+
Since 2010, PET2PET has operated a Starlinger recycling line with a recoSTAR PET 125 HC iV+, with which the pre-cut, washed and sorted flakes are processed into high-quality regranulate. Christian Strasser, Managing Director of PET to PET says: “With Starlinger’s technology, we have chosen one of the safest methods that guarantees thorough decontamination of the material according to the FIFO principle.” He also quoted: “In this regard, the strict requirements of our owners, especially Coca-Cola, greatly influenced our decision when purchasing the line.”
Geographical proximity was also a factor, as Starlinger and PET2PET are located only 30 miles part which allowed short-term spare parts deliveries and swift technical assistance. The recycling of plastics is flourishing these days, and the circular economy package stipulates a recycling rate of 50 % until the year 2025. Last year, PET to PET approached the Starlinger recycling technology with the request for an increase in capacity of the recycling line.
Potential for Improvement to Increase Performance
A detailed analysis helped to identify areas that showed potential for improvement for increasing performance. On the basis of this analysis, Starlinger recycling technology compiled a package that was integrated into the line in several stages. This upgrade comprised of several process steps such as drying, extrusion, filtration, and energy recovery.
Christian Lovranich, Head of Process Engineering of Starlinger recycling technology explains: “After completion of the revamp, the line runs at 20 % more output with consistent quality and constant IV.”
He also stated: “By doubling the capacity for energy recovery, we have not only made the line more productive, but also much more energy-efficient. The successful upgrade at PET to PET shows that even after many years of reliable operation, recycling lines can still achieve an increase in performance.”