Excessive CO2 in the atmosphere significantly contributes to global warming. However, envision a scenario where captured CO2 gets converted into valuable green chemicals—a plausible reality. CO2 electrolysis facilitates this conversion, yet it remains a complex and expensive process.
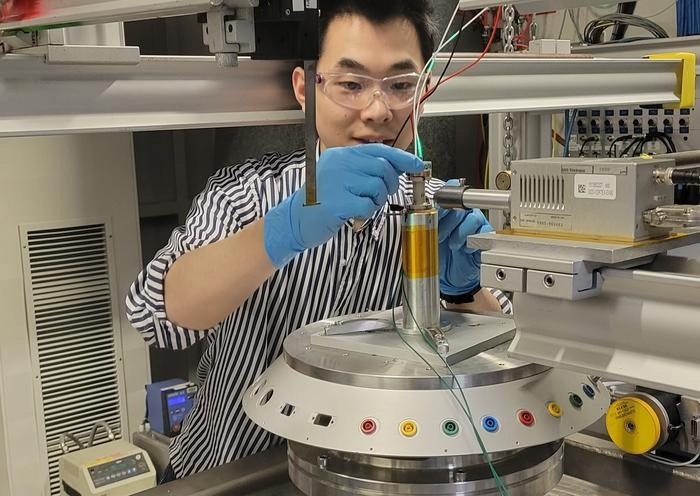
Postdoc Qiucheng Xu, preparing the reactor. Image Credit: Bjørt Oladottir Joensen
Researchers have made significant strides towards a technology capable of converting captured CO2 into valuable green chemicals like ethylene and ethanol. These chemicals hold potential in plastic production, marking a promising step forward.
The majority of today's plastics stem from fossil-based chemicals, contributing roughly 5% to global CO2 emissions. CO2 electrolysis presents a sustainable alternative, utilizing captured CO2 as a resource rather than relying on fossil sources. This technology holds immense promise in facilitating society's shift towards a greener trajectory.
We have found out why and where in the chemical process of electrolysis of CO/CO2 the electrolysis device degrades. Our results provide clear guidelines for researchers and the industry on how to extend the durability of devices for CO/CO2 electrolysis, which will strengthen the commercialization of the technology.
Brian Seger, Professor, Technical University of Denmark
The study results were published in the international journal Nature Catalysis.
Electrolysis Using CO2
Understanding the principles of electrolysis is crucial in appreciating the significance of its outcomes. This process allows for the separation of substances into their elemental components or the creation of new chemical compounds. Electrolysis occurs when an electric current is introduced to an electrolyte, which can be a conductive solution or molten compound.
During electrolysis, positive ions within the electrolyte migrate towards the cathode, while negative ions move towards the anode. For instance, in the electrolysis of water (H2O), the anode within a vessel containing water will attract oxygen (O2), while the cathode will draw in hydrogen (H2), effectively splitting the water into its fundamental elements.
In CO2 electrolysis, the initial output is carbon monoxide (CO). Subsequently, CO electrolysis enables the transformation of CO into valuable chemicals like ethanol (an alcohol usable as fuel) and ethylene (a hydrocarbon essential in producing the plastic material polyethylene).
Durability Increased From Half a Day to 100 Hours
CO2 electrolysis entails a complex, multi-step procedure where various factors influence its efficiency. One significant challenge involves the degradation of the anode within the electrolyte solution, causing device failure after approximately half a day's operation. This limitation renders the process costly and hampers its scalability for industrial applications.
However, promising news emerges from the researchers' success in enhancing the durability of the anode. This breakthrough potentially heralds positive developments for companies engaged in CO2 electrolysis, offering prospects for more sustainable and viable industrial utilization.
The researchers identified a major cause of anode degradation: the production of acetate on the cathode in an alkaline environment. This leads to the formation of acetic acid at the anode, reducing the pH. Anode materials unable to withstand this low pH result in degradation, causing device failure within about 12 hours of use.
By eliminating acetate and maintaining the electrolyte solution's pH, researchers extended the anode's durability from half a day to over 100 hours. Initially achieved through manual replacement of the solution every 12 hours to prevent pH decline, this challenge could potentially be addressed through a straightforward filter once the technology is commercialized.
Our guidelines tell researchers and the industry that they need to monitor the pH value on the anolyte side in order to maintain a pH that does not corrode the anode. This is a simple but crucial point for the companies who are already starting to commercialize the technology.
Brian Seger, Professor, Technical University of Denmark
Journal Reference
Xu, Q., et al. (2023). Identifying and alleviating the durability challenges in membrane-electrode-assembly devices for high-rate CO electrolysis. Nature Catalysis. doi.org/10.1038/s41929-023-01034-y.