Mar 3 2009
Plantic Technologies Limited, manufacturer of starch-based polymers for packaging and other applications, commissioned RMIT University, Melbourne, to undertake a streamlined update of the Life Cycle Assessment (LCA) of Plantic® biodegradable plastic packaging system compared with alternative polymers. The updated LCA reveals that every tonne of Plantic® sheet purchased in place of petrochemical polymers will save up to 2.5 tonnes of carbon dioxide (the average annual emissions of a compact car) and enough energy to power 2.5 average Australian homes.
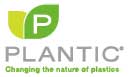
An LCA of Plantic® rigid trays from cradle to grave was first conducted in August 2004 (James and Grant 2004) and was recently updated to incorporate the process changes implemented to Plantic’s production line during that time. The functional unit used for the purpose of this study is the production and disposal of 1000 retail trays used to package chocolates, each 12g in weight.
This updated LCA indicates that when compared to other conventional polymers used in similar tray applications, less than half the energy is required to produce the equivalent number of Plantic® trays. Additionally, Plantic® materials are estimated to have approximately 40-70% less impact on global warming than various petrochemical polymers.
With Easter fast approaching, it is estimated that Easter eggs generate about 3000 tonnes of waste each year. If all of these eggs were packaged in Plantic® material, enough energy would be saved to power 350,000 homes for the Easter period, which is effectively all of the houses in Canberra. It would also save enough carbon to take 140,000 cars off the road in that period. Mr. Brendan Morris, Chief Executive Officer, Plantic Technologies Limited, commented, “We are pleased to note that if disposed of properly in a compost, Plantic’s rigid trays will have considerably less impact on global warming than conventional polymers. And, as this study shows, we are constantly devising new ways to reduce our energy consumption through innovative and streamlined manufacturing processes.
“Ultimately, Plantic’s advanced biopolymer technology provides our customers with sustainablysourced packaging materials that offer a trio of functional, environmental and cost benefits.”
Plantic’s novel polymer manufacturing technology is based on the use of high-amylose corn starch, a material derived from annual harvesting of specialised non-GM (hybrid) corn. The unique chemical and film-forming properties of this type of starch allow for development of a range of applications across conventional plastics markets. The materials are inherently antistatic, offer excellent gas taint and odour barriers and are sealable, printable and laser etchable. Plantic® materials have a renewable bio-content of approximately 85%. In addition to being renewably sourced, Plantic® materials are biodegradable, home compostable, water dispersible and compostable to European (EN 13432) and American (ASTM 6400) standards.